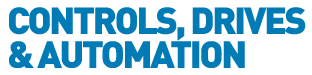
![]() |
Charlotte Stonestreet
Managing Editor |
Home> | DRIVES & MOTORS | >Inverters | >SERVO INVERTER FOR MULTI-AXIS APPLICATIONS |
SERVO INVERTER FOR MULTI-AXIS APPLICATIONS
21 September 2012
With reduced space requirement, a lower number of components, and easier assembly and cabling, Lenze’s new i700 is reported to significantly boost productivity
The i700 from Lenze has been designed for multi-axis applications, and simplifies machine design, build and commissioning. In addition to an easy assembly concept, the new drive system is reported to be remarkably compact and flexible: double axis models ensure that the volume of the drives is a minimum, while dynamic motor control permits a wide range of applications.
With intuitive software tools and a central engineering interface, the i700 can be integrated into automation architectures through EtherCAT. Together with the 3200C controller, originally launched at the SPS/IPC exhibition in November 2010, it constitutes the heart of the Lenze Controller-based Automation System for machines with central motion control.
The new servo inverter comprises single-axis and doubleaxis modules for the power range 0.37 to 15kW, along with appropriate power supply modules. The power supply modules do not usually require any filtering or DC fusing and are factory-fitted with a braking chopper. The intermediate electrical connections between the i700 drives are made without a cable, using an innovative rail system, and are easily installed by setting connector arms.
The reduced space requirement, lower number of components, easier assembly and cabling of the i700 combine to offer a significant boost to productivity. The i700 was designed for engineering using only one interface. Automatic download of parameters and firmware, along with auto-tuning functions, ensure fast commissioning.
SHORT CYCLE TIMES
The i700 supports the full spectrum of motor technologies, from standard three-phase up to synchronous servomotors.With extremely short cycle times (250 microseconds for positional control), a signal resolution of 32 bits and an overload capacity of more than 200%, the new servo inverter is as well-suited to highly dynamic, precise, multi-axis applications. Examples are those found in handling and packaging machines or robot applications, as well as simple positioning tasks. The i700 is available with a variety of cooling technology options – cold plate, push-through technology and panel mounted units.
The integrated safety functionality also simplifies the machine design. "Safe Torque Off” (STO) is provided as standard, while future variants are planned in order to implement extended safety networks, offering, for example, SS1, SS2, SOS, SLS, SDI or SLI, and which achieves the highest safety level (SIL 3, PL e) over EtherCAT (FSoE).
Essential connectivity is covered in the 3200C controller. There are two 100MBit Ethernet interfaces with integrated switch. This means that an external switch which would be otherwise required when setting up a line topology is no longer needed. A third Ethernet interface is reserved for operation as an EtherCAT master, ideal for precise real-time communication with servo and inverter drives.
Thanks to its modular design, further communication buses can be added. Lenze offers expansion with two synchronised CAN buses that can support CANopen. In addition a PROFIBUS card is available. Since the PROFIBUS and EtherCAT interfaces operate in parallel, the new controller is particularly suitable to upgrade systems automated with PROFIBUS by maintaining connections with no changes and adding the modern and fast motion control bus EtherCAT.
Key Points
- The i700 drive system can be integrated into automation architectures through EtherCAT
- Supports the full spectrum of motor technologies
- Integrated safety functionality
- Understanding friction torque limiters
- Secure data handling
- The future of machine programming is FAST
- Energy saving servo drives
- Intelligent automation systems
- Lenze boosts training
- Automated handling design & support
- Smart & geared motor launches
- Customised gearboxes
- Cyber security in mechanical engineering