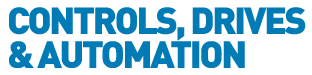
![]() |
Charlotte Stonestreet
Managing Editor |
Home> | DRIVES & MOTORS | >Variable Speed Drives | >Savings hidden in food production |
Savings hidden in food production
18 April 2019
As the demands on food & beverage production become higher, and margins become tighter, ABB’s Andrew Bould, explains why focusing only on the energy efficiency of variable speed drives (VSDs) and low voltage motors loses sight of the bigger picture of potential savings
The food and drink processing industry is the fourth highest industrial energy user in the UK, and electric motors account for the vast majority of consumption. However, many facilities still commonly operate motors without any form of variable speed control, or are running obsolete equipment that by today’s standards delivers poor efficiency performance.
The efficiency benefits of using VSDs in food production are well documented. For instance, high intensity processes like bakery ovens are a prime candidate for variable speed control. VSD fan control can efficiently circulate air flow to regulate temperature and moisture, leading to shorter baking times. This results in less oven use, and typically 20 to 60 percent energy savings. Food production involves a wide range of motor-driven processes, from mixers and shredders to pumps and fans. Using variable speed control on these applications when demand is low can dramatically reduce energy usage.
Belt conveyors, although constant speed rather than variable, can also achieve efficiency savings. Motor and drive packages can be used to ensure that goods are moved smoothly and uniformly to eliminate high peak starting loads, and avoid drivetrain damage.
However, efficiency is only part of the full picture of potential savings. New features increasingly built into modern VSDs now provide hitherto untapped opportunities for improving safety, productivity and reliability in food production.
Safety
Plant and machinery incidents are one of the main causes of major injury in food processing, often during cleaning or routine maintenance. Almost everywhere you look in a typical facility, from mixers and conveyors to moulders and slicers, there is a risk to personnel. VSDs incorporate a multitude of safety features to reduce risk. Safe torque off (STO) is a function that when activated immediately switches off the drive output to the motor, and ensures that it cannot be unexpectedly restarted.
Dust is an occupational hazard of working in food production, and in high concentrations it can be flammable and sometimes explosive. Dust ignition certified motors, constructed from aluminium or cast-iron, are available in both low and high voltages that fulfil EN standards and ATEX directives, to limit the possibility of dust explosions.
Productivity
Production must be agile to adapt quickly to meet evolving customer tastes. However, changing fixed-speed equipment and resetting lines to provide varying production volumes takes time and money. VSDs allow greater flexibility in ramping production lines up and down, as any change in speed requirements can be implemented quickly without the need for lengthy configuration and calibration.
Precision control of motors using VSDs leads to higher consistency. For instance, using features like PID to manage variables such as air temperature, humidity and flow more accurately can improve the texture, quality and uniformity of products passing through provers and ovens, while avoiding temperature spikes. Accurate dosing and precise speed and torque control can also reduce wastage and increase product quality during the mixing and forming stages.
Reliability
In 2016, ABB introduced the ABB Ability Smart Sensor for low voltage motors. The sensor converts traditional motors, into smart, wirelessly connected devices. The smart sensor technology has evolved and is now applied to pumps and mounted bearings. With each component part of the powertrain being tracked and monitored, the important task is to turn the data collected into usable information.
For instance, the measurements collected by the ABB Ability Smart Sensor for pumps, calculates health indicators for detecting common problems including cavitation, bearing failure, vibration, flow turbulence, blade problems, looseness, unbalance or overheating. Because the solution gathers real data on the real condition in the pump, it can be used to efficiently deploy maintenance teams.
The data collected can help identify any inefficiencies in the overall powertrain system, allowing maintenance teams to target individual components for further investigation. Benefits include early warning of problems, helping prevent unexpected downtime and extend equipment lifetime.
Key Points
- New features built into modern VSDs now provide opportunities for improving safety, productivity and reliability in food production
- VSDs allow greater flexibility in ramping production lines up and down, as any change in speed requirements can be implemented quickly
- ABB's Ability Smart Sensor for low voltage motors converts traditional motors, into smart, wirelessly connected devices
- VSD shakes up milking parlour energy costs
- ABB launches virtual technical assistance support service
- The true cost of owning an electric motor
- Landfill site cuts pump power
- In-Built Intelligent Pump Function
- Reliability on a roll
- ABB and B&R to demonstrate integrated automation capabilities at Automation UK
- ABB scoops EFF Future Manufacturing Award
- Automation technologies
- Enabling real-time collaboration
- PUMPED UP PERFORMANCE
- SOFT STARTER OR VARIABLE SPEED DRIVE?
- Jeans With Less Energy
- Enhanced to Withstand Tough Environments
- Savings From Improved Torque Ratio & Efficiency
- Modular VSD
- ENERGY SAVING: AN OLD MESSAGE WITH NEW PROMISE
- Updated installation guide for power drive systems
- UK drives manufacturer seals global automation deal
- WEG motors & drives power high-efficiency air blowers