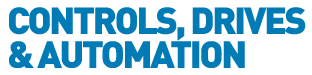
![]() |
Charlotte Stonestreet
Managing Editor |
Home> | POWER TRANSMISSION | >Actuators | >A question of application |
Home> | AUTOMATION | >Actuators | >A question of application |
Home> | CONTROLS | >Actuators | >A question of application |
Editor's Pick
A question of application
27 August 2013
Many commentators claim that electric actuation, motion and control technologies are cheaper, more environmentally friendly, more energy efficient and easier to work with. So what does the future hold for hydraulic and pneumatic technologies? Steve Sands, product manager at Festo challenges the myths that one media is more energy efficient than another.
It is too simplistic to say that electric drives are more energy efficient than pneumatics without considering the application and whether the technology is being applied correctly. If either pneumatic or electrical drives are applied incorrectly they can be inefficient and waste energy. Only a direct comparison of two correctly dimensioned drives – one electric and one pneumatic, being operated effectively – can reveal the advantages and disadvantages of the technologies. It almost goes without saying that poor practices resulting in wastage should be eliminated through good knowledge and skills within the workplace.
Each industrial application has its specific requirements with regards to technical criteria such as speed, acceleration, load capacity and force required, cycle time, holding duration, power to weight ratio, accuracy, control behaviour, torsional rigidity, efficiency or robustness. Both pneumatic and electric technologies have specific advantages and disadvantages as outlined in table 1, which is why it doesn’t make sense to make bland statements on the benefits of a technology, when energy efficiency wholly depends on the task at hand.Taking some simple examples; testing and measurements reveal that for a simple motion task, an electric drive can be efficient. For a pressing or clamping operation, the level of process force and the duration of the operation decide which technology is more efficient. However, if the application requires a holding force, pneumatics is clearly at an advantage.
Clear definition
For example, comparing electric and pneumatic grippers shows how choosing the right solution depends on a clear definition of the task If we consider the energy consumption during the gripping process, a pneumatic gripper will be superior to an electric gripper in applications involving long cycles and with just a small number of gripping operations.
A pneumatic gripper requires pressure only once to initiate continuous holding. No more pneumatic energy is consumed or required for the duration of the gripping operation. However, an electric gripper needs electricity for the entire duration of the gripping operation and can be more energy-efficient than a pneumatic gripper only if the application in question is composed of short cycles with many gripping operations.
For applications which require large holding forces for extended periods, pneumatics has a major advantage compared with electric drives which require constant electricity consumption to generate power.
The following rules of thumb can generally be applied: the shorter the stroke length, the greater the end position force and the longer the holding duration, the more efficient pneumatic technology is. In contrast, the greater the stroke length, the lower the end position force and the shorter the holding duration, the more efficient electric drive technology is.
Overall efficiency
It is important to bear in mind that a technology cannot be selected based on energy aspects alone; other properties including purchase cost, ruggedness, weight, the environment, installation costs and operating costs play an significant part and must be incorporated in the decision making process. A lighter-weight pneumatic gripper can reduce the moving mass of all the actuators throughout a handling system, dramatically reducing the overall energy requirements. It’s clearly better to have an efficient overall system rather than focus on the efficiency of the single components.
Efficiency can only be achieved through understanding the application, technologies and the technical product data to optimise the solution. In summary, there is a place for both pneumatic and electric drives as the most energy efficient selection is application dependent. There is no quick-fix solution for increasing energy efficiency of the system as it must be viewed in an overall context and parameters must often be looked at in detail to provide final data on potential efficiency, savings and economy. Festo has recently published a report entitled ‘EnEffAH’ which evaluates the energy efficiency in production in the drive and handling technology field, which is free to download from www.festo.co.uk/energyreport.
Key Points
- To compare electric and pneumatic technologies correctly dimensioned drives must be considered
- Generally, the shorter the stroke length, the greater the end position force and the longer the holding duration, the more efficient pneumatic technology is
- The greater the stroke length, the lower the end position force and the shorter the holding duration, the more efficient electric drive technology is
- Putting disabled drivers in control
- The smart way to milk
- Easy swap from one PLC manufacturer to another
- Design cartesian robots in minutes
- Fast & reliable configuration of process valves
- A real Industry 4.0 solution
- Linear motor track system
- Packaging system concepts
- Automated biomass cultivation
- Save costs when selecting process valve solutions
- VALVE ACTUATION SUPPORTS OFFSHORE WIND FARM
- Lightning Strike Solution
- MAINTENANCE FREE FOR 10 YEARS
- Extends Operating Life & Reduces Maintenance Costs
- Selecting linear actuators for single and multi-axis positioning
- New IVAC Guide
- Modular Platform
- Rigid Linear Drive Guides
- Tritex II™ AC Powered Actuators
- Exlar GSX Series