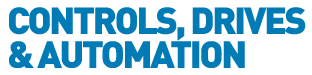
![]() |
Charlotte Stonestreet
Managing Editor |
Home> | DRIVES & MOTORS | >Controls | >New four-phase method for motor control |
Editor's Pick
New four-phase method for motor control
26 October 2022
ENGINEERING AND electrified propulsion systems specialist, Drive System Design (DSD), has pioneered a new four-phase method for motor control development.

The process is intended to reduce time, spend and improve the design and development of electric motors and inverters, with the potential to save clients upwards of £100,000 by mitigating risks earlier in the testing process and saving months of time in test cell development. The method can be used in a range of industries including aerospace, automotive, commercial vehicle and off highway, and defence.
In the typical motor and inverter prototyping method, prototype development hardware is often taken directly to a dynamometer (dyno) test cell; later, critical issues may be uncovered, which can stop the program in its tracks. With this seemingly direct approach, months can be added to the project timelines in order to find and fix unforeseen integration issues.
The method, consisting of four key phases, ensures a more robust, reliable concept before the dyno test cell phase. The test cell is typically the most expensive and complex part of the development method, so by identifying and fixing issues before this stage, it has the potential to save months of time and significant financial cost within the development and testing process.
DSD, with a 90-strong team in Leamington Spa and a US-based office, pioneered the new method for those in motor development within aerospace industries. It will now be implemented for many of DSD’s electric vehicle projects, 10% of which are focused in the aerospace space, with market leading OEM clients in the aerospace space.
The new four-phase method will help organisations to improve the speed, robustness and reliability of the testing process for motor and control elements, helping to mitigate risks and assess fault tolerance ahead of certification.
As an initial investment to fulfil this new motor development strategy, DSD acquired a C-HIL rig, which will be housed in its US technical centre in Michigan. This can be remotely accessed and controlled, giving its UK and Europe teams full use of the technology, and there will be frequent collaboration between the UK and US teams.
The launch comes as DSD marks its 15th year in the UK and celebrates ongoing growth both in the UK and internationally. Its 155% rise in overseas sales was recently recognised by the Queen's award in International Trade.
Murry Edington, head of electrified powertrain at DSD commented: “There is immense benefit in minimising project risk by following our four-phase method. Too often, a push to be first-to-market ends up incurring more cost and time. In our experience, typically 50% of projects involving motor control validation face delays due to motor integration challenges, and we wanted to change this.
“Ultimately, this method will enable system developers to be first-time capable, meaning they will be set up for a successful pairing of the inverter and motor once the product reaches the dyno test cell. This will speed up final validation and significantly reduce the risk of needing major software iteration or hardware revision, saving our customers both time and money while delivering a higher quality system.”
“Real-world issues can now be predicted or reproduced and solved prior to – or in parallel with – dyno or test cell work. This new approach and equipment will further advance DSD’s turnkey capability to deliver motor controls and electrification across a range of markets.
“Given the potential value of taking a more comprehensive approach to motor control and associated hardware development, the company believes those undertaking such projects will adopt a similar method in the next five years, as electrification continues to accelerate across a huge array of applications.”
- Augmented reality in manufacturing
- Ultra high-speed telemetry for motorsports
- Businesses given more time to apply new product safety marking
- INEOS to build hand sanitiser plant in 10 days
- Tax sponsor for Manufacturing & Engineering Week
- Airbag safety system for robots
- Emerging tech driving circular economy
- How condition monitoring improves reliability
- New robotics venture
- AI model generation service
- Expert Advice
- Control Panel Products
- Miniaturised Controllers
- Control Without Speed Reduction
- TRUE THERMAL MODELLING
- Standard & Customised Precision Motion Control
- Medium voltage (MV) motor control solutions
- Drive selection on the Internet with the maxon selection program.
- KEB COMBICONTROL C6
- Integrated evaluation kit