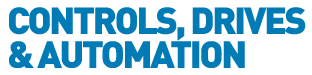
![]() |
Charlotte Stonestreet
Managing Editor |
Home> | DRIVES & MOTORS | >Variable Speed Drives | >The importance of being serviced |
The importance of being serviced
07 September 2020
Many companies service variable speed drives (VSDs), but not all of them carry an official manufacturer’s accreditation to do so. Alan Jones puts forward why he thinks working with a trusted, local partner is crucial to ensure optimal performance and longevity from your motor-driven equipment
Now, more than ever, reducing maintenance costs and improving uptime is crucial in navigating these challenging economic conditions. In the midst of the COVID-19 pandemic, some companies are having to operate with reduced maintenance resources, which can make it all the more difficult to ensure that equipment is kept in peak condition at all times. Others are limiting the number of people and suppliers allowed on-site. This presents new challenges for all in terms of keeping production lines running while having limited resources with which to do so.
Electric motors and variable speed drives (VSDs) form the backbone of almost all industrial processes, powering the fans, pumps, compressors and conveyors that operate throughout the value chain to turn raw materials into finished product. Keeping these critical applications running is essential for maintaining profitability. However, with maintenance budgets being cut, and the logistical problems of getting personnel onto a site, motor and VSD service providers can step in to provide comprehensive maintenance services and ensure that production doesn’t skip a beat.
Flexible servicing
Service contracts for VSDs are nothing new, but in the prevailing circumstances they have come into their own as a key component of an effective maintenance strategy. VSDs have very few parts that need frequent maintenance, but inevitably components will eventually wear out and therefore need to be regularly checked, maintained and/or replaced. A service contract helps companies to stay on top of all their VSD’s needs, whether they are running a single asset or a fleet of them.
Service contracts are not monolithic, and typically offer a tiered approach, allowing flexibility to suit the particular needs of a customer. For instance, a preventive care contract provides a maintenance program for an installed VSD, which is carried out by an engineer either directly from the manufacturer, or from an accredited third party, freeing up in-house personnel for other tasks. Accredited companies are up to speed on the latest product developments and best practices, while also having access to tools and techniques that other service companies do not.
Having a detailed maintenance schedule, which can be managed by a technical partner that you trust, can ensure that your VSD’s performance is always optimised for maximum energy saving and productivity. Rather than sticking to arbitrary schedules, preventive maintenance ensures that parts are replaced when needed, rather than when the schedule dictates, saving you money on components. Against the backdrop of COVID-19, getting personnel, particularly from third parties, on to a site can be a challenge. This can be mitigated by conducting virtual site visits via phone or tablet, and through remote monitoring via the cloud.
Genuine spare parts
Using an accredited partner means that replacement components are of a guaranteed quality, and that engineers are fully trained, experienced, and accountable for the quality of their work. Counterfeit or substitute components are a growing issue in the VSD market. These can put entire production lines or even lives at risk, with potential downtime costing thousands of pounds per hour. Furthermore, many VSD manufacturers specify that the use of non-approved components will immediately invalidate the drive’s warranty. Reputable manufacturers will routinely invest extensively in testing to ensure that safety and performance standards are met both at a component and device level, which cannot necessarily be said for cheaper, non-approved spare parts.
Modern VSDs are incredibly robust, but frequent tripping, and/or hazardous environments, combined with countless hours of usage, can eventually lead to failures. A complete care contract provides an additional layer of protection on top of any preventive maintenance arrangements. In the unlikely event of a complete VSD failure, a complete care contract means that the stricken VSD will be repaired or replaced in good time, and often free of charge.
Hiring VSDs
In the event that the VSD cannot be repaired or replaced in a timely manner, end-users can hire a drive on a temporary basis until a longer-term solution can be found, allowing production to continue. In ABB’s case, once the decision has been taken to either repair or replace, the daily rental cost for the hire drive is lifted once the purchase order has been placed, while the customer can keep the hire drive running until the “new” VSD arrives on-site.
Real-life examples
One example of how a quick response from a local provider can make all the difference occurred recently when my company, APDS, received a call from an aggregates facility in South Wales. A drive thyristor fault meant that production was backing up, and the customer only had 50 hours of capacity available before production would have to cease, costing huge amounts of money in lost production and contractual penalties.
The customer’s service contract with us meant that we could get an engineer on-site almost immediately. We equip our service engineers with ABB service suitcases containing almost everything they could need to diagnose and repair on-site. Ultimately it was thanks to this speedy intervention, as well as our engineer‘s experience in being able to quickly identify and fix the problem under considerable pressure, that the customer was able to get production back online while averting any losses or penalties.
No two call-outs are ever the same, and often my team, as well as my counterparts at other ABB Value Providers across the country, have to use all of their experience and ingenuity to solve complex technical problems. Fellow ABB Value Provider, Gibbons Engineering Group, recently helped a Suffolk pumping station to avoid serious disruption to the water supply for some 2,000 local households after a double drive failure. Within hours of the call-out, the Gibbons team had installed two ABB 90 kW hire drives, buying the water company precious time to arrange a more permanent solution.
Adjusting to the new normal while maintaining or even increasing production levels is a difficult challenge for all. A service contract with a partner you trust can provide you with the peace of mind of knowing that your VSDs are in safe hands, that they are fully maintained and optimised, and that even in the event of a failure, production will not suffer.
A service contract offers much more value than the VSD’s warranty alone. A warranty will not cover wear and tear, nor will it provide maintenance, or cover the cost of repair or replacement. What it certainly does not cover is the cost of sourcing and installing a temporary or permanent replacement in the event of unplanned downtime. A service contract with an accredited partner can ensure that your VSD is kept in optimal condition throughout its entire lifecycle, with round-the-clock support in the event of an emergency.
Key Points
- In current circumstances VSD service contracts have come into their own as a key component of an effective maintenance strategy
- Modern VSDs are robust, but frequent tripping, and/or hazardous environments, plus countless hours of usage, can lead to failures
- A detailed maintenance schedule can ensure the VSD’s performance is optimised for maximum energy saving and productivity
Alan Jones is sales director of APDS, an ABB Value Provider
- Vitens selects ABB to develop new process automation system
- ABB automates warehouse operation
- ABB celebrates 20-year milestone in DCS leadership
- Aquaculture agreement catches real-time data
- Driving smart manufacturing in China's automotive industry
- ABB urges greater adoption of high-efficiency motors & drives
- ABB acquires Sevensense
- Win two tickets to the Formula E London E-Prix
- ABB achieves IE6 hyper-efficiency with magnet-free motors
- ABB acquires innovative optical sensor company
- PUMPED UP PERFORMANCE
- SOFT STARTER OR VARIABLE SPEED DRIVE?
- Jeans With Less Energy
- Enhanced to Withstand Tough Environments
- Savings From Improved Torque Ratio & Efficiency
- Modular VSD
- ENERGY SAVING: AN OLD MESSAGE WITH NEW PROMISE
- Updated installation guide for power drive systems
- UK drives manufacturer seals global automation deal
- WEG motors & drives power high-efficiency air blowers