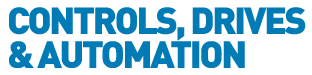
![]() |
Charlotte Stonestreet
Managing Editor |
Home> | POWER TRANSMISSION | >Clutches | >KEEPING TENSION UNDER CONTROL |
Home> | INDUSTRY FOCUSES | >Printing & Packaging | >KEEPING TENSION UNDER CONTROL |
KEEPING TENSION UNDER CONTROL
30 October 2012
This tension release backstop from Renold enables sprag clutches to be operated safely where obstructions might otherwise cause a potentially dangerous build-up of tension in conveyors
A sprag clutch is a freewheel device with an inner race and an outer race, either of which can be the input or output member.
The input member can be arranged to drive the output member in a chosen direction and permit the output member to overrun in the same direction. In general, sprag clutches are able to transmit greater torques than other types of freewheel device, within given overall dimensions.
In simple form, the sprag clutch comprises shaped steel sprags or wedges, located in the annular space between concentric inner and outer races. Power is transmitted from one race to the other by the wedging action of the sprags between them. Each sprag is so shaped that rotation of one race in the ‘driving’ direction causes the sprags to tilt, thus transmitting the torque in full from one race to the other.
Conversely, rotation of the race in the other direction frees the sprags and permits overrunning between the races.
BASIC APPLICATIONS
There are three basic applications for the sprag clutch: overrunning; indexing; and backstopping or holdback.
Overrunning applications often can be found in barring drives or standby drives, where two or more motors drive a machine. The high speed/high power drive being the prime mover, with a secondary drive at lower speed and power connected into the system to provide a slow speed drive for maintenance or other function.
Indexing is an application where accuracy and consistency is required. By linking a reciprocating motion from the prime mover to one race of the sprag clutch the motion is converted to an indexing movement at the other race.
Applications include assembly conveyors, packaging, food and drink and printing machines.
For many years, standard sprag clutch backstops have been successfully used as safety devices to prevent inclined conveyor belts from running back when stopped in a loaded condition. The outer race is attached to the machine frame and the inner race is allowed to rotate in the forward direction. If the machine attempts to backdrive, the sprag clutch will prevent reverse rotation by acting as a holdback. Applications include inclined conveyors, bucket elevators, fan drives and pumps.
In overrunning and backstopping applications, one race of the clutch is required to run at a faster speed than the other. The inner race is always the one that runs at high speed and the outer race at the lower speed.
If the clutch is used as the sole failsafe device in any application, then other factors in the operating environment, such as improper use, lack of servicing maintenance or lubrication may cause the clutch to fail, causing danger to users, personnel and property. In particular, when conveyors stall because of an obstruction between the bottom belt and the return end drum, extreme tension is caused in the top belt as standard sprag clutch holdbacks do not allow the slack bottom belt to ease through the drive.
The release of these obstructions has caused fatal accidents, when the uncontrolled release of tension in the top of the belt rapidly pulls the bottom of the belt around the end drum with a sudden surge of extreme force.
LIMITATION OVERCOME
To overcome this safety limitation Renold has designed a range of tension release backstops, which may be fitted to the gearbox drive shaft to ensure safe controlled release of the built up tension in the top belt. This is achieved through controlled friction slippage of the sprag clutch element of the backstop. In addition to improving workforce safety, this device protects expensive plant against costly repairs and production downtime.
Features of the TRM-I device include automatic torque limiting.
Being a custom-designed device, there are no external dimensional changes to the gear unit. The TRM-I is also designed so that no modifications are necessary to the gear or worm shaft, thus existing field units can be readily converted and no special tools are required to operate them. They are suitable for single or multiple drive applications in the automatic mode and no lengthy preparation time is required prior to operation in the manual mode.
Renold torque limiting backstops have been designed for use in dual drive or tandem drive systems traditionally used on long material handling conveyors, such as are used in steel mills, iron ore handling or coal mines
Key Points
- In general, sprag clutches are able to transmit greater torques than other types of freewheel device
- Three basic applications are: overrunning; indexing; and backstopping or holdback
- Renold has designed a range of tension release backstops, which overcome safety limitations
- Looks Good On Paper
- No Need For Circuit Breakers
- ACCURATE 2D & BARCODING
- No Sensor Readjustment Necessary
- Friction Discs
- Enhanced Performance From Asynchronous Spindle Motors
- High Accuracy
- SWEET SUCCESS OF SINGLE CONTROLLER
- OPENSAFETY STANDARD UNDERPINS NESTLÉ PACKAGING AUTOMATION
- THE ROBOTICS PACKAGE