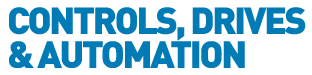
![]() |
Charlotte Stonestreet
Managing Editor |
Home> | AUTOMATION | >Handling & Logistics | >RFID solution as a service |
RFID solution as a service
02 March 2022
While most of us are more than familiar with basic concept of RFID, the technology goes far beyond the idea of a 'smart barcode'. Ian Manning takes a look at the concept of RFID as both a product and a service

WHILE THERE are some similarities between an RFID (radio frequency identification) tag and a barcode, there are also significant differences. It is these differences that compelled Turck Banner to consider RFID not as an isolated product but as a solution technology. This not only spans the whole organisation from input to output but often extends well beyond the company premises.
If we compare a barcode and an RFID tag: A barcode is a fixed reference number that is read using a laser or camera. A direct line of sight is required between the reader and the barcode. The code must be presented to the reader within an angle of about 70 degrees and typically only one code can be read at a time.
An RFID tag is powered, identified, read and written using radio waves. Each tag has a globally unique identification number and can also hold up to a few Kilobytes of re-writeable data. Tags can be read from a distance of more than 3m can be in any orientation, and hundreds of tags can be read at the same time.
Short range read/write heads can be used where precise positioning of a product is required i.e. tracking a vehicle through a production line.
Long range ability
The ability of long range read/write heads to see multiple tags broadens their use enormously, for example a whole pallet of components, each with an RFID tag, can be read in one pass without unpacking the pallet.
As a product or technology, RFID is well proven, but the real challenge and advantages come in its implementation. Not only does a good implementation have to achieve its primary goals, it also has to cope with errors to maintain reliability and accuracy. To give a few examples: It can identify stray tags which may have become detached from their component and become stuck under the racking. It can determine which tags are on a specific pallet, not adjacent pallets.
Although an RFID installation often stops at its initial requirement, the infrastructure needed for this can be utilised for a greater advantage and return on investment.
In a recent installation the multi read capability was used to inventory complete shipments of sub-assemblies as they arrived at a factory. The individual sub-assemblies were then tracked through the production process until they left the factory as a complete assembly. An individual footprint trace through production allows any faults in the final product to be tracked all the way back to the original suppliers. Analysing data gathered from all the traces through production highlights where improvements can be made. Tags were added to the bulk containers of sub components and this data was added to each assembly as it passed through production, further enhancing traceability. Real time production statistics were now available.
Improvement data
The initial investment was based upon the time saved, not having to count and process the sub-assemblies as they arrived at the factory. The traceability and production improvement data gathering were added for very little extra cost. In order to provide these sorts of added benefits Turck have an specialist RFID division (Turck Vilant) who employ in excess of 20 full time programmers with the expertise required to maintain the accuracy and reliability of the data and to also integrate our system into existing infrastructure, MES, ERP, WMS Cloud etc. Turck Vilant will manage a project from design concept to implementation and beyond, with the confidence to offer 24/7 service level agreements.
RFID is both a product and a solution. The product is good but the solution is great.
Ian Manning is marketing manager at Turck Banner
Key Points
- Sustainability germinates at Turck Banner
- Industrial connectivity - the past, present & future
- Pick-to-light technology
- Control on a roll!
- Sustainability through supply chain management
- Seeing the light
- Choosing a precision measurement sensor
- Process monitoring at every level
- Centralised or decentralised Automation?
- Distributor turns manufacturer