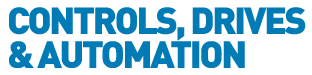
![]() |
Charlotte Stonestreet
Managing Editor |
Home> | DRIVES & MOTORS | >Electric Motors | >Complete drive train savings |
Complete drive train savings
07 May 2013
With the continued rise of energy costs, electric motors are recognised as an important element for reducing electricity bills. But, according to Lenze, the electric motor itself is only part of the picture...
Electric drives are responsible for about one-third of electricity used in Europe. According to the German trade association ZVEI, the energy saving potential in electric motors is 10%. However the saving potential with frequency inverters is three times higher, and that for optimising the complete drive train is six times higher. The real saving potential comes from looking beyond the motor to the drive elements that are connected with it.
The technology needed for these energy savings is available today, and is proven and reliable. Methods of applying the technology are easy and accessible. An initial investment is usually needed, but payback times are remarkably short, often less than one year. This article looks at the whole drive train, looking at the obvious places where energy savings can be made but also some new and less obvious places.
International efficiency classes
The majority of electric motors used in industrial machinery are standard AC asynchronous designs with an average power in the region of 11kW. Current European regulations require them to meet the IE2 efficiency level which will increase to IE3 in January 2015. A higher level of IE4 is on the horizon. What have these new regulations achieved? The table below illustrates typical efficiency values for 4 pole motors at three typical powers:
Power | Old IE1 efficiency before 2011 |
IE3 motor efficiency from 2015 |
1.5kW | 79% | 87% |
7.5kW | 87% | 92% |
40kW | 91% | 94% |
Typical efficiency gains are between 3 and 8% and these gains can be directly related to energy usage. At first glance the numbers look small and relatively insignificant. However the savings are significant – for a 7.5kW motor running 5000 hours a year they represent £190 a year with a payback on the additional motor costs in about 6 months. From there on the savings are a profitable reduction in overheads for the machine operator. The extra cost of meeting the regulations are well worthwhile, even complying in advance of the date, but there are ways to save much more.
Connected to the motor is often a gearbox. Selection of the wrong type can waste much more money than was gained with an energy efficient motor. Worm gearboxes may be quiet and low cost, but they are also inefficient. They should only be used for drives that run infrequently. Changing to a bevel, planetary or helical gearbox will achieve 94 to 98% efficiency depending on size and ratio. The energy savings can easily be as much as 25%. The initial cost is higher but payback periods will be less than one year. In the example below where the power requirement is 1.0kW, an inefficient gearbox will require a 2.2kW motor whilst a gearbox with 95% efficiency can be driven with a 1.1kW motor.
Inverter drives bring in opportunities for large energy savings. However they should not be used where the speed and load are constant as their own losses will reduce the system efficiency. Large savings are well known in pumps and fans. These are always designed to satisfy the highest demand (maximum attendance, hottest day…) whilst actual demand is normally lower, sometimes by a large percentage. If the inverter lowers the average speed in response to actual demand by as little as 20%, the reduction in electricity bills is a massive 50%. There are many more applications where turning down the speed in response to load is appropriate, for example conveyors, revolving doors and escalators. These can be slowed or even stopped when there is low demand. A frequency inverter can handle the control and give huge energy savings.
There are cases where the machine speed needs to remain constant but the load varies. Consider an airport luggage system which can be full of suitcases or at another time empty. The nature of asynchronous motors is that their efficiency falls at low loads. This is particularly true below 40% load, and as much as one third of the efficiency can be lost at 20% load. The reason is that the magnetisation current that produce the magnetic flux in the motor remains high as the load reduces. Yet today there are frequency inverters that include software algorithms that can adjust the magnetisation current in proportion to the load. In applications where the load varies but speed is unchanged, savings up to 30% are possible and at zero or minimal cost.
In some cases the motion in the application puts energy back into the drive motor. Examples are crank mechanisms, stopping of high inertia loads, vertical motion in cranes, hoists and lifts, also robotics and winding. Historically the common solution here was to dump the energy as heat into a brake resistor. This may heat the surrounding air but really is a waste of energy. Today there are three better options:
- if there are two or more axes where one is regenerating whilst others use power, the DC bus in the drives can be connected. This means the braking energy charges the DC bus and the drive that is motoring can then take the energy from the bus. The result is a reduction in the power taken from the mains. Typical applications are in winding and storage/retrieval units, and the savings can be 40% or more.
- the braking energy can be stored in a capacitor, a similar concept to flywheel storage, and re-used in the next operation. This particularly suits fast cycling drives such as cross-cutters and the energy saving potential is 50%.
- the surplus energy can be returned to the mains supply, just like a domestic feed-in tariff. A regenerative unit is needed to turn the DC energy in the drive into 230VAC. This is particularly effective where the energy generation is for a longer period such as with winding applications. Regenerative units have a significant cost but they can be economic, particularly for drives above 5kW.
So there are many options to choose the optimum energy efficient components in a drive train. This leads on to the next step of sizing the components where all the gains can be wiped out through incorrect selections. For best running costs combined with small size and low maintenance, the drive should match the requirements of the application. Not too big, not too small, just right. Very few cases are simple to assess. A solution to this problem lies in selection software that can provide numeric evidence.
A software tool called DSD Drive Solution Designer brings many benefits here. It looks at the entire drive train, single- or multi-axis, and brings together product data with real-life application experience. Standard cases are prepared with motion formulae and additional features such as inertia calculators. Variations in ambient conditions are allowed for. Each drive is optimised and graphical displays show how close they are for their performance limits. It is easy to compare alternatives on performance and cost. Finally there is the output of an Energy Certificate that details lifetime costs. DSD is available for 6 months free trial and also it is free to Universities. Alternatively it can be implemented on site by the manufacturer. Of course every case is different and the powerful optimisation available from DSD is a significant factor in reaching the 60% levels of energy saving proposed by ZVEI.
Saving energy is good for the environment but it needs to make business sense too. Electric motors used in industrial machinery offer the biggest potential for savings and the technology is in place to exploit them. The secret is to look at the whole drive train from the inverter to the motor and the gearbox. Accurate selection and use of the appropriate products is essential if the high levels of saving identified by ZVEI are to be achieved. Generally extra investment will be paid back in a short time. Machine users should demand efficient drive trains and evidence of reductions in their running costs. Machine builders should use the same evidence as a key benefit to increase their sales.
Key Points
- Real saving potential comes from looking beyond the motor to the drive elements that are connected with it
- Changing to a bevel, planetary or helical gearbox can result in energy savings up to 25%
- If an inverter lowers average speed in response to actual demand by as little as 20%, the reduction in electricity bills is 50%
- SERVO INVERTER FOR MULTI-AXIS APPLICATIONS
- Baggage handling solution
- Smart & geared motor launches
- Torque limiters for heavy-duty machinery
- Fully scalable frequency inverters
- Meet the challenge of warehouse automation
- Lenze celebrates 50 years in the UK
- New stock partners for frequency inverters
- Secure data handling
- Intelligent drive tailored for conveyors
- JOINT WIND ENERGY GENERATORS VENTURE
- Washdown Motors
- Engineering Talent Search
- Cooling System & Frame Optimised
- Sustainable Motors
- WEG motors & drives power high-efficiency air blowers
- Stainless Motors For Washdown Environments
- IECEx Certified
- Configurable Online
- Explaining the different types of AC electric motor