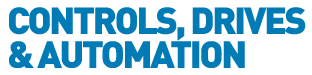
![]() |
Charlotte Stonestreet
Managing Editor |
Home> | DRIVES & MOTORS | >Variable Speed Drives | >Ironing out reliability issues |
Editor's Pick
Ironing out reliability issues
19 February 2014
Park Laundry, Scarborough's largest commercial laundry, is achieving more reliable speed control of a calender ironing machine following the installation of an ABB variable-speed drive.
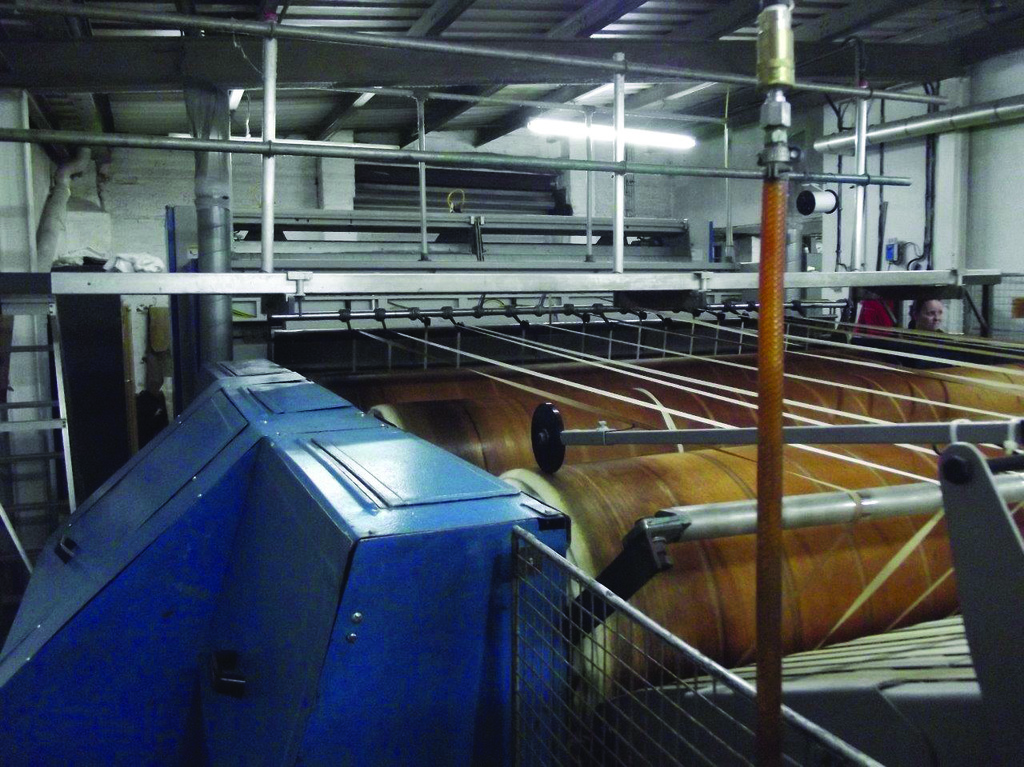
Typically in operation for nine hours a day, the machine was originally operated using an old slip ring motor, with speed control provided by an auxiliary servo motor. With spares becoming harder to source, the company was considering replacing this motor when it suffered a sudden failure.
Electrical contractor Eclipse Electrical Engineers was contacted for a replacement motor. Eclipse offered a new induction motor and contacted Halcyon Drives, an ABB authorised value provider, for a speed control solution.
The machine consists of a feed-in belt section that sends newly washed items to three 18 inch diameter heated metal rollers, driven from the motor by a chain. These iron the items and send them to the final section for folding. Speed control is vital as the items vary in size from domestic towels and clothing, to commercial laundry items from hotels and restaurants such as napkins, table cloths and king sized bed sheets. These hold different amounts of water and although they are spun dry, they are still damp so need to be ironed at different speeds.
The drive solution supplied by Halcyon Drives incorporates a 15 kW ABB general purpose, ACS550, variable-speed drive together with sensors on the feeder and folder that feedback to the drive to synchronise the roller speed. The drive was also supplied in an enclosure rated to IP54 to prevent the ingress of moisture from the damp working environment of the laundry.
As well as the improved reliability and better availability of spares, the new drive and motor combination is also more efficient than the previous arrangement, though as they have been installed only a short time, it is too early to tell how much they have saved in energy costs although the first electricity bill after installation is noticeably reduced, some due to working less hours but some definitely due to improved efficiency of the unit.
- PUMPED UP PERFORMANCE
- SOFT STARTER OR VARIABLE SPEED DRIVE?
- Jeans With Less Energy
- Enhanced to Withstand Tough Environments
- Savings From Improved Torque Ratio & Efficiency
- Modular VSD
- ENERGY SAVING: AN OLD MESSAGE WITH NEW PROMISE
- Updated installation guide for power drive systems
- UK drives manufacturer seals global automation deal
- WEG motors & drives power high-efficiency air blowers