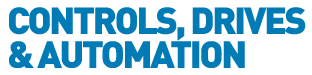
![]() |
Charlotte Stonestreet
Managing Editor |
Home> | DRIVES & MOTORS | >DC Motors | >Rossi UK Aftermarket Repairs |
Home> | DRIVES & MOTORS | >Geared Motors | >Rossi UK Aftermarket Repairs |
Home> | POWER TRANSMISSION | >Gears | >Rossi UK Aftermarket Repairs |
Rossi UK Aftermarket Repairs
15 February 2013
When searching the web for a suitable industrial gearbox and geared motor repair centre within the UK it appears that the customer is spoilt for choice. However Rossi UK believe that very often, this choice is limited, as many of these repair centres are not authorised by the OEM and therefore the repair is carried out at higher risk to end user and could lead to incurring additional costs.
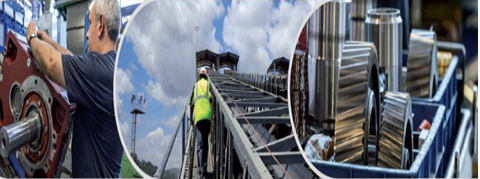
Rossi as the OEM for all of its comprehensive product range has invested a significant amount of time and money in the design and manufacturing process for each component used in a Rossi geared motor or reducer. The risk of using untested substitutes is not considered as this puts the reputation of the Rossi brand at risk and could also have a negative impact on the performance of the product which in turn could cause significant losses in production for the customer.
For more than 60 years, Rossi has been developing its business in the most demanding applications, becoming one of the world’s leading gearbox specialists in key strategic segments. All Rossi repairs are supported with a 1 year warranty linked to workmanship and/or faulty parts.
Throughout Rossi’s history the focus has been on providing a commercially attractive, technically compliant product selected according to the needs of the customer and ensuring that through the design, manufacturing and assembly phase the final product will conform to the customer’s expectation. This philosophy remains as the foundation for Rossi UK focus on supporting the After Market within the United Kingdom.
As a company we ensure that the processes behind our After Market Service are identical to the manufacturing and assembly procedures for new equipment. As such Rossi UK has invested in tooling to service the G series helical bevel and helical parallel units up to size 225 (approx. 20000NM).This includes an assembly turntable workbench and a 100ton press. All our fitters undergo assembly training according to Rossi’s global assembly standard and further investment in the IT processes specific to recording each and every step of the repair process has been implemented.
Further investment in local stock holding of components has also been undertaken to improve delivery times of repairs. Components not in stock local can be ordered via a special order basis of 24/48/72 hour from the factory subject to availability and dispatched accordingly. Rossi IT systems, allows for real time part stock level identification from any of its global locations.
Rossi’s technical knowledge and experience can provide root cause analysis on the failure. Then together, with Rossi Industry segment managers, and the customer, they can establish corrective measures to prevent future failures from occurring in the existing application.
Additional "After Market Services" include; oil analysis, photographic record of all failed components, final inspection reports and limited test running of the units prior to dispatch.
Rossi UK, will arrange to collect and dispatch a repair to anywhere within the United Kingdom
- Synchronising asphalt batch mixing
- Fits existing parameters
- Planetary Units From Stock
- New servo gear reducer range
- Batch mixing synchronised
- Gear reducers for mining & aggregates
- Ambitious investment
- Deck Machinery & Planetary Gearboxes
- INCREASED PERFORMANCE FROM PLANETARY REDUCERS
- Rossi relocates to add value