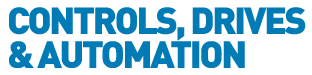
![]() |
Charlotte Stonestreet
Managing Editor |
Home> | CONTROLS | >Motion Controls | >Motion control: engineering partnerships |
Motion control: engineering partnerships
22 October 2021
Throughout the pandemic, OEMs have been challenged to provide solutions from design adaptions through to completely new machines. Many of these machines rely on high accuracy, meaning high demand on servo system design. Gerard Bush explains the need for a collaborative approach in motion control development
THE COVID-19 crisis has increased demand across a wide variety of medical sectors, not least imaging and diagnostics. As a result, CT (computerised tomography) scanners, used in the diagnosis of conditions impacting the lungs and circulatory system, among other organs and biological processes, have been heavily relied on. As a result, the motion system on which CT scanners are based, being integral to provide control accuracy, have also faced a strong requirement.
A CT scanner generates a 3D representation of the body by taking a wide series of X-ray images from a range of angles surrounding the patient. To optimise the patient outcome, the key attribute of a CT scanner includes high image resolution, where the more detail and clarity that the scanner presents, the higher the potential of analysis and diagnostics by the medical practitioner. This capability is the result of the speed and accuracy of the scanner's servo drive and motor control, and the servo package also has to combine control precision with speed of operation in order to minimise the time the patient is subject to the X-ray procedure.
Precision motion control
To achieve these benefits, a medical imaging OEM partnered with Kollmorgen for the supply of its servo drive, motor, cable and supplementary motion control equipment. The AKD servo drives form the basis of precision motion control and are selected by the CT scanner OEM as a result of their high bandwidth torque and velocity loops, combined with real time performance feedback.
The servo drives are matched with the AKM servo motor that offer low cogging to provide smooth and controlled motion, required for precision across multiple X-ray frames per second. High motor power density also ensures a more compact footprint for a smaller overall machine.
Ease and speed of motion application development and programming is also crucial for a faster time to market – especially crucial during the peak demand that the Covid crisis has presented. Combined, drive and motor compatibility ensures fast and reliable integration, which is made easier thanks to the simple to operate graphical user interface and wizard-based autotuning.
As part of Kollmorgen's global service, its capability is supported locally by country-based distributors and solution partners. In the UK, INMOCO supplies and supports Kollmorgen's products to OEMs, advising on a variety of aspects to facilitate effective machine design.
If specification criteria for application requirements, such as torque and speed, are as unknown by the OEMs design engineers, INMOCO can provide an OEM with servo sizing along with a detailed review of all potential application design aspects. This service extends through to a co-engineering capability, where INMOCO's engineers will interface directly with the OEM and Kollmorgen to develop the optimum motion package.
This could range from identifying aspects such as voltage requirements and the windings best able to suit application needs, through to calculating servo braking speeds. Machine design is also assisted with Kollmorgen's 3D image CAD library, which serves 50,000 product options for fast and simple motion solution integration within the overall machine.
Engineering partnership
If the partnership needs to extend further than the motion solution surrounding the motor, INMOCO can also work alongside Kollmorgen and the OEM to focus on software application development for the motion solution. This could range from programming motion profiles across the machine, through to the integration of third-party devices.
Gerard Bush is sales manager at INMOCO
Key Points
- Medical imaging OEM partners with Kollmorgen for supply of servo drive, motor, cable and supplementary control equipment
- The servo drives are matched with the AKM servo motor that offer low cogging to provide smooth and controlled motion
- INMOCO can provide an OEM with servo sizing along with a detailed review of all potential application design aspects
- Direct drive motors with zero cogging
- Compact washdown motor
- Force control for robot end effectors
- Optimising hygienic actuator design
- The fundamental principles of stepper motors
- High performance control for heavy duty servo applications
- Continuous control for long-life use
- Voice coil motors
- Motor selection for battery-powered industrial equipment
- Optimises machine design
- HARMONIC CANCELLATION
- Integrated Motion Control
- New 4th Generation PH Series Servo Planetary Gears are Largest in Class and offer Engineers even more benefits
- Driving Trends & Developments
- EtherCAT I/O is Tightly Integrated into Aerotech's A3200 Automation Machine Controller
- Galvo and Controller Combination Offers Infinite Field of View and 24-Bit Resolution
- Control systems
- Rail Coupling Minimises Downtime
- Custom Motion System For CT Scanner
- Full Servo Motion Advantages At A Fraction Of The Cost