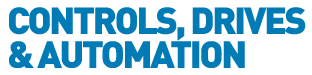
![]() |
Charlotte Stonestreet
Managing Editor |
Home> | POWER TRANSMISSION | >Brakes | >Optimising Safety Brakes |
Optimising Safety Brakes
02 October 2012
Different applications for electromagnetic safety brakes require different design approaches. Hermann Bestle of Mayr Transmissions explains how wind turbines and machine tools differ
Electromagnetic safety brakes, also called spring-actuated brakes, function according to a fail-safe principle. When they are de-energised, even on emergency stop and during power failures, these brakes are closed. If the magnetic coil is energised, a magnetic field is produced which releases the brake against the force of the integrated thrust springs.
After releasing, a far lower voltage is required to keep the brake open reliably, which allows operators to operate the brake in open condition at lower voltages, thus saving a great deal of energy during operation.
During the development of its electromagnetic safety brakes, Mayr Power Transmission has optimised the magnetic flow through construction design and selection of materials so that the required magnetic tensile force can be achieved with as low a coil power as possible. Optimum dimensioning of the magnetic coils and designs optimised for magnetic flow are also important aspects.
OPTIMALLY ALIGNED
The brake and the control have to be optimally aligned with one another – standard rectifiers are not suitable for this purpose. On these, mains alternating voltage and rectified coil voltage are always in fixed relation to each other. Therefore, new electronic wiring units have been developed for brake electromagnets which work using switchable voltages.
On switch-on, the electronics energise the brake temporarily with a high voltage in order to attract the armature over the air gap. Once the armature is lying against the magnetic body, the voltage is reduced.
Using this procedure, voltage conditions between releasing and holding of up to 3:1 are possible. If the voltage is reduced after release of the brake to a third of the nominal voltage, the coil power is reduced and therefore also the energy consumption by approximately 89%. Optimum wiring therefore provides enormous optimisation potential.
The standard series insulation system for Mayr safety brakes is suitable for control with electronic wiring units. If appropriately dimensioned, electromagnetic brakes by other manufacturers can also be controlled using Mayr DC voltage modules while saving energy at the same time. In addition, it would be possible to retrofit the majority of brakes already installed and operating without voltage reduction, which are still wasting an unnecessary amount of energy.
The fields of application for safety brakes in which energy savings are a top priority are increasing. One classic example of this are small, gearless wind turbines without pitch systems, meaning that the rotor vanes cannot be turned to ‘flag’ position and thus taken out of the wind during unsuitable wind conditions.
One such small turbine with, for example, 3kW nominal power, achieves approximately 1kW of continuous output as an annual average. In order to brake this turbine to the specified switch-off speed reliably and to stop it, a brake is needed with approximately 600Nm braking torque. The standard holding capacity of such a brake totals approximately 100W. This already amounts to 10% of the power fed into the small turbine. By using an appropriately modified, energysaving safety brake and a matching electrical circuit with a Mayr DC voltage module, the holding capacity drops to below 10W. Due to this immense improvement in the degree of efficiency on the turbine, 9% more power can be fed into the mains.
The operation of a safety brake with reduced voltage has other positive advantages. The reduced power means that the magnetic coil heats up less and therefore requires less surface to dissipate the heat into the surroundings.
This means that the magnetic coil can be smaller.
TIMED TO PERFECTION
The amount of iron and the number of copper coils in the magnets determine their induction and also affect the switching response times. Using this effect and the possibilities provided by an adapted electronic control,switching times can be achieved which were not previously possible on standard controlled brakes. The connection time until the full braking torque is reached could be shortened with a concept brake of this kind by up to 70%, and the attraction time when releasing the brake by 40%.
On the ROBA-stop-M fastswitching brake, this positive sideeffect becomes highly important.
These spring-applied, electromagnetic fail-safe brakes are installed in machine tools on the ball screw spindle in the bell housing. The brake is dimensioned to minimise the generation of heat through the magnetic coil.
By controlling the brake via the ROBA-switch 24V control unit, the power consumption could be reduced by a further 75%.
Although the fast-switching brake is directly installed on the ball screw spindle, the heat generated by the coil power can be neglected, and does not affect the accuracy of the machine. Operating costs can also be reduced and the environment protected due to the cuts in power consumption.
The main focus on this application, however, is the extremely quick switching behaviour of the brake. On power failure or emergency stop, the fall path of the carriage is crucial. This fall path is primarily dependent on the brake switching times. It has therefore been optimised especially for very short switching times. Halving the switching time reduces the fall path by 75%. In many cases, this is sufficient to prevent critical damage to machine components or workpieces after a power failure.
Energy-saving does not start with the operation of a system, but rather with the initial development of a product. On electromagnetic safety brakes, constructional design and selection of materials should optimise the magnetic flow so that the required magnetic tensile force can be achieved with as low a coil power as possible.
Through optimum design of the magnetic coils and a construction which accommodates magnetic flow, the material input for a brake can be substantially reduced.
However, by far the largest potential for saving energy is when the product is in operation. The utilisation of all control-technological possibilities without making compromises can reduce power consumption on safety brakes by up to 90%.
On a ROBA-stop-M safety brake Size 1000, the savings made in energy costs therefore add up to approximately 100 EUR per year, assuming 3000 operating hours at an energy price of 0.20 EUR per kilowatt hour. Many million such brakes or similar ones are used daily. The possible savings potential is truly gigantic.
Key Points
- The fields of application for safety brakes in which energy savings are a top priority are increasing
- New electronic wiring units have been developed for brake electromagnets which work using switchable voltages
- Using all control-technological possibilities can reduce power consumption on safety brakes by up to 90%
- Pitch & YAW Brakes For Wind Power
- High performance in a compact design
- Shaft Couplings for High Torques
- Intelligent brake control
- Power transmission specialist
- Reliable torque limitation
- Reliable monitoring of safety brakes in servo systems
- Reliable protection for high speeds
- Intelligent control for brake technology 4.0
- Backlash-free servo couplings