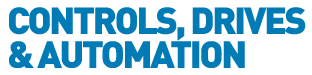
![]() |
Charlotte Stonestreet
Managing Editor |
Single source energy-efficient synchronous powertrain
12 June 2018
Together with two of its subsidiaries, WEG has developed a complete drive with a synchronous motor at its core. The result: a powertrain based on a permanent magnet motor that can be customised precisely to customer needs. WG20 gear units and CFW11 variable speed drives complete the drive system
Any areas of application where electric motors are in continuous operation place high demands on the lifetime of the drive technology used. The significance of high efficiency levels, even in the partial-load range, is becoming increasingly important in terms of overall energy saving. For example, energy-efficient motors, gear units and control units with a high protection class are required in the textile industry; these need to have a long lifetime for use at high speeds, thereby ensuring high operational safety. Drive systems put together from components made by different manufacturers are often used here.
WEG subsidiary, Württembergische Elektromotoren, has developed a new synchronous motor range with a rated output of 0.12 to 3kW, which comes with speed feedback in its standard form. This range of motors has been designed for demanding industrial applications and can be operated as both open-loop (without feedback) and closed-loop (with feedback), thanks to its electrical configuration.
The new four-terminal permanent magnet motors exceed efficiency class IE4 (Super Premium Efficiency) in all operating modes – both open-loop and closed-loop – and achieve efficiency levels of over 90% across a broad range of speeds with rated torque of 1 Nm to 10 Nm. This means that they comply and, indeed, exceed the required standard for small drives of 0.12 to 3.0 kW and the synchronous motors will be available in four sizes – 6, 7, 8 and 9 – as of summer 2018. They are characterised by excellent speed accuracy and high dynamics as the result of high overload capacity and low individual mass moment of inertia.
Depending on size, the rated torque of the motors is 1.2 Nm, 2.8 Nm, 5 Nm or 10 Nm. All the motors can cope with 3.5x overload. Depending on size and optimised mass inertia adjustment (iopt. = JExternal / J Motor = 1:1), acceleration takes between 13 and 53 ms.
Continuous operation
For applications such as 24/7 continuous operation in the textiles sector or the continuous use of pumps and dosing pumps, using synchronous motors is the best solution. This applies particularly if they run at a high efficiency level in continuous operation across the entire speed range and can be controlled by a control unit. The main disadvantage of permanent magnet motors – their higher investment costs compared to asynchronous machines – can be offset in these cases by significant savings in energy costs, thanks to their shorter operating periods.
Along with a high current/torque and torque/volume ratio, the synchronous motor technology offers a more compact design and better dynamics than asynchronous technology. IE4 permanent magnet motors that are one size smaller than their equivalent asynchronous motors can provide the same level of performance. Württembergische Elektromotoren uses standardised readily available components as the basis for its synchronous motors. This covers an incredibly wide range of usage requirements.
Various different housing forms and add-ons for the new synchronous motor range are also possible: when it comes to mechanical design, for example, users can choose between non-ventilated or ventilated smooth housings and ridged housings made from lightweight aluminium. Thanks to its modular system, the synchronous motor can also be customised to individual customer needs, from the terminal box to the connector.
The synchronous motor range can be combined directly, without motor adapters, with the WG20 gear units manufactured by Austrian gear unit specialists Watt Drive, also part of the WEG Group. The elimination of motor adapters not only saves on cost, but prevents the mass moment of inertia on the motor shaft from increasing any further. With its helical, parallel shaft and helical bevel gear units, the WG20 range is the ideal addition to synchronous motors. Thanks to their pinion design, the WG20 gear units are easy to adjust for optimum implementation and can often be arranged as two-stage units as a result of this alignment.
Eliminating one gear stage further reduces total losses, which results in particularly high energy efficiency. The WG20 gear units offer efficient power transmission and can be combined with synchronous motors in energy efficiency class IE4 to create drives with high power density. Their mountings, in line with market requirements, ensure that they can be exchanged anywhere in the world without user machine modifications.
Control units
CFW11 variable speed drives are used as the control units for the synchronous drive. They cover rated voltages of 220 V to 480 V (50/60Hz) and an output range of up to 3 kW in normal operations. Designed exclusively for industrial/professional use, the high-performance high-end devices in the CFW11 range contribute to process optimisation and increase productivity as part of a powertrain. The CFW11 offers a range of helpful and useful functions, particularly in terms of simple configuration and operation and the variable speed drive supports both voltage vector control (VVW) and control using U/f control characteristics. WEG's technology provides outstanding response characteristics, precise torque and speed control, accurate positioning and high overload capacity.
For use in safety-critical applications, WEG also integrates numerous protection functions with fault and alarm indications in the variable speed drives, as well as EN ISO 13849-1 safe shutdown – Safe Torque Off (STO), Category 3/PL d (as an optional module). The CFW11 housing is available in protection class IP54. What’s more the series supports the Modbus-RTU (RS232 and RS485), CANopen, DeviceNet, Profibus-DP/DPV1, Profinet, Modbus-TCP, Ethernet/IP, Ethercat and BACnet communication protocols as standard.
All the drive components of the synchronous solution were designed for optimum use together, both in terms of mechanical and electrical aspects and can be combined on an application-specific basis. This means that users get a product that fulfils their own application needs exactly, providing them with a long-lasting drive solution from a single source, including guaranteed service routes and shorter delivery times. The complete drive train – consisting of a synchronous motor, WG20 gear units and CFW11 variable speed drive – combines the drive know-how of the WEG Group with the motor expertise of Württembergische Elektromotoren GmbH, the development and manufacturing skills of Watt Drive and the global sales and service network of WEG.
Key Points
- WEG subsidiary, Württembergische Elektromotoren, has developed a new synchronous motor range with a rated output of 0.12 to 3kW, which comes with speed feedback in its standard form
- The synchronous motor range can be combined directly, without motor adapters, with the WG20 gear units manufactured by Austrian gear unit specialists Watt Drive, also part of the WEG Group
- CFW11 variable speed drives are used as the control units for the synchronous drive; they cover rated voltages of 220 to 480V (50/60Hz) and an output range of up to 3 kW in normal operations
- WEG and AMT form collaborative partnership
- WEG acquires industrial electric motors and generators business from Regal Rexnord
- Modular global motor
- Energy reduction initiative
- Decentralised drive package
- Tough & dynamic synchronous motors
- VSDs vs. soft starters
- Frame size H VSD
- Bringing legacy DC motors into the digital age
- Large explosion-proof motors