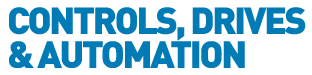
![]() |
Charlotte Stonestreet
Managing Editor |
Home> | IIot & Smart Technology | >Big Data | >Fluke integrates eMaint with Azima AI |
Home> | AUTOMATION | >Condition Monitoring | >Fluke integrates eMaint with Azima AI |
Fluke integrates eMaint with Azima AI
04 August 2025
FLUKE RELIABILITY has announced the full integration of its eMaint Computerised Maintenance Management System (CMMS) with Watchman Services, the company’s AI vibration condition monitoring solution. This new integration enables maintenance and reliability teams to seamlessly bridge the gap between asset condition monitoring and maintenance execution, improving uptime, accelerating response, and reducing costs.

When Fluke Reliability acquired Azima DLI in 2023, eMaint users began using Azima’s advanced diagnostics and AI-driven fault detection to better inform maintenance decisions. Now, with both platforms directly connected, insights happen faster, with real-time vibration data and recommendations from Watchman Services going directly into eMaint work order management.
Unplanned downtime remains one of the most expensive challenges in industrial operations, often disrupting production schedules, inflating maintenance costs, and reducing overall equipment effectiveness (OEE).
"This integration marks a pivotal advancement in industrial maintenance strategy uniting asset management and 30+ years of learned data and analytics to deliver a truly predictive approach,” said Aaron Merkin, chief technology officer at Fluke Reliability. “By connecting eMaint and Watchman Services, we’re empowering teams to act faster on the data they already have; eliminating data silos, accelerating decision-making, and enabling maintenance teams to act before failures occur. The result is a smarter, more resilient operation that reduces unplanned downtime, lowers costs and drives measurable performance gains."
Watchman Services monitors the condition of machines, sending crucial information on machine faults and failures to eMaint software. This process creates a ticket and assigns an action to a facility manager, enabling a problem to be swiftly resolved. Key features include:
- Predicting machine failure: Integrated software enables corrective and preventative maintenance activities to be scheduled in advance, before a failure occurs, often months ahead of time, by identifying early warning signs and long-term degradation patterns
- Proactive strategies: Factories and warehouses can leverage this integration to accurately forecast spare part needs for planned maintenance, optimising working capital, and reducing the risk of overstocking parts that may expire over time, crucial in an era of supply chain challenges
- Streamlined labour solutions: Built-in automation eliminates the need for end users to manually review spreadsheets or maintenance schedules by identifying issues and automatically sending tickets to the right person to act.
- IO-LInk Now Included
- As Long As The Wind Blows
- CONDITION MONITORING FOR THE COMMON MAN
- Breakdown Avoided Thanks To Condition Monitoring
- "Try & Buy" Offer For Thermal Imaging Camera
- New generation condition monitoring
- Diagnostics from a distance
- Power plant protection
- Real-time monitoring
- Cost-effective protection for smaller machinery