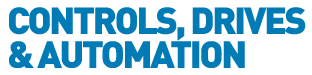
![]() |
Charlotte Stonestreet
Managing Editor |
Home> | IIot & Smart Technology | >Industry 4.0 | >Digitalisation on the menu |
Digitalisation on the menu
29 June 2022
Chris Evans discusses the challenges faced when looking to digitalise a food manufacturing production line or plant and how to overcome them

IMPLEMENTING A smart, digitalised food manufacturing production plant on a green field site should be a relatively straightforward task. However, many food manufacturing plants have evolved over time with their production facilities spanning the entire automation spectrum, from fully automated, through semi-automated and on to ‘not very automated at all.’
The key to digitalisation and smart manufacturing, is the ability to capture data from the asset level about plant performance, down time, energy efficiency and so on. Fundamentally that requirement is the adoption of automation at the asset level and the presence of an Operational Technology (OT) network infrastructure which will capture vital data and be able to analyse it and turn it into real information.
Many plants have good levels of automated assets but find without a site standard, the plant is populated with assets controlled by multiple automation vendor’s equipment. This not only causes extra cost due to carrying multiple spares but can also lead to legacy automation issues further down the line. Understanding where the current plant sits in relation to these requirements is crucial from a planning, budget allocation and return on investment perspective (ROI). The good news is with the right approach, all of these challenges can be overcome, or at least minimised.
Solutions
It is easy to think that digitalising a food manufacturing plant in order to make it a smarter operation should be tackled from the top down. The challenges that typically face us appear to suggest that the best approach would be to focus on the production end of the plant first and as always it is not as straightforward as that.
Firstly, and arguably most importantly, any digitalisation project should consider what success looks like. What improvements are we trying to make and how can we quantify our ROI?
Next, as we have already discussed we must look at the level of automation and network infrastructure that currently exists and whether that meets the needs of the project. Equally, the vision of the final goal should be considered, ultimately how far are we traveling along this road to digitalisation?
With the adoption of open network standards and standard communication protocols, the issue of disparate automation vendors existing at the asset level is not such a problem, providing that the automation vendor chosen at the data capture level, to pull all this data together, supports these standards. Data capture solutions deployed at the Edge layer should be capable of varying degrees of data aggregation and analytics and should offer a scalable and flexible approach to meet the project budget.
It is important to understand what data management system either exists or will exist at the Enterprise or data management level, whether deployed in cloud services or at on premises servers. This will dictate how each of the assets will pass their data to the next level. It is possible to interface directly with the Enterprise level without deploying a data capture solution at the Edge layer, although it can often be false economy to pass multiple unaggregated data points to the Enterprise level as this can be costly and does not operate in real time with the plant.
Successful digitalisation projects, consider the levels of investment required to deliver against the desired outcome, focusing on the automation and network infrastructure required to capture data and a clear plan and methodology which demonstrates how that data is processed, aggregated and delivered back as useful information.
Transforming an existing plant into a smarter, leaner operation is possible with a planned staged approach, challenges can be overcome and significant improvements can be achieved. Discussion and understanding of the objectives is vital in delivering that success.
Chris Evans is vertical industry and projects group manager at Mitsubishi Electric UK
- Is Your Automation Architecture Holding Back Your Business?
- A pressing need for automation
- Energy efficiency - it's a journey, not a destination
- Developer’s kit for machine builders
- HMI for extreme environments
- Robots take their pick in plastic moulding application
- Cutting edge cake slicing
- Robots make the cut
- Industry-first salient-pole motor
- Securing OT systems against cyber-attack
- Industry 4.0 ready
- Intelligent interlocks
- The digital future has begun
- The smart future of manufacturing
- Partnership integrates freight & warehouse management
- When & where will Industry 4.0 actually happen?
- Education key to unlocking I4.0
- How well is your smart farm running?
- Digitalisation, automation & electrification
- Industry 4.0 guidance platform