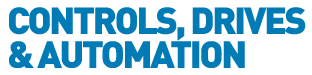
![]() |
Charlotte Stonestreet
Managing Editor |
Home> | AUTOMATION | >Robots | >Flexible application essential for full potential |
Flexible application essential for full potential
22 August 2024
From load carrier to colleague to team player: the role of robots has changed dramatically over the past seven decades. AI is creating more possibilities, but humans remain the determining factor, says Peter Lange

Robots or humans – who will determine production in the future? Industry and business stakeholders have been discussing this question for many decades – ever since the American inventor George Devol filed a patent for a programmable manipulator in 1954, thus heralding the birth of industrial robotics. The Unimate robot developed by Devol was used in a General Motors factory to remove hot metal parts from a die-casting machine – a dangerous task humans had previously carried out.
Looking back over the past 70 years of industrial robotics, it is clear that it is not about robots “against” humans, either then or now. Instead, the focus has always been on the team equation “robot + human = efficiency”. What has changed, however, are the demands of producers, the market, and the environment: flexibility, scalability, adaptability, and sustainability have never been as important as they are today. But also consider this: the tasks that robots take on are always the jobs we let them do so that human employees can concentrate on truly value-adding tasks.
One in four industrial companies plans to invest in automation
To illustrate the importance of modern industrial robotics, it is worth looking at current studies. Scientists at Stanford University have calculated that there are currently over 3.4 million industrial robots worldwide. According to analyses, the global ratio of robots to people in the manufacturing industry is 1 to 71. Industrial companies also plan to invest a quarter of their capital in industrial automation over the next five years. The development of industrial robotics is characterized by numerous technological advances, a broader application in various industries, and the integration of new approaches such as artificial intelligence (AI) and machine learning.
Cobots are becoming colleagues
At the same time, a paradigm shift can be observed: whereas in their early years, robots were seen primarily as useful devices that could take on repetitive and heavy tasks in particular, the idea of the robot as a colleague – without the previously required protective fences – has become increasingly important with the advent of collaborative robots (cobots). The principle of cobots was developed in the 1990s, the first models came onto the market at the beginning of the new millennium, and since around 2010 cobots have become indispensable in many areas of manufacturing. In addition, products and manufacturing processes need to be increasingly traceable. With the help of robotics, production, packaging, and inspection processes can be traced and quantified much more transparently and reliably than before.
Repetitive tasks are given to cobots
The success story of collaborative robotics began in Scandinavia, especially in Denmark and Sweden – countries that have had to try for a long time to cover the lack of skilled workers, who are also very expensive, with technical support. Palletizing is a prime example of collaborative robotics in this context – a repetitive, uncreative, and non-value-adding task that can be easily taken over by technology instead of by humans. In contrast, human employees can use the time they have saved to take care of more important and complex tasks.
Trend cognitive robotics: NEURA Robotics and OMRON cooperate
This new type of interaction between humans and technology has even gone further in recent years, with increasing harmonization in manufacturing automation. The integration of AI and machine learning is creating progressively adaptive and learning robots that learn from their experiences and thus optimize tasks. This enables flexible adaptation to different production requirements. In addition, robotics is more and more being trained with the support of AI to imitate human senses and cognitive connections. In this area, OMRON is collaborating with NEURA Robotics, a global pioneer in the field of cognitive robotics. The partnership aims to transform the manufacturing industry by introducing cognitive robots in factory automation and advanced AI functions to improve efficiency, flexibility, and safety. Unlike conventional industrial robots, cognitive robots can learn from their environment, make independent decisions, and adapt to dynamic production scenarios. This opens up new application possibilities, including complicated assembly tasks, detailed quality control, or adaptive material handling.
The key to success: adaptability
Modern cobots, on the other hand, are working side by side with human employees in a safer, more natural, and seamless way. Advances in sensor technology and safety software have enabled and spread this interaction. The Internet of Things (IoT) in Industry 4.0, on the other hand, has led to the networking of robots and production facilities, enabling comprehensive automation and real-time monitoring. Not to forget improvements in hardware and precision, which benefit reliability and performance. In addition, modern industrial robotics is simpler to program than ever, making it easier to implement and use in smaller companies. Current requirements, especially for medium-sized companies, are to be able to respond flexibly to new requirements. Robotics must therefore be able to adapt effortlessly and flexibly to different applications to respond quickly to changing production requirements.
Potential vs. challenges
Technological advances and innovations have significantly increased efficiency and flexibility in manufacturing in recent years. At the same time, however, there is a wide range of challenges to be overcome to fully exploit the potential of robotics. These include optimized integration into existing processes, a well-thought-out coupling of IT and OT, scalability, cost efficiency, data security, comprehensive employee training, and the clarification of organizational and structural issues.
Conclusion: humans must remain in command
A recent study by the Technical University of Berlin, for example, suggests that people who work closely and frequently with robots come to rely more and more on their performance over time and no longer consistently recognize errors and inaccuracies. This too is an aspect that should be given more attention in the future. At the same time, however, more and more robotics is needed to operate more productively and efficiently, to mitigate the increasing shortage of skilled workers, and to make processes and companies more sustainable. For this to succeed, future robots must be able to act more like humans, while at the same time becoming simpler and more adaptable. This does not mean that human employees will be replaced. Instead, their tasks will change: today's plant operator will become a robot operator. The robot takes over the heavy and often also mind-numbing tasks, while the human remains in command. For decision-makers, this means that all the important parties, IT, operators, and so on must be brought on board from the outset in order not to torpedo the successful introduction of innovative robotics.
Peter Lange is business development manager robotics at Omron Electronics
- End-of-line automated
- Cobot innovation resolves redeployment challenge
- Omron's solutions support TheOpenVentilator
- UV-C Robot helps fight against COVID
- Robotics & the potential for the lights-out factory
- OMRON completes panel solutions line-up with 237 new models
- Flexible & intuitive operation
- High-efficiency control for almost any AC motor type
- Machine interface
- OMRON appoints Reeco Automation cobot solution partner
- Balls to Gravity
- ROBOTS GIVE FASTER CELL TOOL CHANGE TIMES
- ROBOT FOR DELICATE ASSEMBLY
- NUMBER OF ROBOTS IN UK ON THE RISE
- The future is bright - The future is automation!
- High Demand For Grant
- More Capacity, Less Space
- FREEBIRD - THE THIRD DIMENSION
- PRECISION ROBOT CELL FOR THE PHARMACEUTICAL INDUSTRY
- ROBOT SALES REACH ALL TIME HIGH