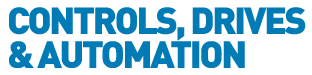
![]() |
Charlotte Stonestreet
Managing Editor |
Home> | POWER TRANSMISSION | >Bearings | >Lowering beverage industry production costs |
Home> | AUTOMATION | >Condition Monitoring | >Lowering beverage industry production costs |
Home> | MACHINE BUILDING & ENGINEERING | >Machinery | >Lowering beverage industry production costs |
Lowering beverage industry production costs
29 November 2023
At BrauBeviale, one of the leading capital goods fairs for the beverage industry worldwide, Schaeffler will be on site with a presentation that focuses on solutions for economical and efficient beverage production.

Ralf Moseberg, senior vice president industrial automation at Schaeffler, comments: “The high cost pressures in the industry also have a positive side effect. Established series solutions are being questioned and the search for new and more efficient designs and solutions is beginning – and increasingly, this includes the entire life cycle of machines and systems. This is very much in line with our solutions for the food and beverage industry, from standard components and engineering to solutions for efficient operation and optimised maintenance.”
Safeguarding the brewing process with the OPTIME Ecosystem
The OPTIME Ecosystem not only provides brewers with an overview of the condition of all pumps and assemblies but also monitors lubricant supply. OPTIME Condition Monitoring (CM) is a system for the automatic monitoring of pumps, electric and geared motors, fans, rolling bearings and other assemblies of the kind often used in the beverage industry. The risk of unscheduled downtime is significantly reduced, which helps to achieve annual targets. Maintenance work can be planned and is more cost-efficient.
OPTIME C1, the first smart, automated lubricator on the market, is part of the OPTIME Ecosystem and uses the same technologies and user interfaces as OPTIME CM. Maintenance personnel are alerted via the Schaeffler OPTIME app about lubricators with a critical fill level, a fault in the lubrication supply and lubrication points with increased temperature.
Energy efficient beverage filling with direct drive systems
Worm gear motors are often used to drive star wheels in beverage filling machines. Although the drive power is just a few kilowatts, the annual losses add up to a considerable amount due to 24/7 operation and the low overall efficiency of 0.73-0.75. A direct drive like the Schaeffler RIB torque drive offers a significantly higher efficiency of 0.92 in this output class. Using this direct drive can save several tens of thousands of euros in energy costs and more than 100 tonnes of CO2 emissions over the life cycle of a single beverage filling line.
For the linear guides used in star wheels, Schaeffler recommends its KUVE-B series monorail guidance systems in combination with the KIT450 long-term lubricating units and a friction-optimised sealing assembly. The uniform distribution of the lubricant in the carriages reduces the amount of lubricant needed. By using these linear guides, operators can save around 50 per cent lubricant and 70% maintenance costs. Service lives of more 50,000 km without relubrication are possible.
Automation and robotics
At its exhibition booth, Schaeffler will use a Kuka IONTEC HO robot with barrel gripper to showcase its RT1 and RT2 series precision strain wave gears and configurable complete drives – known as drive systems – as well as the PSC range of precision planetary gear units. From the linear segment, 7th axes and new lifting columns will also be presented. For the automated transport and handling of bottles, boxes, drums and pallets, Schaeffler offers all bearing components, from simple linear bearings to portal handling and multi-axis systems.
Radial insert ball bearings in plastic housings
Radial insert ball bearing housing units are important components purchased by the beverage industry. Schaeffler offers a total of five housing variants in white plastic: two plummer block, two two-bolt and two four-bolt flanged units. The glass fibre reinforced PBT plastic is FDA-approved and is resistant to moisture, UV radiation, bacteriological and fungal attacks as well as many chemical media. All deep groove ball bearing components in the FD variant are in stainless steel. The allergen-free lubricating grease used in the bearings is approved to NSF category H1, meets the requirements of FDA21 CFR 178.3570, and is certified to halal and kosher standards.
- Cylindrical roller bearings for heavy-duty industrial gearboxes
- Taking monorail guidance systems to the next level
- Bearing solution for vertical lift bridge
- Linear profile rail system replacement
- Innovative solution package for robotics industry
- Schaeffler buys digital CM specialist
- Plummer block housed
- The fight against fake bearings
- Schaeffler OPTIME wins Industry 4.0 Innovation Award
- Deep groove ball bearings