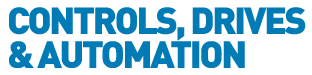
![]() |
Charlotte Stonestreet
Managing Editor |
Home> | DRIVES & MOTORS | >Synchronous Motors | >Growth or sustainability? |
Growth or sustainability?
03 October 2024
Marek Lukaszczyk explains how WEG’s new W23 Sync+ ULTRA motor utilises two technologies to reduce electrical losses for more sustainable operations and reduced total cost of ownership (TCO)

ECONOMIC GROWTH means increasing production and consuming scarce resources, which invites negative effects on the climate, nature, and human well-being. Nevertheless, in the 1970s, American economist William Nordhaus argued that long-term economic growth is not constrained by resource scarcity — such as the depletion of fossil fuels or minerals — because these issues can be overcome with more efficient production and the use of renewable resources.
Today, half a century later, renewable energy use is on the rise across the European Union as industry seeks to adhere to the 2015 Paris Agreement, targeting a 45% emissions reduction by 2030 and net zero by 2050. The European Commission (EC) reports that renewable energy sources accounted for 24.8% of the region’s total energy use for heating and cooling in 2022, up from 11.7% in 2004, with the industrial sector being a major driver of this growth.
Meanwhile, the European Environment Agency (EEA)’s Growth Without Economic Growth report echoes Nordhaus’s sentiments. It cites the idea of “ecomodernist thought that invests its hopes in scientific and technological progress (e.g., ecodesign, green innovation) directed towards sustainability". A critical step towards achieving the Paris Agreement’s goals is the rapid implementation of energy-efficient technologies – including electric motors.
Ecodesign and motors
Electric motor systems, which account for 53% of global electricity use according to the International Energy Agency (IEA), play a vital role in reducing CO2 emissions. The IEA’s World Energy Outlook 2021 underscores the importance of these systems, outlining 40 key milestones necessary to prevent a 30%increase in final energy consumption by 2030.
One such milestone is ensuring that all motor sales adhere to best-in-class standards by 2035. While many countries have established Minimum Energy Performance Standards (MEPS) to support their climate agendas, the current technologies available in the electric motor market make it possible to advance rapidly.
Induction motors have long been the go-to choice for industrial applications, prized for their affordability and reliability. However, their dominance faces challenges from emerging technologies driven by stricter efficiency regulations and heightened awareness of energy efficiency’s importance.
While induction motors can achieve efficiencies surpassing IE4 standards, permanent magnet (PM) and synchronous reluctance (SynRM) motors have pushed boundaries, achieving efficiencies surpassing IE5 levels — an International Efficiency (IE) class, established by the International Electrotechnical Commission (IEC) that categorises motors based on their energy efficiency levels.
To illustrate the importance of IE ratings and ecodesign in motors more generally, research by WEG found that upgrading from standard IE2 high-efficiency motors to IE3 premium-efficiency motors can result in energy savings between 2.1 and 12.4%. The highest established efficiency level, IE5, is an evolution with 20% lower losses than its predecessor, IE4.
Utilising magnets
Now, in a climate increasingly focused on energy efficiency and environmental stewardship, WEG has introduced a hybrid innovation that merges PM technology, including ferrite or neodymium magnets and SynRM motor technologies.
The W23 Sync+ achieves the IE5 efficiency level, while the W23 Sync+ ULTRA, WEG's premier model, reaches the IE6 efficiency level. If a motor is rated to IE6, it means simply that the machine has 20% less losses than IE5.
WEG’s PMSynRM technology ensures a consistent efficiency curve, delivering superior efficiency across the entire speed range compared to traditional induction motors and a higher power factor than standard synchronous reluctance motors.
This efficiency translates to lower energy consumption and reduced TCO for plant managers. PMSynRM technology reduces electrical losses in the motor by utilising magnets that generate their own magnetic field without needing to induce currents, thereby minimising the motor's total losses.
Compared with competing SynRM motors, the W23 Sync+ ULTRA has a superior Power Factor (PF) — the efficiency of converting electrical power into useful mechanical power, influencing energy efficiency and operational costs. Because of this, a smaller sized variable speed controller can be used, leading to large energy savings. Let’s consider some applications where the W23 Sync+ ULTRA can prove beneficial.
Reducing CO2
Industrial processes often operate at fluctuating load requirements depending on required flow and throughput.
Examples include variable air volume (VAV) systems in large office buildings, conveyor systems in manufacturing plants, or water treatment processes involving pumps and blowers that must adjust their speed to match changing water flow rates. These applications do not require the motor to run at rated speed for their entire operation time, which can be problematic for some types of motors.
For instance, induction squirrel cage motors are most efficient at between 80 to 100% of the rated output, but this efficiency drops sharply below 50% of rated output. What’s more, efficiency isn’t solely about energy consumption, and also impacts the motor’s operational lifespan.
Higher losses also mean higher heat, which impedes the operational lifespan of the motor and increases maintenance needs. Considering that energy costs account for about 97% of the TCO during a motor’s lifetime, it’s clear that a more energy-efficient technology is needed.
To this end, the W23 Sync+ ULTRA operates at synchronous speed, eliminating almost all the electrical and magnetic losses in the rotor, being more efficient and offering a significant reduction in energy consumption. In addition, the W23 Sync+ ULTRA presents improved operating characteristics in partial load conditions. The partial load efficiency of the W23 Sync+ ULTRA is much higher when compared to induction squirrel cage motors.
How does this contribute to reducing CO2 emissions? The W23 Sync+ motor line enables significant energy savings that directly affect a facility's carbon footprint. For example, WEG has calculated that replacing a 75kW 4-pole IE3 induction motor with an IE6 W23 Sync+ ULTRA can result in a reduction of 126 tons of CO2 over the motor's expected 25-year lifespan.
By setting higher efficiency standards and reducing energy waste, the W23 Sync+ ULTRA plays a crucial role in reducing carbon emissions and advancing the energy transition. Going forward, PMSynRM motors will play a key role in helping industry achieve more sustainable and eco-friendly operations and answer the age-old question: yes, economic growth and sustainability can complement each other.
- Sustainability on the open seas
- WEG and AMT form collaborative partnership
- Energy reduction initiative
- Frame size H VSD
- VSD for HVAC
- Baking rolls on a large scale
- VSDs for safer operations
- Flexible & efficient geared motors
- Transport infrastructure project benefits from over 350 WEG motors
- Energy efficient standard motor range with 40% less losses
- High Speed, Low Vibration
- HIGHER TORQUE
- Fast Payback In High Power Applications
- Synchronous PM Motors - IE4
- Production line upgrade
- Natural ventilation permits wider use of torque motors
- Permanent-magnet motor surpasses IE4 standard
- IE5 efficiency without rare earth magnets
- Interroll raises profile
- Reliability issues solved