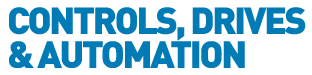
![]() |
Charlotte Stonestreet
Managing Editor |
Home> | DRIVES & MOTORS | >Servo Motors & Drives | >Masters of harsh environment motion control |
Editor's Pick
Masters of harsh environment motion control
30 June 2020
With its longstanding and well proven expertise for stepper motor based applications in deep space, ultra-high vacuum and cryogenic conditions as well as submersible motors and motors deployed under extreme levels of radiation, specialist German manufacturer Phytron, knows a thing or two about harsh and extreme environment motion control
Image: Motorised multi-axis mechanism inside an ultra-high vacuum chamber
Exclusively represented in the UK and Ireland by Mclennan, Phytron’s business areas are divided between industrial, harsh, extreme, and space environments. For each area, the principal characteristic technology is the stepper motor. With no contact and thus wear between rotor and stator components and perfect operation from digital open-loop controls (with the option of position verification using highly ruggedised resolvers or encoders), their simple construction, straightforward control and very high inherent reliability make stepper motors the preferred drives for these challenging environments. For Phytron, motion control tasks are equally fulfilled with stepper motors as separate components with complementary indexing drives or motion controllers. They can be integrated with precision gearboxes as rotary or linear actuators, or as complete linear or rotary positioning stages for multi-axis applications.
Image: Phytron’s LA25 - stepper driven linear actuator for use in ultra-high vacuum and temperature as low as -269°C
The extreme environments covered can be categorised by one or any of combination of the following conditions: very low or very high temperatures from -270˚C to + 300˚C in the vicinity of the motor; vacuum levels up to 10-11 Torr with provision for undesired gas emissions; ionising radiation which attacks and deteriorates drive systems (up to 108 Rad); and also aggressive environmental conditions requiring a motors or actuators that are hermetically sealed.
Whilst Phytron has a comprehensive standard range, for many harsh and extreme environment applications it is often necessary to custom modify standard product, whilst for space projects it is almost always essential to design and build from scratch. Phytron’s stepper motors are based upon NEMA frame sizes and typically cover holding torque ratings from 3 mNm to 13 Nm – size for size, a measure of performance derating often accompanies environmental conditions for each given application.
Industrial grade IP68 sealed stepper motors and actuators find applications in food and paper processing industries as well as outdoor use for aerospace and oil-industry positioning tasks. Often accompanied with the need to withstand high temperature extremes, high ambient pressures and endure high levels of shock and vibration, such motors require a much more robust design than standard off-the-shelf stepper motors from other manufacturers. Specialised harsh environment capable products also include complete IP67 rated linear actuators and IP protected stainless steel housed motors.
Application expertise
Examples of Phytron’s application expertise for extreme environments include manipulation and precision positioning of beam-line components in particle accelerators or transporting frozen samples in liquid nitrogen at temperatures below -200˚C. Typically motors and geared actuators for high-energy physics include stainless steel or titanium materials for housing, flanges and internal parts with bearings dry-lubricated and vacuum prepared. Other applications include high vacuum rated motors and actuators for mass spectrometers, electron microscopes and coating/spluttering equipment where radiation hardened materials are an absolute necessity.
Optional features for actuators can include encoders with a switching cam system for verification of positional movement and integrated thermocouples for accurate motor temperature measurement.
Phytron’s expertise in deep space motion control spans more than 30 years with over 1000 motors successfully deployed on exploration craft and satellite systems. Phytron's phySPACE space-certified and optimally robust drives are built to withstand high levels of vibration, resist radiation and high temperatures as well as meet the demanding requirements for use in an ultra-high vacuum environment. Other factors in consideration include optimised weight, low magnetic radiation and of course, complete reliability.
Image: Model of the seismometer used on NASA’s InSight Mars lander with Phytron motors deployed for levelling
Mclennan has worked with Phytron for several years, providing product and service support as a specialised motion component supplier and as a system integrator where the German Mittelstand- and AirCert-certified manufacturer’s products have been applied across manufacturing & test, process industries, scientific research and deep space. For more information on Phytron’s product range visit www.mclennan.co.uk
Key Points
- With no contact and thus wear between rotor and stator components, stepper motors the preferred drives for challenging environments
- For many harsh and extreme environment applications it is often necessary to custom modify standard products
- Typically motors and geared actuators for high-energy physics include stainless steel or titanium materials for housing, flanges and internal parts
- Integrated servomotor with built-in Industrial Ethernet interface
- JVL 4.5kW MAC servomotor available from Mclennan
- MDX+ integrated servo drives available from Mclennan
- Matched Motors & Drives
- Mclennan safeguards manufacture & supply of SmartDrive D- & DM-series Eurocard stepper drives
- New microstepping drive range with multiple communication options
- Full featured microstepping drive is a real space saver
- Miniature stepper-gearmotors & user-configured drive
- IP65 rated
- Precision linear actuators feature roller screw and grooved roller bearings for unparalleled power and force