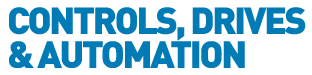
![]() |
Charlotte Stonestreet
Managing Editor |
Home> | AUTOMATION | >Networks | >Chips, Bricks & Modules |
ARTICLE
Chips, Bricks & Modules
08 October 2024
The market for industrial networking is now over 20 years old, and has changed beyond recognition. However, far from the expected rationalisation, there are more networks and protocols than ever, says David Folley, general manager, UK and Eire, HMS Industrial Networks
MORE FROM THIS COMPANY
- Monitor & control
- New PCI cards
- 2017 industrial network market shares
- HMS offers Netbiter under eWON brand
- Secure remote configuration
- M-Bus sensors connected
- Cloud-based remote management
- IIoT gateway & remote access router
- HMS Networks and Red Lion Controls join forces
- EtherNet/IP to PROFIBUS DP linking device
RELATED ARTICLES
- ONE-WIRE DIGITAL AV NETWORK
- Now With Digital Interface
- CC-LINK STARTER KITS
- FOOD & BEVERAGE ACCOLADE
- TOP-LEVEL SECURITY
- Networking Options Extended
- ARE YOU READY FOR…THE INTERNET OF THINGS?
- Community Growth
- Yokogawa joins Friends of the Supergrid
- BACnet support for building services applications as standard
OTHER ARTICLES IN THIS SECTION