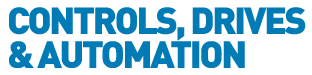
![]() |
Charlotte Stonestreet
Managing Editor |
Home> | AUTOMATION | >Robots | >Safe collaboration |
Safe collaboration
13 June 2016
As collaborative robots continue to gain popularity, CDA's consulting editor Andy Pye looks at the safety challenges which need to be addressed
In recent years, we have seen the emergence of collaborative robots - or Cobots - that are easier to program and that can work alongside humans. In contrast to traditional robots, which cannot operate in an operator-occupied workspace without safety fencing, these cage-free robots can work side by side with humans on shared or separate tasks.
The term “collaborative robots” usually refers to power and force limited robots that are all equipped with force sensing. This means that in any situation they can feel an abnormal force and stop their motion immediately. Although they still cannot avoid a crash, they can reduce its impact and avoid certain types of incidents, like crushing accidents.
Although safety requirements are not fixed yet, several countries with stringent safety regulations, such as Germany, have adopted collaborative robots in their production lines with excellent results.
At the PPMA Total Exhibition coming up in September, on the Pacepacker Services stand, a Fanuc Robotics Cobot will work alongside a caged cell containing a conventional Level 3 robot, with no safety fences.
Whilst most other collaborative robots are encased in a sensing cover that stops the robot when a human gets too close, Fanuc’s s collaborative robot ensures safety through the use of intelligent sensors, which automatically stop the robot if it touches a human operator. This means the CR-35iA can go closer to the jig and other peripherals when required.
Importantly, the human-safe CR-35iA Cobot has a 35kg payload, opening up applications that have previously been off-limits for both traditional industrial robots and lighter duty collaborative robots. With health and safety regulations stipulating 25kg as the maximum load a human operator may handle, there is a real requirement for a robot to handle higher loads than this.
Bosch is also using connected sensors to enable operators to work in conjunction with robots where the automated machinery has “awareness” of the operator.
This collaboration of man and machine relies on the Bosch APAS Assistant product, an industrial robot fitted with a sensor skin which detects the proximity of a worker. The operator can therefore work safely within the working field of the robot, since the arm slows down when it detects proximity and comes to a complete halt when it detects close proximity. The robot arm automatically restarts its cycle when the obstruction is cleared.
However, Cobots do still present new safety concerns. There is a thin line between a safe and unsafe robot. According to Stewart Robinson, Principal Engineer and Functional Safety Expoert at TÜV SÜD Product Service, the increased need for adequate protection of people from the safety risks associated with industrial robot systems led to the development of an international and European standard which has two parts.
EN ISO 10218-1:2011 Robots and robotic devices - Safety requirements for industrial robots - Part 1: Robots; and
EN ISO 10218-2:2011 Robots and robotic devices - Safety requirements for industrial robots - Part 2: Robot systems and integration.
In order to ensure that humans are not exposed to unacceptable risks when working collaboratively, the current standards describe four separate measures that can be used to provide risk reduction. It is required that at least one of these is fulfilled.
- SAFETY-RATED MONITORED STOP: this requires that when it is detected that a human has entered the collaborative workspace, the robot should be stopped.
- HAND GUIDING: the human can guide the robot at the end effector by hand.
- SPEED AND SEPARATION MONITORING: the robot must maintain a specified separation distance from the human and operate at a pre-determined speed.
- POWER AND FORCE LIMITING BY INHERENT DESIGN OR CONTROL: the power and force of the robot actuators need to be monitored by safety-related control systems to ensure that they are within limits established by a risk assessment.
Levels of robot safety
The national bureau of standards defines three levels of safety sensor systems in robots:
- Level 1 --- perimeter penetration detection
- Level 2 --- intruder detection inside the workcell
- Level 3 --- intruder detection in the immediate vicinity of the robot.
Key Points
- Collaborative robots – or Cobots – can work side by side with humans on shared or separate tasks without safety fencing
- Although safety requirements are not fixed yet, several countries with stringent safety regulations have adopted collaborative robots in production lines
- Increased need to protect people from safety risks associated with industrial robot systems has led to development of two part international and European standard
- Government moves forward on advanced trials for self-driving vehicles
- HAI ROBOTICS celebrates 5th anniversary
- 2022: a watershed year for AI adoption
- Flexible alternative to conveyor-based sortation
- Eight pioneers chart a sustainable future for UK manufacturing
- Ericsson & Porsche rev up for 5G future
- UK Digital Twin Centre opens in Belfast to drive nationwide industrial innovation
- Call to action to upskill on offshore wind robotics
- Mercedes-Benz acquires YASA
- Industrial robot market to surpass $56,171.4m by 2033
- Balls to Gravity
- ROBOTS GIVE FASTER CELL TOOL CHANGE TIMES
- ROBOT FOR DELICATE ASSEMBLY
- NUMBER OF ROBOTS IN UK ON THE RISE
- The future is bright - The future is automation!
- High Demand For Grant
- More Capacity, Less Space
- FREEBIRD - THE THIRD DIMENSION
- PRECISION ROBOT CELL FOR THE PHARMACEUTICAL INDUSTRY
- ROBOT SALES REACH ALL TIME HIGH