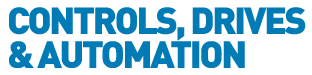
![]() |
Charlotte Stonestreet
Managing Editor |
Home> | IIot & Smart Technology | >IIoT | >More efficient manufacturing technology |
Editor's Pick
More efficient manufacturing technology
24 February 2020
Infusion 4.0, a project funded by the German Federal Ministry of Economics and Energy, shows how effective fiber-optic sensors are in monitoring the vacuum infusion process during the production of large composite components.

Together with its project partner, MT Aerospace AG, the Fraunhofer Institute for Structural Durability and System Reliability LBF has made the previously-hidden process steps visible and digitally controllable, thereby increasing process reliability. This new, efficient manufacturing technology supports reliable and fast development of aerospace products.
Using CFRP booster housings, MT Aerospace AG in Augsburg, Germany, manufactures large CRFP components (carbon fiber-reinforced plastic) using vacuum infusion processes. In vacuum infusion, a dry-wrapped pre-form is inserted in a vacuum bag and is infiltrated with resin while slowly rotating in an oven. Intelligent sensors are required in order to monitor the flow front of the in-flowing resin and to optimize processes. Scientists from Fraunhofer LBF and their industrial partners are embedding fiber-optic sensors into the component as early as the winding process in various 3-dimensional positions. These then control resin distribution during this important production step.
Digital twin
Each sensor fiber contains several of the more than 60 glass fiber sensors. The flow front is the line when the resin first gets in contact with the dry fibers. The signals are transmitted from the rotating part in the oven to an outside computer in situ in order to digitally monitor the process. A digital representation of the sensor position on the component shows when the flow front reaches the sensor. “We are receiving transparent information for the manufacturing process of these thick-walled parts for this first time. This increases process reliability for vacuum infusion processes,” explains Martin Lehmann, Research Associate at Fraunhofer LBF.
The new manufacturing process makes previously hidden processes visible and digitally controllable, thereby increasing process stability. Information gained by resin flow monitoring ensures reproducibility and quality of the new product, enabling timely intervention if required during production. Production ramp-up can be accelerated with this improved control. This increases the company’s competitiveness.
Integrated sensors
In addition, the new technology makes future automated control of manufacturing processes in Industry 4.0 possible. Integrated sensors provide structural monitoring (structural health monitoring, or SHM) even from the earliest phase of the product lifecycle.
This Infusion 4.0 project idea won third place in the Innospace Masters Challenge offered by the German Aerospace Center (DLR) in 2017. It was a finalist at the 2018 German Aviation Innovation Award for research needs in this environment. The project’s successful completion in October 2019 confirmed the Darmstadt scientists’ approaches as well as those of their Augsburg colleagues.
- NatWest Group to lend additional £1b to support net zero
- Sage report into UK manufacturing sector
- Belting for peak season
- Second profit warning of the year from Renishaw
- UK tech that ‘teleports’ humans into robots in finals of global robotics competition
- BCIA releases new Technical Guide: The Impact of Controls on the Energy Efficiency of Buildings
- HIMA Group acquires Sella Controls
- Technology to help contain threat of Covid-19
- Machinery regulation gets an update
- Non-chemical precision robotic weeding
- Industry 4.0 ready
- What operators need to know about IIoT adoption
- Predictive maintenance leader
- The digital future has begun
- The smart future of manufacturing
- Partnership integrates freight & warehouse management
- Secure data handling
- Makes IoT available in practice
- When & where will Industry 4.0 actually happen?
- Simplifying IIoT & product suite understanding