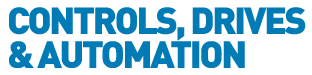
![]() |
Charlotte Stonestreet
Managing Editor |
Home> | POWER TRANSMISSION | >Gears | >Polymers in robotic gearing |
Polymers in robotic gearing
22 June 2015
Andy Pye looks at examples of the use of advanced polymers in robotic gears from both sides of the Atlantic
Many modern high-performance engineering plastics are stronger than steel for a given size and are, of course, much lighter. They are also inherently resistant to corrosion and weathering, and the best types are unaffected by exposure to virtually every type of chemical and petrochemical, as well as by exposure to UV light from the sun.
One sub-group – the triboplastic polymers – also provides an answer to the lubrication problem - special attention has been given to optimising their frictional properties. As a result, it is now possible to construct systems from triboplastics that require no lubrication throughout their working lives.
Igus has introduced Robolink D, a direct drive joint kit that is available in three different sizes and can be combined to form customised and configurable articulated robotic arms with one to four axes. Robolink D is intended for robot manufacturers, mechanical engineers and automation specialists, working in a variety of industries ranging from automotive production to medical technology.
Each low-cost joint kit comprises a PRT polymer slewing ring bearing, which is self-lubricating and therefore maintenance free, and worm gear, which is housed in plastic for added protection while ensuring weight is kept to a minimum.
Advanced polymers
Precision gearing can also be machined from advanced polymers. If an application is running trouble-free with either traditional metal or injection moulded gears, cut polymer gears probably won’t deliver much value. But spur, helical, bevel and worm gears can be machined from gravity cast nylon, acetal and other engineering polymers, both with and without metal structural hubs.
In surgical robots, engineers may specify high precision, ground helical gears. By selecting a polymer as the gear material it is possible to reduce noise, perhaps by 6dBa. An example is a very precise polymer/aluminium helical drive that is produced by Intech in the US to AGMA 11 accuracy standards.
These gears have to run for five years without a drop of oil and a key design challenge is thermal management: with a maximum pitch line velocity of 5.2m/s, the gears would generate an excessive amount of heat within their compact housing. The design relies heavily on aluminium to dissipate heat, not only for the polymer gear hubs but also the entire middle gear.
A proprietary tooth form modification involves an increase in the pressure angle of the helical teeth. By rounding the tooth flanks for a reduction in sliding movement between mating teeth, the increased pressure angle limits friction and heat development. The pressure angle modification also increases load bearing capacity by up to 18%.
This design also significantly reduces system inertia by a factor of seven compared to steel gears, which makes the robotic system more responsive to positioning commands.
The design has virtually no backlash at operating temperatures. This would be unusual for conventional plastic gears, which typically have about twice the backlash of a comparable metal gear. To compensate for growth from moisture absorption or thermal expansion, conventional plastic gears require a substantial undercut, which in turn introduces some positioning "slop".
By producing the gears from high-performance polymers that don’t absorb moisture, and providing an integral metal core to reduce expansion at the robot’s operating temperatures, it is possible to do away with the undercut - and the backlash that goes along with it.
Energy chains
Another part of the power transmission spectrum is the energy chain, which consists of multiple elements linked with moving joints. Fabricating energy chains from high performance plastics are tough, resistant to corrosion and impact, they are lubricant-free so require no maintenance and have very long working lives. Energy chains from Igus are also available in ATEX-compliant versions.
Key Points
- Many modern high-performance engineering plastics are stronger than steel for a given size, and much lighter
- It is now possible to construct systems from triboplastics that require no lubrication throughout their working lives
- Spur, helical, bevel and worm gears can be machined from gravity cast nylon, acetal and other engineering polymers
- SCHUNK to invest 85 million euros in production sites
- Unlocking smarter manufacturing
- Hitachi acquisition to aid expansion in medical sector
- 2022: a watershed year for AI adoption
- Northamptonshire Manufacturing Week
- Food for thought
- Machine monitoring platform
- Agricultural drones & robots used for disinfection operation
- Controllers for smart surfaces & multi-function displays
- Smart power enablers