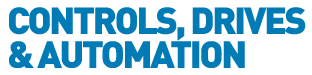
![]() |
Charlotte Stonestreet
Managing Editor |
Home> | DRIVES & MOTORS | >AC Motors | >Make motors part of your headache cure |
Home> | DRIVES & MOTORS | >Electric Motors | >Make motors part of your headache cure |
Home> | DRIVES & MOTORS | >Variable Speed Drives | >Make motors part of your headache cure |
Make motors part of your headache cure
14 October 2015
Production managers in the food and beverage industry face a number of headaches, yet with the right approach, electric motors can be part of the solution rather than part of the problem, as Dave Hawley, ABB, explains
The food and beverage industry is diverse, encompassing some 30 different industries and employing a variety of processes such as grinding, mixing, baking, chilling and distilling. Despite this array of processes, plant layouts and products, there are certain things in common that will keep the industry’s production managers awake at night: "How can I reduce my plant’s energy consumption?” "How can I get maximum uptime from my equipment?” "How can I reduce unnecessary maintenance?” "How can I cut my spares inventory?” "How can we best comply with food safety standards?”
When considering these issues, production managers may be tempted to focus on assets such as bottling plants, centrifuges and mixers, but there is a more fundamental component that often does not get the attention it deserves. This is the workhorse of all industry, the electric motor. Whether in cooling fans, refrigeration pumps, hot water pumping or packing lines, the electric motor is there, underpinning all the plant’s production processes. This means that getting the most out of electric motors and using them efficiently needs to be a top priority for all food and beverage plants. Getting your motors operating correctly can go a long way to curing those headaches.
Efficiency pays
The food and beverage industry operates on notoriously small margins. This means that energy costs, and ways to reduce them, are one of production managers’ biggest headaches. Generally, more efficient motors will be more expensive to buy, yet even small increases in efficiency will make a substantial saving in the overall cost of a motor, taking into account its operating and capital cost.
For example, an 11 kW motor costs, typically, under £500 to buy, yet over £50,000 to run over a 10 year operating life. The purchase price therefore, is just 1 percent of the motor's total life cycle cost.
Motors are now classed according to efficiency - IE1 Standard Efficiency, IE2 High Efficiency and IE3 Premium Efficiency. Working near full load, a typical 11 kW IE3 motor will be around 1.6 percent more efficient than an IE2 equivalent. When considering a new investment in process machinery, it could be worthwhile asking your OEM what efficiency class the motors are.
Some motor manufacturers are pushing the boundaries still further. The magnet-free IE4 synchronous reluctance (SynRM) motor technology launched by ABB is a motor that is robust, has no windings and practically no operating losses. Using variable-speed drives to control motors can add further substantial energy savings.
Simple measures such as switching off a motor to save energy when it is not actually being used to process product can also be effective. Motors left running when not required waste a significant amount of energy - even under no load, motors can consume as much as 40 percent of full load power.
Reliability doesn’t just happen
Another concern of production managers is reducing the spares inventory they carry. It’s all very well having a spare motor for a critical process which would lead to unacceptable loses in perishable stock if it was interrupted, or if a production problem would cause a loss of faith with a major supermarket customer. However, you don’t want to have large amounts of capital tied up in spares for other less critical machines just because you cannot rely on the motors they use.
Reliability comes through choosing motors designed for a high availability. They have windings, bearings, laminations, connections and winding encapsulation that resist wear, excessive temperatures, strain and the ingress of moisture and dust.
Yet even the most well designed and built motors need careful monitoring and management if you are to gain full benefit from them.
Manage your motors for maximum production time
Getting the most out of your motors means managing all aspects of their life and operation. A proper motor management policy will assess the installed base, upgrade existing motors, manage the purchase of new motors, establish regular maintenance and monitoring and plan for repair and replacement.
Analysing the installed base of motors gives an indication of age and efficiency levels. This will produce candidates for upgrading. The best motors to upgrade with more efficient ones are those over five years old, those repaired or rewound more than once and motors operating for more than 2000 hours a year.
When purchasing a new motor, ask your motor vendor or OEM about the motor’s reliability, what preventive maintenance it needs, how much it costs to run and the long-term support offered. You may not need a high quality, high efficiency motor for a non-critical application, which is why you should calculate the total cost of ownership for each motor. As well as purchase price and running costs, consider the cost of not-running – the lost production caused by a failed motor.
Planning for repair and replacement involves considering lead times for a new motor, the cost of a repair versus a new motor, what spares stock you want to hold and the perishability of ingredients or partly processed products.
A better maintenance plan
A major part of managing the life of motors is a proper maintenance regime. Carrying out maintenance on installed electric motors regularly is critical to ensure high levels of reliability. Yet, this needs to be carried out at the correct intervals, otherwise resources will be wasted and motors will be taken off line unnecessarily.
The trick to getting the correct level of maintenance effort is to monitor the condition of the motors. The four key motor parameters that should be measured are operating temperature, alignment, vibration and lubrication. For example, improper lubrication accounts for 80 percent of motor bearing failures, while poorly aligned direct couplings lose up to five percent efficiency and may result in premature bearing failure.
A service provided by ABB called MACHsense-P provides a comprehensive analysis of electrical and mechanical faults in the complete shaft line, including the motor, gearbox and driven loads such as fans, pumps and compressors. The system collects vibration and electrical data to address issues in crucial areas: rotor windings, power quality, installation, bearings, gear condition and driven load condition.
This level of monitoring goes a long way to improving the production time of a motor, allowing you to conduct maintenance according to a schedule, avoid reactive maintenance caused by unexpected failures and prolong the overall life of the motor.
Food safety first
Perhaps no other aim for the food manufacturer is as important as maintaining food safety standards. Cleaning of food contact surfaces is of course mandatory but it should not be forgotten that splashes, spills and condensates can end up coating the drive components of production machinery, especially if those components are usually out of sight of the operatives. As well as forming a breeding ground for pathogens, these food deposits can potentially get ingress to the internal components of an unprotected motor, causing premature failure as well as a possible safety hazard.
Stainless steel is the preferred surface for food equipment. Look for stainless steel cased motors that also offer protection features that can withstand harsh washdown features, allowing them to be cleansed with high pressure water as well as surfactants to dissolve accumulated grease.
Production managers in food plants may face headaches, but with the right approach and with the best technology and services, motors don’t have to be one of them.
Key Points
- While more efficient motors are more expensive to buy, even small increases in efficiency make a substantial saving in the lifetime cost
- Using variable-speed drives to control motors can add further substantial energy savings
- As well as purchase price and running costs, consider the cost of not-running – the lost production caused by a failed motor
- ABB VSD training moves to Bristol
- Savings for Tata Steel
- SynRM motor & VSD packages
- Total Plant Automation For Power And Water Sectors
- ABB launches Drives Solutions Team
- World's most remote robot automates Amazon reforestation project
- High performance PLC
- ABB’s Robot Podcast back for season three
- Spherical roller bearings cut installation time by up to 75%
- Production stoppages halted
- HIGH EFFICIENCY
- JOINT WIND ENERGY GENERATORS VENTURE
- PUMPED UP PERFORMANCE
- SOFT STARTER OR VARIABLE SPEED DRIVE?
- BAE SYSTEMS TEAMS WITH QINETIQ TO DELIVER HYBRID ELECTRIC DRIVE
- Efficient Drives
- Jeans With Less Energy
- Enhanced to Withstand Tough Environments
- Loher motors available in UK
- HYGIENE SENSITIVE