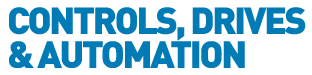
![]() |
Charlotte Stonestreet
Managing Editor |
Home> | CONTROLS | >Motion Controls | >Turbine blade pitch control |
Home> | INDUSTRY FOCUSES | >Renewables | >Turbine blade pitch control |
Editor's Pick
Turbine blade pitch control
02 May 2014
Moog’s self-sensing closed-loop pitch speed control for wind turbines enables synchronous motors to be used for pitch systems, since it can keep them under closed-loop speed control even if there is a failure in the motor position feedback. This avoids high turbine loads that would otherwise result from non-synchronised pitch speeds in the turbine in traditional approaches.

This self-sensing closed-loop speed control feature is only one of the benefits built into the new AC Pitch Axis Servo (PAS) concept from Moog. The new interior permanent magnet synchronous (IPMSM) motor was specially designed for the pitch application.
It ensures maximum efficiency at low speeds during pitch operation and a peak torque capability of up to 3.5 times nominal pitch torque, even at grid fault condition. The motion control concept guarantees a wide field weakening operation area in order to fully control the feathering speed, even under grid loss condition.
- VALVE ACTUATION SUPPORTS OFFSHORE WIND FARM
- HARMONIC CANCELLATION
- MAKING WAVES WITH TOUCHLESS TECHNOLOGY
- Integrated Motion Control
- As Long As The Wind Blows
- New 4th Generation PH Series Servo Planetary Gears are Largest in Class and offer Engineers even more benefits
- Yokogawa Joins Friends Of The Supergrid
- Driving Trends & Developments
- EtherCAT I/O is Tightly Integrated into Aerotech's A3200 Automation Machine Controller
- Galvo and Controller Combination Offers Infinite Field of View and 24-Bit Resolution