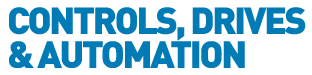
![]() |
Charlotte Stonestreet
Managing Editor |
Home> | IIot & Smart Technology | >Big Data | >Making the connection |
Home> | IIot & Smart Technology | >Connectivity | >Making the connection |
Making the connection
06 July 2022
Connected manufacturing goes way beyond simply collecting data, asserts George Thompson, chairman of the British Automation and Robotics Association (BARA)

THERE ARE lots of different names for the process of connecting different parts of the manufacturing process together and collecting relevant data from the various pieces of equipment in order to measure the Overall Equipment Effectiveness (OEE). Some of these names are Industrial Internet of Things (IIoT), Industry 4.0, Smart Factories, Connected Manufacturing, Big Data, and Interconnectivity to name a few. Irrespective of what it’s called, it is effectively the same thing. But there is FAR more to it than just collecting data and creating graphs that get filed away just in case someone wants to look at in the future. For this article, I will refer to the process as Connected Manufacturing.
Establish a starting point
I have often asked what potential customers want to capture and the most common answer is ‘how much can I get?’ My reply is typically, to guide them to what the business NEEDS to capture to help with planning. I often suggest that they write a ‘job description’ for the automation as if it was an employee and then decide what Key Performance Indicators (KPIs) they would normally assign for that role. Now we have a starting point! This is not a final definitive list, but more of a starting point.
As anyone that knows or has worked with me, I am a fan of the whole Six Sigma / Kaizen process. Just in case you are not familiar with the process, it sets out a continuous improvement process where you Define, Measure, Analyse, Improve, Control and then start over. It should be a truly continuously developing situation, however don’t make snap decisions. REALLY analyse the data – find the root cause of any patterns that become apparent, then apply the continuous improvement methodology to that portion of the production process. Before long, relevant data is being collected from the entire process and this is where Connected Manufacturing comes into its own.
With more equipment connected, it is possible to introduce line balancing. This is where the various pieces of equipment communicate and share information – one part indicates that it may be starved of product – or perhaps it’s over saturated with product due to an unplanned stoppage – or maybe it just can’t keep up with the flow. The line PLC would then either slow down or speed up some parts of the line so they continue to work at a reflective rate instead of coming to a stop.
Waste reduction
The other advantage of Connected Manufacturing in my opinion is the potentials of reducing waste. By balancing the lines around the slowest part of the process, any time critical parts of the process can be managed more closely – or by selecting a different component to be indexed to a different part of the product flow – if that is a possibility. The possibilities are dependant on the industry, the process but most importantly, the budget available to make the changes. If you are just making a start into the world of Automation, please don’t be overwhelmed. Get good advice from a few good reputable integrators and take the best bits to further develop your specification. The end result will be much closer to what you need to improve your production process.
If you would like to start your automation journey, but don’t know where to start – I would highly recommend visiting the BARA web site detailed below, where we have outlined several topics under the Expert Advice section to give some initial information. While you’re there, why not register for our next Roundtable discussion. You could also watch some of our previous Roundtables again as there is likely to be just the information you have been searching for contained within the discussions.
- Inspired solutions!
- Automation UK 2024 doubling in size to meet exhibitor demand
- Why supply chain development is critical to automation adoption
- Automation influences
- We need to automate more!
- High Demand For Grant
- BARA announces ‘Safety Benefits of Robots for Dangerous Tasks and Environments’ roundtable event
- RMGroup becomes the UK’s first certified robot integrator
- Not all integrators are created equal
- Automating UK supply chain from the top down
- The digital future has begun
- Transmission of Data to Cloud
- Secure data handling
- Makes IoT available in practice
- Education key to unlocking I4.0
- Complete solution for IO-Link
- Cables for data-intensive IIoT environments
- Smart sensor technologies
- Trelleborg joins Smart Data Innovation Lab
- Easing entry to smart manufacturing