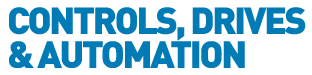
![]() |
Charlotte Stonestreet
Managing Editor |
Home> | AUTOMATION | >Systems | >Energy management benefits cannot be ignored |
Energy management benefits cannot be ignored
08 May 2013
Chris Evans, marketing & operations group manager at Mitsubishi Electric, looks at implementing an energy management strategy and how existing automation control architecture can be used to help deliver significant energy savings
Many customers tell us that one of their biggest business costs is energy, so it would seem obvious that tackling and improving the problem would be the natural thing to do. However, this ignores the pressure of producing product and satisfying customer’s demands, which all manufacturers face on a daily basis.
An argument often heard is that the energy bill is seen as a ”sunk cost”, or that it is the necessary evil endemic in the production process and that "it is what it is.” The solution is often seen as merely negotiating the best tariff from the supply authority, but this approach fails to recognise the opportunities that lie dormant within the existing automation control architecture to identify areas for improvement and, with some investment in energy management, to deliver significant energy and cost savings.
Perceived obstacles
Some of the perceived obstacles to implementing an energy management system include cost, ROI and disruption to the production process. Indeed, this perception alone is often enough to prevent any further discussion in favour of continuous production needs. The counter argument to this must be the widely reported view that adopting a holistic approach to energy management can return savings of up to 30% – and surely this possibility cannot be ignored.
Another interesting fact is that a reported 20% of the UK’s total energy usage centres on industrial processes and that 60% of that energy is consumed by electric motors. A typical production plant consists of a variety of machines, often containing electric motors of various sizes, and these are usually linked together by conveyors and handling systems, again brimming with electric motors. It is a well-trodden argument that says fitting variable speed drives (inverters) to electric motors will save energy. This is easy to see on a machine where the motors are large but on a conveyor, for example, the motors tend to be much smaller and the effect harder to see. If this argument is indeed accepted then why is it that many motors on many plants do not adopt any form of energy reduction techniques?
Implementing intelligent control of plant equipment will create the possibility to dictate how it operates. This illustrates the difference between energy saving and energy management. Fitting an inverter to a fan or pump motor will save energy, but understanding the energy usage of the production facility leads to the possibility of implementing an energy management control strategy.
How often are machines left to run during production downtimes or during extended breaks? Fitting an inverter to a conveyor and controlling the inverter from the line control system means that decisions can be made to, for example, reduce the conveyor speed during downtimes (reducing speed saves energy) or switch off completely if that is the most appropriate decision. These decisions can be made intuitively by the overall control system and could be linked to production planning if we take it to the next stage.
Cost/benefit
Getting to the lofty heights of total energy management will seem a long and expensive road to anyone who has minimum or zero energy saving already implemented but like all good strategies it can be implemented in stages, evaluating the cost/benefit analysis along the way.
The first place to start is to know what the current situation looks like. To implement this stage will certainly require some investment and this will depend on the control level network architecture that already exists. Programmable controllers (PLCs), inverter drives and other control equipment are perfectly capable of offering up a raft of energy information. They may not have been programmed to deliver this when installed but by engineering over and above the existing control program the information can be easily accessed. This extra engineering can be non-intrusive and does not have to affect the control program already present. Communication of this information can then be transferred across the control level network to a dedicated energy monitoring package, where full analysis can take place.What if no control level network exists? The choices are in essence either implement one, or deploy metering on the perceived "hotspots” to directly feedback the energy information. A properly thought out and costed strategy will no doubt include both of these techniques, in whole or in part.
The importance of this monitoring phase cannot be underestimated as this information will be vital in determining the next phase of the project. It is also highly likely during this phase that some behavioural problems will come to light, for example, perhaps a particular shift tends to leave machines running and others don’t. Simply implementing a procedural change can often give immediate improvements and cost savings. Even if this approach seems rather piecemeal, it should be implemented as part of the "bigger picture” from the beginning as taking the holistic view will deliver the best results and the greater savings long term.
Problems identified
Problem areas will be defined from this analysis and suitable actions can be taken. This will range from fitting inverters, as previously discussed, to implementing a full energy management control strategy and all points in between.
It is vital that you engage with an automation supplier who can provide audits, proposals and have the capability of delivering a total solution.
At Mitsubishi we can deliver a number of advantages. Our inverter drives include an optimum excitation control (OEC) feature which can deliver up to 12% extra energy saving over and above the standard energy saving available from an inverter drive. We have our Energy Control Pack which can provide a wireless metering solution for gathering energy information and our MX4Energy software solution allows total energy management of assets and the production environment.
MX4Energy is also capable of monitoring non-electrical utilities such as oil, gas, water etc., providing a total site management system. Couple this with our adoption of open network technologies and this means that the Mitsubishi energy management solution can be added to the production facility regardless of the preferred automation supplier at the control level. Added value services can be provided from our System Service Group including energy surveys and audits, and project integration from our network of approved service agents and system integrators.
It is perfectly understandable why manufacturers are so concerned about achieving production targets, sometimes at the expense of all other considerations. However, energy is a considerable cost to any business and any strategy that can reduce that cost by up to 30% has to be considered. It is proven that for relatively small levels of investment, significant savings can be made and it is clear that the cost of doing nothing will outweigh the cost of taking action.
Key Points
- Perceived obstacles to energy management include cost, ROI and disruption to production
- Strategies can be implemented in stages, evaluating the cost/benefit analysis along the way
- PLCs, inverter drives and other control equipment offer up a raft of energy information
- Backup & Restore
- Terminal block technology guide
- MID-RANGE PLC BRIDGES THE PERFORMANCE GAP
- Robots take their pick in plastic moulding application
- Wind(ings) of change
- Food chain traceability
- AI improves maintenance management for robots
- Transparent Link Between Automation Components & PCs
- Energy from waste technologies
- The immediate future of automation in the food industry
- SWISSLOG SECURES MAJOR ORDER
- IMPROVED PERFORMANCE & RELIABILITY
- Engine Facility
- BULK AUTOMATION
- Integrated Packaging Solutions
- INTEGRATING ELECTRIC AND PNEUMATIC CONTROLS
- Rockwell Automation expands Midrange system portfolio
- Yokogawa joins Friends of the Supergrid
- Festo extends reach of VTUG and MPA-L valve terminals
- Siemens extends TIA Portal engineering framework