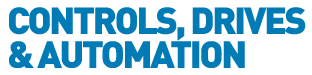
![]() |
Charlotte Stonestreet
Managing Editor |
Home> | IIot & Smart Technology | >IIoT | >Leading by example |
Home> | IIot & Smart Technology | >Industry 4.0 | >Leading by example |
Leading by example
15 December 2021
FANUC Europe President & CEO Shinichi Tanzawa talks to Controls, Drives & Automation about the company’s smart factories, robots building robots and the impressive savings that IoT solutions can generate
CDA: SINCE the start of the COVID-19 pandemic, industry has shown an increased interest in automation, robotics and so-called smart factories with the implementation of many automated and, in some cases, completely unattended processes. How does FANUC feel as the supplier of these solutions?
Shinichi Tanzawa: FANUC is not only a supplier of factory automation products, but for more than 30 years now we have been automating and robotising our own factories. Today our production is almost completely automated and robotised, supported by the analysis of machine data to improve our production processes even further. In fact, at some of our factories, only a handful of people are working while the entire plant runs automatically with machines and robots.
Of the people who work in our factories most are not doing manual labour, but serving as engineers behind the scenes. If any issues occur, they receive an automatic alarm on their phone and can react quickly. When the pandemic began to impact production facilities worldwide, our factories kept running uninterrupted. This fact caught the attention of many people in the manufacturing industry who now fully understand what our company has achieved in the field of automation over the past three decades.
CDA: Your factories are a functional example of next-generation intelligent automated production. Can you explain in a little more detail the origin of this concept; how did its implementation take place?
Shinichi Tanzawa: All FANUC factories are highly automated. As a supplier of automation and robotics we have always strived to fully utilise our own products in our factories. Our motivation is to prove the capability and benefit of FANUC products on the factory floor. We feed all of this information back into our product development, leading to continuous improvements. Today, we are using more than 4000 robots in our own factories. These robots run 24/7 and complete a variety of tasks. For example, at one of our factories, robots are assembling new robots. We are probably the only robot supplier that is fully utilising its own robots as part of its production.
CDA: Is the experience and knowledge gained from the operation of intelligent robot production applicable in other industries?
Our experience of using FANUC equipment to automate our factories is applicable in all manufacturing sectors. In fact, our customer base is very wide and not limited to the metalworking industry. The extent to which factories worldwide have adopted automation to date may be different, but it is clear that demand for automation will continue.
CDA: An important part of smart factory projects is the digitisation and involvement of IoT in production processes and operations. To what extent do your solutions take advantage of these factors?
In order to help customers use production data effectively, we have developed an Industrial IoT platform called FIELD system and many associated IoT software apps; we are also utilising these in our own factories. To provide customers with even more options, we have developed FIELD system as an open platform. This means that not only FANUC, but also third-party app developers and customers can use our IoT platform to develop software solutions for specific production requirements. We know from experience that using IoT solutions in manufacturing quickly leads to higher production efficiency. At present, we are in the process of explaining and proving these advantages to our customers.
CDA: Standardisation will play an important role in the advent of smart factories and the solutions they use. Does Fanuc cooperate in this field with other companies or organisations?
We have some cooperation agreements, such as those with NTT, Fujitsu and certain software development companies, particularly with regard to FIELD system. As a company we already work with many European partners in developing apps and building up the infrastructure for our IoT platform. And we plan to expand this kind of cooperation.
CDA: Generally speaking, how do you see the future of smart factories in practice? So far, with a few exceptions, they have taken place at pilot project level. Do they require significantly more investment and engineering expertise than conventional operations, and will they pay off at all, and in which segments?
We started making our factories smart more than 20 years ago. Today, a wide range of machines and robots in our factories benefit from connecting to FIELD system.
We have gained greatly from this, achieving high product quality and profitability. However, to prove the benefits we are now in the process of implementing our IoT platform and other IoT products at the factories of our customers. The experience we get from these projects will help us to grow our product sales going forward. We see that in the beginning, many customers are fearful of high investment costs, but we believe they will realise impressive savings within a relatively short period. From talking to our customers we already have evidence that this is the case.
- FANUC UK offers free trial of simulation software
- FANUC extends collaborative robot range
- Robot Slims Down & Speeds Up
- FANUC extends handling robot range
- Navigating cobot safety regulation changes
- FANUC to supply Ford plant in Cologne with 500 robots
- Polestar Interactive is first strategic partner for FANUC UK FIELD system
- Fanuc praised for changing perception of industrial automation
- Simpler, more efficient manufacturing automation
- Robot production booming
- Industry 4.0 ready
- Intelligent interlocks
- What operators need to know about IIoT adoption
- Predictive maintenance leader
- The digital future has begun
- The smart future of manufacturing
- Partnership integrates freight & warehouse management
- Secure data handling
- Makes IoT available in practice
- When & where will Industry 4.0 actually happen?