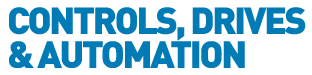
![]() |
Charlotte Stonestreet
Managing Editor |
Home> | CONTROLS | >Motion Controls | >Cabinet-free drive technology |
Editor's Pick
Cabinet-free drive technology
29 August 2023
Leading manufacturer of confectionery machines, Winkler und Dünnebier Süßwarenmaschinen (WDS) is modularising its machines with control cabinet-free drive technology from Bosch Rexroth

A MODULAR machine design has a number of advantages for confectionery machine manufacturers: Pre-installed and tested equipment saves time and money during on-site set-up. At the same time, modules which can quickly be combined to produce customer-specific solutions have valuable standardising effects. Decentralised drive technologies from Bosch Rexroth play a significant role here as they do not require a control cabinet and can be wired quickly and easily.
At interpack 2023, WDS demonstrated just how effective the new modular concept is on a moulding station for the ConfecPRO modular confectionery machine. It can fill up to 25 molds for chocolate, jelly or over-the-counter products per minute depending on the product and the equipment. This corresponds to an hourly output of up to three tons, with a dosing accuracy of only 0.5% of the average product weight.
Decentralised drive
The exacting requirements in terms of quality and productivity call not only for precision mechanics but also a powerful control system.
“In larger systems, we combine up to 120 axes and 100 drives in synchronous mold transport,” said Bernd Plies, head of digitalisation at WDS. “Each drive can have its own optimised movement profile.”
In order to achieve this decentralisation, WDS chose a combination of the control cabinet-free drive solution IndraDrive Mi and the IndraDrive MLC motion control system.
“We’ve been working with Bosch Rexroth for approximately thirty years and know of no other provider with an equally sophisticated solution that can be integrated into our machines with such flexibility and with no additional effort – including supply units in protection class IP65.”
In this type of modular confectionery machine, the IndraMotion MLC coordinates around 40 electronically synchronized transport movements with its own decentralised drive. This way, the polycarbonate molds can be transported seamlessly through the machine using a chain drive in accordance with the loose mold principle. A warming period is followed by the first molding process with liquid chocolate. Afterwards, a shell is created using the patented Flash Shell Cooling technology which is filled again, cooled and sealed. The control unit can connect the dosing unit and other individual axes as required.
Quick ramp-up
The modular design reduces the electrical installation work on site by up to 70%. The previous power and feedback lines to the central control cabinet are no longer needed. Instead, the individual drive modules are connected via hybrid cables using the daisy chain method. Compared to the previous machine generation, WDS now requires over 50 percent fewer supply and feedback cables.
In the first ConfecPRO, the control cabinet was only 1.8m long instead of 12m as it was before. The latest generation now requires no control cabinet at all. The power consumption is also reduced: Replacing the former central cooling systems with decentralized enclosures featuring filter fans reduced the power required for temperature control by a total of 7.5kW. The use of recovered energy via the DC-bus coupling of the servo system further improves the energy balance.
IIoT and digitalisation options
The many connectivity options of Rexroth’s control system ctrlX CORE as an edge device also helped to win over WDS. They range from vertical interfaces in accordance with the Weihenstephan Standards (WS) or PackML (Packaging Machine Language) to direct data access via ERP and MES systems and horizontal communication on the basis of OPC UA and WS Sweets, the new library in the Weihenstephan Standards.
Tobias Gerhard, business development fast moving consumer goods at Bosch Rexroth, explained the potential that the system offers: “M2M communication makes it possible to pass the current status on to the upstream and downstream machine. Thanks to the completely transparent value stream, the whole line can flexibly adjust to new products and situations – from the preparation and the mold system to primary and secondary packaging."
According to Plies, another advantage of the ctrlX CORE edge solution is the fact that it can easily be connected to the SweetConnect industry platform – an open platform ecosystem developed for the confectionery industry.
- Linear motor modules
- Connectivity: The future of factories
- Interactive hydraulic catalogue
- Why Industry 4.0 is an evolution, not a revolution
- Free calculation program
- Re-branded filtration range now available in the UK
- Back-Up Drive Equipment
- Bosch Rexroth to acquire Elmo Motion Control
- Helping to make machines fit for the future
- Industry 4.0 training rigs
- HARMONIC CANCELLATION
- Integrated Motion Control
- New 4th Generation PH Series Servo Planetary Gears are Largest in Class and offer Engineers even more benefits
- Driving Trends & Developments
- EtherCAT I/O is Tightly Integrated into Aerotech's A3200 Automation Machine Controller
- Galvo and Controller Combination Offers Infinite Field of View and 24-Bit Resolution
- Control systems
- Rail Coupling Minimises Downtime
- Custom Motion System For CT Scanner
- Full Servo Motion Advantages At A Fraction Of The Cost