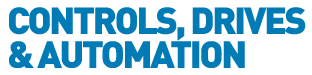
![]() |
Charlotte Stonestreet
Managing Editor |
Home> | MACHINE BUILDING & ENGINEERING | >3D Printing & Prototyping | >Pronto Prototypes For Full Testing |
Editor's Pick
MORE FROM THIS COMPANY
OTHER ARTICLES IN THIS SECTION
![]() |
Charlotte Stonestreet
Managing Editor |
Home> | MACHINE BUILDING & ENGINEERING | >3D Printing & Prototyping | >Pronto Prototypes For Full Testing |