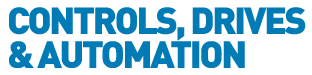
![]() |
Charlotte Stonestreet
Managing Editor |
Home> | DRIVES & MOTORS | >Variable Speed Drives | >What does the future hold for drives and motors? |
What does the future hold for drives and motors?
18 May 2021
Motor and variable speed drive technologies are continuing to evolve rapidly, opening new possibilities for improving the efficiency, productivity, reliability and safety of industrial processes. David Hughes explores some of the major new innovations that are set to influence the market in the coming years
ELECTRIC MOTORS and variable speed drives (VSDs) are by no means new technologies, but if you think that we’ve reached a plateau in terms of what they can do, and how they can add value to industrial processes, then think again. New innovations are continually emerging and helping to improve performance, make maintenance easier and streamline the integration of drives, motors and other powertrain components into the heart of the modern factory.
Looking ahead to the next few years, here are just some of the ways in which motors and drives are set to open new opportunities, in particular for end-users and OEMs.
Smart sensors
Wireless smart sensors have been around for several years, but the latest generation is pushing the boundaries of where and how they can be used. In addition, manufacturers are increasingly starting to ship them as standard with powertrain components, helping to bring affordable remote condition monitoring capabilities to a wider cohort of end-users.
Improvements in robustness and reliability are introducing new applications to the benefits of smart sensors. For instance, ABB’s High Performance Smart Sensor for hazardous areas permits monitoring of equipment in explosive atmospheres. ATEX, IECEx and NEC 500 certified, the sensors are ruggedised to perform in harsh environments, and have a battery life three times longer than previous generations. Smart sensors now have greater accuracy, with newer generations boasting a wider data range and greater sensitivity to small changes in the condition of equipment, allowing better monitoring and earlier warning of potential faults. As a result of smart sensor technologies, remote condition monitoring will soon be available to all.
Value added services
When choosing between various VSD and electric motor suppliers there are many factors to consider. Reliability, efficiency and ease of use of both the product and the supplier are clearly important. But many people still consider the most important differentiator to be cost, both in capital (capex) and operating (opex) expenditures. However, manufacturers are increasingly including more value-added services in the cost of the VSD and motor. The true value of these services is not always immediately obvious at the point of purchase but can end up making all the difference further down the line.
Service contracts, for instance, are becoming smarter. For companies or sites with a large installed base, it can be difficult to keep track of maintenance requirements and upgrade strategies for each device. A Life Cycle Assessment (LCA) is a service that allows you to essentially automate this process. After registering the device, the service can keep track of condition, maintenance intervals and life cycle for you. This helps to provide an easily accessible pathway for upgrades and replacement of motors and drives, while ensuring that obsolete or failed equipment can be replaced quickly and with a suitable device for the application. This can save a huge amount of time spent manually logging equipment and updating spreadsheets.
Remote condition monitoring is also an area where significant value can be added. VSDs, by their nature, are digital devices, loaded with performance data. Collecting information from VSDs and analysing it with digital algorithms, gives a valuable insight into a plant's motor-driven applications, raising its operational efficiency.
For instance, ABB Ability Condition Monitoring for drives consists of a suite of services designed to provide key information about drive events and changes in behaviour – ensuring an application is always available, reliable and well maintained. A drive's status can be viewed through ABB’s internet portal or the data can be integrated with a company's own existing monitoring systems. Optional services include digitally enabled remote assistance by ABB technical support, advanced analytics and reporting and a range of other features that make maintenance operations more effective.
The true cost of a breakdown is usually a lot more than merely replacing a failed product. That is why it is essential to consider the total cost of ownership (TCO). The TCO not only considers the purchase price and the running costs, but critically, the cost of not running. The cost of not running is a direct cost to a process such as the impact that a forced outage can have on a company’s brand and image. It can also mean tens, or even hundreds of thousands of pounds for every hour in lost production as well as manufacturing staff not being fully utilised. The cost of running and cost of not running are two costs that can be so huge that they dwarf the initial purchase cost.
E-mobility
It is no secret that electric vehicles are the future of transport, but what you may not know is that many of the technologies developed for industrial electric motors are transferable to e-mobility motors.
Motors have long been a cornerstone in industry, keeping fans, pumps and compressors running 24/7, while also adapting to the variable external dynamics experienced when used with heavy-duty machinery. In the latter, more arduous applications, motors must be extremely robust, be safe to operate, optimised to the specific machine application and possible to manufacture in high volumes.
Meanwhile, ABB has extensive experience with traction motors. For a century, it has provided the railway industry with optimised traction motors for applications ranging from small trams to large diesel-electric locomotives.
Now, these skills in traction motors are being combined with the experience from the portfolio of industrial motors to produce e-mobility motors for heavy working machinery, such as that used in mining, construction and material handling.
A further development sees the arrival of complete electric drivelines which integrate the motor, drive and digital monitoring system and then optimises the combination for individual machines and working cycles. The e-mobility drivelines are easy to install in new electrified machines and can readily convert existing engine platforms to an electric drive – thus minimising development cost and effort for OEMs. ABB’s driveline solutions are already in commercial operation, for example, in the mining industry, where it has developed optimised driveline solutions in close cooperation with heavy machine OEMs.
Synchronous reluctance motorThe synchronous reluctance motor (SynRM) is another technology that has been around for some years, but thanks to new developments, it is fast becoming the most efficient motor type on the market. Synchronous reluctance technology combines the performance of permanent magnet motors with the simplicity of induction motors. The rotor in a SynRM has no magnets or windings and suffers virtually no power losses.
In 2020, ABB introduced a new generation of SynRM that achieves IE5 efficiency levels. These offer up to 40 percent lower energy losses as well as significantly lower energy consumption and CO2 emissions compared to an equivalent IE3 induction motor. Lower bearing and winding temperatures mean a longer lifetime compared to induction motors, while their versatility makes them a good fit for a wide range of industrial applications where they can offer accurate control and high efficiency across the whole speed range, even at partial loads.
Quite simply, the SynRM is now the most efficient motor on the market, and its price is comparable to standard induction motors, making it likely that we’ll see them adopted far more widely.
In conclusion
Often it is only when you look back over previous years that it becomes apparent just how quickly motor and VSD technology has moved on. A decade ago IE3 was considered the gold standard for efficiency – now we have IE5 motor-drive packages, as typified by ABB's synchronous reluctance motor (SynRM) and drive package. Smart sensors were not widely available – now some manufacturers are shipping them as standard. The evolution of motor and VSD technology is often manifested in incremental gains, but when you add these incremental gains up, and compare technology from even recent times with what is available today, it’s clear that the evolution of motors and VSDs shows no sign of letting up.
David Hughes is UK managing director, ABB
Key Points
- ABB acquisition complements smart buildings portfolio
- ABB acquires innovative optical sensor company
- Big savings at Mini plant
- ABB publishes EPD for distributed control system controllers
- Power of data reveals energy saving opportunities
- How we arrived at ready-to-ship high voltage motors
- Reduce your motor-drive energy losses by up to 50%
- ABB urges greater adoption of high-efficiency motors & drives
- ABB enhances Connected Worker Suite
- ABB acquires Sevensense
- PUMPED UP PERFORMANCE
- SOFT STARTER OR VARIABLE SPEED DRIVE?
- Jeans With Less Energy
- Enhanced to Withstand Tough Environments
- Savings From Improved Torque Ratio & Efficiency
- Modular VSD
- ENERGY SAVING: AN OLD MESSAGE WITH NEW PROMISE
- Updated installation guide for power drive systems
- UK drives manufacturer seals global automation deal
- WEG motors & drives power high-efficiency air blowers