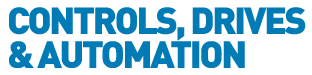
![]() |
Charlotte Stonestreet
Managing Editor |
Home> | POWER TRANSMISSION | >Linear | >Keeping heavy loads moving without cage creep |
Home> | MACHINE BUILDING & ENGINEERING | >Machinery | >Keeping heavy loads moving without cage creep |
Keeping heavy loads moving without cage creep
09 March 2022
WHEN IT comes to incorporating a crossed roller linear rolling guide into a motion system, machine designers often have to weigh up its ability to carry a heavy load against the risk of cage creep.

As the name suggests, these specialised guides use cages with alternately crossed cylindrical rollers between two V-shaped ways that act as track grooves to allow loading in any direction. The cage separates the rollers to prevent rubbing friction and drag, to ensure both smooth and highly accurate linear motion.
Over time, a conventional crossed roller assembly may see the cage develop 'creep'. It is particularly prevalent in vertical orientations where gravity acts against the cage. As a result, the cage tends to drift to one side and potentially incur skidding or hitting of the end stops, which can cause cage deterioration, bending, cracking or even damage to the machine itself. No operator wants to shut the machine down for repair or cage reset.
To combat cage creep, linear guide manufacturers have added mechanisms to their crossed roller devices. One successful approach adds a rack and pinion to the crossed roller way assembly. This keeps the cage's position in its proper place while also supporting high-speed movement. However, some crossed roller way guides have limited load-carrying abilities.
IKO International builds on the speed and accuracy of the rack and pinion mechanism by increasing the bearings' rigidity to accommodate higher loads. The company has reduced the pitch between the rollers of its CRWG...H Series crossed roller linear guides, enabling more rollers to be incorporated into the assembly. The added rigidity from the extra rollers results in dynamic load capacities that range from 525N to 35,700N in stroke lengths from 3 mm to 148 mm, depending on the model and size (1.5-mm roller diameter to 4-mm roller diameter).
This anti-creep crossed roller bearing now makes it possible for designers to incorporate a crossed roller linear rolling guide that not only solves cage creep, it also handles greater load capacity while reducing machine size and extending the lifetime, says the company.
- New technology lets humans & autonomous robots understand each other
- PPMA GROUP INDUSTRY AWARDS
- Record growth at Technidrive
- Oil pressure
- Three layers of predictive maintenance
- Solution for integrating self-driving cars into real traffic
- Drum drive range expanded
- Expanded Pioneer Safety Group appoints MD
- Partnership to accelerate development of AI solutions for future mobility
- AMP Institute receives funding boost