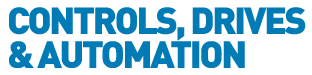
![]() |
Charlotte Stonestreet
Managing Editor |
Home> | POWER TRANSMISSION | >Bearings | >When the going gets tough |
When the going gets tough
20 March 2013
Phil Burge, country communication manager for SKF, explains why hybrid bearings have proved so effective in challenging applications.
Maintaining machinery and equipment reliability in harsh environments with aggressive operational conditions really tests rolling bearings to the limit. So, in addition to providing the best possible sealing solutions and lubrication tools, the designers and engineers behind modern bearings have focused their energies on improving bearing material and design, and yielded some excellent results. One such success has been the development of hybrid bearings.
High speed
Hybrid bearings combine rings made of bearing steel and rolling elements made of bearing grade silicon nitride (Si3N4). The combination of strength and lightness offered by hybrid bearings has proved to be a powerful formula that can serve a range of applications. For example, hybrid ball bearings offer a higher speed capability than standard steel bearings and typically provide a longer service life than all-steel bearings. Hybrid ball bearings also offer exceptional resistance in high temperature applications such as jet engines, where shaft speeds exceed 30,000 r/min and bearing temperatures are higher than 650°C. And, if further proof is required that hybrid ball bearings are a powerful solution, consider that where gas temperatures rise above 1100 °C, only high-performance ceramic materials are considered.
Robust service
One such example of critical equipment is the cryogenic pump used in the oil and gas and hydrocarbon processing industry. Cryogenic pumps must withstand a series of challenges, including high rotational speeds and prolonged vibration. They must also be able to function at extremely low temperatures (as low as -253°C) and resist corrosive gases and liquid corrosive contaminants, whilst providing robust service under continual start-stop cycles. Despite this tough list of demands, hybrid bearings have proved to be exceptionally reliable in this application. Steel roller bearing service life in cryogenic applications is typically less than six months, and demands high maintenance and repair costs, but an SKF hybrid bearing, combining ceramic rolling elements with super-tough, high-nitrogen stainless steel bearing rings, extends bearing service life by 300%.
The capabilities of hybrid bearings as excellent electrical insulators have also been significant in driving their proliferation in many applications, from F1 engines to machine tools. Stray electric currents are often caused by variable speed drives, an increasingly popular component used to optimise machines, but can also be the result of rotor asymmetries and unbalanced windings. Whatever the cause, it is important to minimise stray currents as they can cause significant damage to the bearing surface. Bearings can provide the path of least resistance for stray currents; the lubricant film in a rolling element bearing acts as a capacitor, and when the voltage difference that builds up between the bearing casing and the rolling elements overcomes the insulation provided by the lubricant a discharge occurs. As a result heat generated by the discharge causes local melting of the bearing metal surface. However, bearings with ceramic rolling elements can eliminate the electrical pathway through the motor bearings, preventing bearing damage and premature replacement.
Engineers are continuing to discover and exploit the properties of hybrid bearings in demanding applications. They are now offered in extra-large bore sizes to combat the dangers of stray electrical currents in wind turbines, where it is critically important to minimise costly maintenance visits to remote and hard to access locations. Hybrid ball bearings are now available in sizes specifically designed to fit these turbines – providing yet another example of how valuable these bearings can be.
- Hybrid bearings combine rings made of bearing steel and rolling elements made of bearing grade silicon nitride
- They offer higher speeds than standard steel bearings and typically provide a longer service life
- Electrical insulation properties alleviate damage caused by stray electric currents
- Bearing housings enhanced
- Affordable machine health monitoring
- White etching cracks: causes & mitigation
- Shaft alignment
- Thought leadership report
- Makes bearings selection easier
- SKF & Imperial College London extend relationship
- Bearing rating life model
- Super-precision series
- Linear motion technology showcases