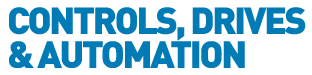
![]() |
Charlotte Stonestreet
Managing Editor |
Editor's Pick
Breaking down interoperability barriers
16 December 2021
As an open communication protocol, OPC UA enables continuous and transparent communication from the sensor to the cloud. By adding the real-time capability of TSN, the protocol enables IT and OT to merge into a common network, asserts Christoph Neumann

WHETHER IN classic mechanical and plant engineering, medical technology, process automation or in the construction and operation of critical infrastructures: the future belongs to systems that work according to the principles of Industry 4.0. Machines in smart factories organise themselves to a large extent, supply chains coordinate themselves automatically and preliminary products supply their complete production information themselves to the machines that manufacture products from them.
To achieve this, production must adapt agilely and dynamically to changing requirements. This makes it necessary for all parts of the plant automation to communicate with other systems in the company on many levels. In the course of implementing the Industrial Internet of Things (IIoT), the number of self-intelligent nodes at the field level in the networks is increasing rapidly.
In addition, real-time capability is required in many places in industrial applications for the synchronisation of movement processes. Time-critical applications, such as synchronising a robot with an intelligent track system, can require cycle times down to the microsecond range.
Although Ethernet enables the fast transmission of large amounts of data, it does not have a truly predictable time behaviour and thus does not fulfil these criteria. Therefore, under the common term Industrial Ethernet, a plethora of different - basically proprietary - systems emerged that deviate from the Ethernet standard to a greater or lesser extent and are not compatible with each other.
"Connecting different incompatible protocols via interfaces to form an overall network is very time-consuming," says Christoph Neumann, VP technology at embedded computer manufacturer Kontron. "Only with a uniform, real-time network that is interoperable and unifies the standards of IT with the standards of industry will the implementation of Industry 4.0 methods become realistic."
Cross-manufacturer communication
The prerequisite for this is an open and at the same time real-time-capable communication protocol. Many leading manufacturers of automation and information technology rely on the manufacturer-independent communication solution OPC UA over TSN. This universal communication platform is reported to be about to establish itself as the only globally uniform real-time communication standard.
An industrial communication protocol has already existed since 2006 with which machine data can be described semantically in a machine-readable manner: Open Platform Communication Unified Architecture (OPC UA) according to IEC 62541. In addition to its independence from manufacturers and inherent security, OPC UA owes its high popularity to an integrated introduction mechanism. "This allows new and previously unknown devices to be brought into the network later without having to take this into account from the outset in the programme or configuration," says Christoph, describing its benefits. "This makes production plants future-proof, because it significantly reduces the effort for conversions and modernisations."
However, OPC UA does not have deterministic time behaviour, so it is not suitable for the transmission of real-time data within synchronised plant sections. For data exchange between controllers, the OPC Foundation therefore introduced the fast Publisher-Subscriber (Pub/Sub) communication model. Continuous transmission, without waiting for responses from the recipients between individual messages, already enables a considerable acceleration of communication and a reduction in the load on the network. The ability for deterministic, hard real-time behaviour, however, comes from using the real-time Ethernet standard TSN (Time Sensitive Networking).
The new Ethernet
Time-Sensitive Networking (TSN) is an extension of the Ethernet standard of the IEEE (Institute of Electrical and Electronics Engineers) by a whole bundle of standards that regulate the transmission behaviour of data packets in various ways and thus give it real-time capability. For this purpose, TSN has three core capabilities: time synchronisation via a uniform time base, traffic scheduling and automated system configuration.
Ultimately, only the combination of OPC UA PubSub with the communication technology TSN enables the realisation of real-time capable applications in the industrial environment based on generally available standards.
"The extension of OPC UA with TSN guarantees the deterministic transmission of data in large convergent networks and can resolve the previous separation of machine and IT networks," says Newman. "It can enable intelligent decentralised architectures as well as fast centralised drive concepts."
Performance increases in the course of the redefinition of Ethernet also contribute to this. This technology enables plug-and-produce-capable networks with several 10,000 nodes that can be easily administered and configured. At the same time, the network participants can communicate up to 18 times faster than with all previous protocols. Among other things, this opens up new possibilities in the field of highly synchronous drive applications and control tasks.
A reality today
As one of the pioneers of this technology, Kontron presented a starter kit for TSN at the SPS IPC Drives 2018 trade fair in Nuremberg. Following an FPGA software upgrade, this now also supports new standards such as IEEE 802.1Qbu and 802.1CB for reduced latency and jitter as well as redundant, fault-tolerant networks. The open source stack according to open 62541 for OPC UA over TSN with PubSub and the netconf protocol required for central management via CUC and CNC are now also integrated in the starter kit.
In addition, Kontron is equipping more and more products with TSN capability as standard, for example COM Express® modules, 3U VPX blades and 3.5" SBCs. This is facilitated by the integration of TSN functionality in semiconductors from numerous manufacturers, such as the 11th generation Intel Core processors.
"By fully integrating OPC UA over TSN into our hardware and software, we make it easier for users to realise convergent Ethernet-based networks, being able to run time-synchronised, deterministic communication parallel to regular IT data traffic," Christoph is convinced. "This way, real IIoT or Industry 4.0 based on universally valid Ethernet protocol standards become possible."
Christoph Neumann is VP Technology at Kontron
Key Points
- Industry 4.0 ready
- Intelligent interlocks
- Phoenix Contact takes over Etherwan Systems Inc.
- EtherCAT control solution
- Protecting rack mount Ethernet switches
- Increased Ethernet network visibility
- Stainless Steel Solutions
- Slewing Solutions
- Double-Enveloping Worm Gear Sets
- Precision Motion Control Solutions