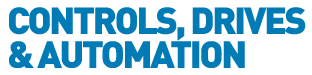
![]() |
Charlotte Stonestreet
Managing Editor |
Home> | IIot & Smart Technology | >Big Data | >Prioritising steps to Industry 4.0 reality |
Home> | IIot & Smart Technology | >Industry 4.0 | >Prioritising steps to Industry 4.0 reality |
Prioritising steps to Industry 4.0 reality
27 April 2022
With Industry 4.0 seeing systems and devices exchanging and interpreting shared data, advanced sensors are increasingly finding their way into modern manufacturing lines, facilitating informed decision-making – but this is just the beginning, says Paul Taylor

WHILE INDUSTRY 4.0 is a growing reality, much of it still remains a concept as the shift to this new method of working requires significant investment. While manufacturers’ understanding of Industry 4.0 and its potential value has grown steadily, many have not been able to translate that into workable transformation plans. This is because many brownfield factories do not have the necessary infrastructure to support Industry 4.0 in the UK and Europe. Hence some industries chose to follow the easier path of employing a low skilled and low paid workforce to carry out repetitive tasks. As companies become more aware about Industry 4.0, the realisation will become apparent that it is a route that must be taken for their business to thrive and survive.
As Industry 4.0 is gathering momentum globally, many companies are looking to adopt technologies such as data analytics and Industrial Internet-of-Things to improve their manufacturing competitiveness. This new era of manufacturing is characterised by seamless and effective data exchange across the value chain – from customer requirements, to supply chains, manufacturing, logistics and after-market services. Smart components and digital twins are also introducing a new level of flexibility to the production line. While the Industry 4.0 concept offers significant potential, the requirements for a successful transition go far beyond technology change.
The prevailing view appears to be that it is easier to build a new facility from scratch, rather than update current systems and processes – something that takes expertise, time and money. Consequently, while manufacturers recognise the potential value of i4.0, many have been unable to translate that into workable transformation plans. As companies become more aware about Industry 4.0, the realisation will become apparent that it is a route that must be taken for their business to thrive and survive. But, how should manufacturers, both large and small, effectively initiate this complex transformation to Industry 4.0?
Smart approach
In 2017, Singapore launched the Smart Industry Readiness Index, a diagnostic tool to help companies (large or small) evaluate the Industry 4.0 readiness of their facilities. It offers pragmatic analysis across the three fundamental building blocks of Industry 4.0 – Process, Technology and Organisation.
The Index was thoroughly validated by an advisory panel of academic and industry experts, and to ensure that it is an easy-to-use tool, the Index was piloted with companies within a diverse range of manufacturing sectors (e.g. chemicals, biomedical, electronics, aerospace) and across all business sizes, including small and medium-sized enterprises (SMEs). Its accompanying Assessment Matrix was the world’s first self- diagnostic i4.0 tool aimed at helping companies worldwide– regardless of size, industry, and digital maturity – determine how to start, scale and sustain their Industry 4.0 transformation.
The first step for a business with Industry 4.0 aspirations is to identify which aspects it must address to harness the full potential of a transition. The Index assessment process provides a valuable understanding of critical dimensions, as well as crucial insights into the individual facility’s status against those factors. This enables manufacturing companies to migrate by taking a targeted and stepwise approach, thereby creating tangible value for the business.
Realising that companies now need more help to better design and execute their transformation roadmaps, a new Prioritisation Matrix has been developed. This was developed by a partnership of the Singapore Economic Development Board, McKinsey & Company, SAP, Siemens and TÜV SÜD.
The Prioritisation Matrix partnership identified that the gap between awareness and implementation is often due to a company not having an effective Industry 4.0 roadmap, and that prioritisation was critical to achieving this. Identifying focus areas that generate the greatest value drives both informed decision making and effective resource allocation.
The aim of the Prioritisation Matrix is to therefore guide manufacturers to identify the areas of focus that will yield the greatest benefit to them. The ultimate aim is to alleviate uncertainties and help to accelerate the pace of Industry 4.0 transformation. The Prioritisation Matrix should be used after companies have used the Assessment Matrix to determine the Industry 4.0 maturity of their manufacturing facilities.
Let us first take a step back to the TIER framework, which provides a conceptual structure that underscores four key principles that companies must consider for a holistic prioritisation:
- Today’s state - an in-depth understanding of the company’s current Industry 4.0 maturity level
- Impact to the bottom line - identify the distinct Industry 4.0 areas that can generate the greatest financial return
- Essential business objectives – the most critical business objectives should guide the selection of Industry 4.0 areas
- Reference to the broader community - emulate successes and learn from the mistakes of the manufacturing community.
To translate the four TIER principles into practice, the Prioritisation Matrix helps to quantitatively identify high-priority Index Dimensions where improvements will bring the most benefit. The idea is to offer an approach to help companies move in the right direction as they forge ahead with their Industry 4.0 transformations roadmaps.
The Prioritisation Matrix formula brings together four inputs, each reflecting a key principle of prioritisation represented in the TIER framework:
1. Assessment Matrix Score – provides a baseline for companies to measure the impact of potential changes and track the progress of their transformation.
2. The Revenue-Cost Profile - breakdown of profit and loss categories as a percentage of overall revenue. This allows more emphasis to be placed on Index Dimensions that have greater influence over the key cost drivers and prioritise those that deliver the greatest financial benefit.
3. Key Performance Indicators – ranked to best reflect a company’s desired future positioning and business outcomes.
4. Identify proximity to the best-in-class – identify what the best-in-class have attained, to set pragmatic goals and aspirations. Identify the areas with the greatest scope for improvements. Companies that are already best in class in-class in certain aspects could use this information to further widen the gap against their competitors.
Industry 4.0 transformation
Some of the key Industry 4.0 concepts are the convergence of cyber-physical systems, with the advent of Information Technology (IT) and Operational Technology (OT) such as data analytics, robotics, and wireless communications. This results in the emergence of intelligent and autonomous networks that are capable of communicating and interacting with one another, and centralised factory control systems that increasingly give rise to decentralised decision-making.
By implementing Industry 4.0 solutions related to big data, machine learning, digital twin, artificial intelligence, predictive analytics etc., manufacturers aim to achieve the optimal level of responsiveness, adaptiveness and fully connected processes of a smart factory. However, planning and executing an Industry 4.0 transformation plan is a significant challenge as companies must make significant resource investments. However, it is hoped that the Prioritization Matrix will deliver industry greater confidence and encourage more companies to commit to an industry 4.0 transformation.
The expectations of Industry 4.0 are that it will increase efficiencies and enable product developers and manufacturers to tailor products to customers’ needs faster. However, the connected world of Industry 4.0 adds a new and significant dimension of complexity. There are many reasons why companies have been slow to adopt Industry 4.0 solutions despite high levels of awareness. One of the most commonly cited barriers is the lack of an effective strategy. In a world of scarce resources, information overload, and pressures to deliver short-term results, a clear Industry 4.0 vision is essential for companies to push beyond small-scale pilots and embrace real transformative projects.
Paul Taylor is business development director for industrial services at TÜV SÜD
Key Points
- Machinery safety risk assessment
- EMC Centre Of Excellence
- New CEO at TÜV SÜD UK & Ireland
- Getting the PUWER factor right
- New UK EMC test facility for TÜV SÜD
- Be on guard for cobot safety
- Wireless module warning
- New machinery guarding standard
- Electromagnetic machinery safety service
- UK’s first dedicated Industry 4.0 IoT cellular test service
- Industry 4.0 ready
- Intelligent interlocks
- The digital future has begun
- The smart future of manufacturing
- Partnership integrates freight & warehouse management
- Secure data handling
- When & where will Industry 4.0 actually happen?
- Education key to unlocking I4.0
- Trelleborg joins Smart Data Innovation Lab
- How well is your smart farm running?