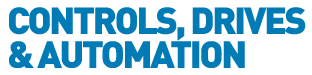
![]() |
Charlotte Stonestreet
Managing Editor |
Home> | MACHINE BUILDING & ENGINEERING | >3D Printing & Prototyping | >New answer to conformal cooling |
New answer to conformal cooling
08 October 2018
A recent step change in technology is set to revolutionise the manufacture of mould tools for plastic parts. Marcel Gowers explains this development and its benefits to businesses
One of the key challenges when manufacturing a mould tool is how to incorporate water channels that will allow even and effective cooling of the tool to improve the quality of the finished part while reducing and optimising cycle times.
To date, cooling channels are generally produced as drilled holes running in straight lines through mould tool core and cavity inserts. Bringing these straight runs close enough to the mould surface to provide optimal cooling is impossible when parts have curved or complex shapes, thin profiles or large numbers of intricate features. Additionally, drilled water holes have to compete for space with ejector holes; in box-shaped parts such as enclosures and housings, these both need to be located in the same place at each corner. In most cases, cross channels have to be drilled between two parallel channels and then sealed at each end, with ‘bubblers’ being used to make water run in and out of cores in a plane perpendicular to the drilled holes. However these techniques are only ever a compromise aimed at achieving the best cooling possible within the limitations of machining straight holes.
Conformal channels
What is needed for high-quality results is ‘conformal cooling’. In this approach, water channels closely follow the surface contours of the mould, bend to fit its shape precisely, and fit into all areas. To date, however, this has been too slow and costly to produce for most applications due to the limitation of the available technology. For example, to engineer conformal channels using conventional subtractive machining, engineers need to build mould tools in a series of layers. Each layer is machined separately, and they are then stacked together and brazed to form the finished tool. As well as being expensive, these tools can be less durable and are not suited to all part shapes.
The advent of additive manufacturing technology has opened up new possibilities. Using direct metal laser melting, powder materials can be formed into complex shapes enclosing channels of almost any shape and size. Unfortunately, the surface of tools made in this way is not smooth enough for subsequent moulding, so secondary machining is needed to make them usable.
Technological breakthrough
A new technology developed by OGM now combines additive manufacturing and CNC machining into an integrated build process which produces mould tools in a single operation. This technology is being offered as a new service from OGM; branded ConformL Cool, it promises to overcome many barriers and make conformal cooling a much more viable option.
This new technique is applied by OGM using the first manufacturing machine of its kind to be installed in the UK. Steel mould tool inserts are built layer by layer through laser sintering, with an automatic secondary machining process rapidly removing excess material after each set of layers has been completed. The conformal cooling channels are incorporated as part of the build process, which has an extremely high degree of dimensional accuracy, with a fine finish on both internal and external surfaces. There is generally no need for separate finishing work, which means the process is faster and more economical.
The precision and flexibility of this technology enables channels to be printed in whatever shape or route will best serve the moulded part’s cooling needs. Channel cross sections can be round, elliptical, rectangular or teardrop-shaped to maximise heat transfer in different situations. It is also possible to incorporate special features that encourage turbulent water flow, to keep channel surfaces smooth and free of trapped debris or fungal growth.
In addition to its inherent efficiency, and resulting cost-effectiveness, the new hybrid technology offers consistent levels of quality and, with OGM being located in the UK, means that lead times, compared to offshore manufacturing, can be significantly reduced from around 12 weeks from a far East supplier to just 4 weeks or less.
Marcel Gowers is additive applications engineering manager of injection moulding specialist, OGM.
Key Points