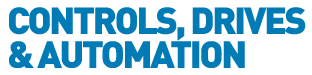
![]() |
Charlotte Stonestreet
Managing Editor |
Home> | DRIVES & MOTORS | >Maintenance | >Current developments in motor monitoring |
Current developments in motor monitoring
22 April 2016
After bearing problems, electrical faults are the most common cause of motor failure. Yet many organisations ignore electrical testing when they select condition monitoring strategies for the motors that run their plants. Michael Herring, Channel and Platform development manager, Electric Motor Condition Monitoring at SKF explains why they shouldn’t
Modern electric motors offer high levels of energy efficiency and reliability. Yet they can and do fail in service. As companies increasingly adopt condition-based maintenance approaches in an effort to reduce unplanned downtime, motors usually feature prominently on their lists of critical assets.
Gaining a full picture of the health of an electric motor requires the use of a number of different tools and techniques, and it requires good record keeping and data analysis so slowly developing trends can be identified. The tool maintenance teams will use most is vibration analysis. Vibration can identify 60 to 70 per cent of the issues that can eventually cause motor failure, including problems with bearings, unbalanced loads and shaft misalignment.
To identify a large portion of the remaining 30 to 40 per cent of potential problems, however, teams must make use of electrical testing techniques. These tests fall into two broad categories: static tests, conducted on a motor when it is not running, and dynamic tests, conducted on the motor in service.
Static testing
The majority of the electrical failures in motors begin with a weakening of the thin insulation around individual wires in the motor coils. This is typically caused by thermal stress, contamination and movement of the winding due to the magnetic forces during start-up and shut-down of the motor. Static testing uses industry accepted standards to identify the weaknesses within the motor windings. Tests are typically conducted from the motor control cabinet, which ensures electrical faults outside the motor itself – such as in junction boxes or external cables – are also identified.
A sequence of tests is conducted to measure the winding resistance and the insulation resistance to earth, as well as the turn-to-turn and phase-to-phase insulation condition. As this insulation degrades, the inrush of voltage during motor starting can cause arcing, further degrading the insulation and creating a conductive carbon path that will eventually lead to a short circuit and complete failure. A special test known as a surge test is used to detect weak turn-to-turn insulation before a short occurs. Winding resistance and insulation resistance tests cannot detect turn-to-turn weakness.
If static testing is like an annual health check, dynamic testing is the equivalent of monitoring an athlete during a race – giving the chance for both instant feedback and long-term advice.
Portable dynamic motor test equipment, such as the SKF Dynamic Motor Analyzer - EXP4000, gathers voltage and current information and uses special algorithms to assess the quality of the power supplied and certain issues within the motor, such as cracked or broken rotor bars. State-of-the-art equipment like this can also provide torque information, both in real time and as a spectrum across a pre-determined frequency range. This provides information on the driven load, and helps distinguish a mechanical problem in the wider machine from an electrical problem in the motor.
Dynamic testing should ideally be performed as frequently as vibration analysis, and more frequently than static testing. Poor power quality, for example, can cause overheating, which can destroy insulation within a motor. For this reason, it is vital to identify and correct power quality problems as early as possible.
Dynamic testing is most often performed using portable test units, which makes sense as the tests are performed ‘in the field’. However, there is an increasing trend towards permanently installed online motor analysers such as the SKF Online Motor Analysis System - NetEP, which monitors multiple motors on a continuous basis.
Online systems allow data to be accessed centrally, at any time, which helps technicians and managers make better decisions – and much more quickly. Alerts can flag up the need to investigate or replace a critical motor, while trend data from months of monitoring can help to prioritise maintenance planning. Tens or even hundreds of critical assets can be monitored automatically with such systems. As an added bonus, these types of online dynamic analyser can improve safety, by removing the need for technicians to visit hazardous areas.
Key Points
- Vibration analysis can identify problems with bearings, unbalanced loads and shaft misalignment, which can eventually cause motor failure
- Other problems are identified using electrical testing techniques, which can be static or dynamic
- Many electrical failures in motors begin with a weakening of the thin insulation around individual wires in the motor coils
- SKF & Imperial College London extend relationship
- Spherical roller bearings cut maintenance costs
- Enables higher rail freight loads
- White etching cracks: causes & mitigation
- Automation changes the face of maintenance
- SKF Commences Civil Action Over Counterfeit Bearings
- Magnetic system
- SKF launches software centre for condition monitoring
- Bearing with food safety features
- Super-precision bearing system
- MAINTENANCE PRODUCTS GUIDE
- COOL, CALCULATED EFFICIENCY
- Grease: how to avoid economic meltdown
- Lubrication
- Robot improves motor inspection
- Comparator & Measuring System
- Commissioning motors for reliable and efficient service
- ERIKS launches multi-level reliability service
- Partnership to deliver digital monitoring
- Decreasing bearing failures with WEGscan