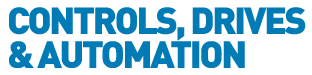
![]() |
Charlotte Stonestreet
Managing Editor |
Home> | POWER TRANSMISSION | >Actuators | >Technology for tomorrow's automation... today |
Technology for tomorrow's automation... today
25 June 2013
Driven by semiconductor industry requirements, linear motor manufacturers have steadily increased precision, reduced prices, developed multiple motor types, and simplified integration into automation equipment. Russell Cleasby from Dunkermotoren Linear Systems reports
Moore’s Law, famous for predicting long-term gains in semiconductor chip density, has long endured, thanks in large part to ongoing advances in linear motor performance and dependability. Today’s modern linear motors provide 50g+ peak acceleration and 10-meters/second velocity, deliver unmatched dynamic agility, minimize maintenance, and multiply uptime. In fact, with ten times the speed and ten times the operating life of ball screws and lower running costs than pneumatics, linear direct drive technology is often the most effective solution for machine automation.
Three linear motor types
Different manufacturing groups have specialized in one or another of three basic linear motor configurations: Flat bed, U-Channel, and Tubular motors. Each motor has its intrinsic benefits and limitations. Drawbacks specific to one motor type can often be sidestepped by using either of the two alternatives.
Flat bed motor
Flat bed motors while offering unlimited travel and highest drive force, exert considerable and undesirable magnetic attraction between the load carrying forcer and the motor’s permanent magnet track. This attraction force requires bearings that support the extra load.
U-channel motor
The U-Channel motor with its ironless core, has low inertia hence maximum agility. However, the Forcer’s load carrying magnetic coils travel deep within the U-Channel frame, restricting heat removal.
Tubular linear motor
Tubular linear motors are rugged, thermally efficient, the simplest to install and they provide drop in replacements for ball screw and pneumatic positioners.
The tubular motor’s permanent magnets are encased in a stainless steel tube (thrust rod), which is supported at both ends. Without additional support, load travel is limited to 2-3m depending on thrust rod diameter.
Brake permits vertical operation
Vertical operation is not a barrier in linear actuator applications as an electromechanical brake option will hold load position when drive power is removed. The brake also protects against damage in event of power failure and shutdown.
Dynamic stiffness & superior settling
Dynamic performance of conventional positioning mechanisms is limited by leads screws mechanical linkages, which produce hysteresis, backlash and wear. Similarly, pneumatic actuators suffer from piston mass and friction, as well as air compressibility, which produce servo control complexity. Linear motors and actuators shed the mass and inertia of the conventional positioners, so are freed from these fundamental limitations, providing unequalled dynamic stiffness. Motor and actuator are able to take full advantage of modern controller performance. The controller is tuned for high loop gain operation, achieving precise positioning, fast settling, and rapid recovery from transient disturbances.
Shorter cycle times, increasing productivity
Applications that demand rapid repetitive motion can exploit the linear actuator’s high bandwidth to achieve twice the throughput available with alternative solutions. Machines that maximize throughput by operating without stopping the material flow. These motors accelerate to synchronise with material flow, travel at material speed to initiate the process and after completion, returning at high speed to its starting point awaiting the next round-trip cycle. Throughput, in such applications, is directly related to the units forward/reverse excursion time.
Two-motors-in-one
Tubular linear motors lend themselves to productivity doubling applications with two or more independent Forcers operating on a single Thrust Rod. Each Forcer can travel fully independently of the other. One Forcer can then load, for example, while the other unloads. The technique can double throughput by lifting items two at a time from a fast travelling conveyor, separate and place them with precision on a second conveyor. Try this with a ball screw positioner!
Challenge servo pneumatics
Simple "bang-bang” pneumatic cylinders provide fast back-and-forth operation, but only for fixed travel distances. Modern short-run automation demands variable positioning and today’s linear motors and actuators are cost-competitive, quiet, and don’t need a supply of compressed air.
Introducing micro actuator and micro motor
Micro actuator and micro motor options that measure just 28mm wide bring automation to a new level of intricacy. Both provide travel and drive force far surpassing piezo electric or voice coil positioners and provide productivity-enhancing mechanisms in rehabilitation medicine, assembly, packaging, printing and many more uses.
Linear motors and actuators are now cost competitive with ball screws and belt drives and offer distinctly superior agility and bandwidth. They provide cost competitive drop-in ball screw replacements for throughput upgrades. Direct linear drives will increasingly replace servo-controlled pneumatic cylinders, contributing reliability and controllability, free from the cost, noise, and upkeep of air compressors.
Key Points
- Linear direct drive technology is often the most effective solution for machine automation
- Vertical operation is not a barrier in linear actuator applications
- Applications that demand rapid repetitive motion can exploit the linear actuator’s high bandwidth to achieve twice the throughput
- Dunkermotoren launches new IIoT brand
- Improved control for dynamic motors
- Hygienic linear motors
- Incorporates power supply & all functions
- Now with Profinet
- Ultra-compact brushless DC motor
- BG motors with field-oriented control
- Integrated controller
- Optimal solutions for linear movement
- Integrated controller option
- Extends Operating Life & Reduces Maintenance Costs
- Rigid Linear Drive Guides
- Tritex II™ AC Powered Actuators
- Exlar GSX Series
- Linear actuator gives bomb disposal robot extra lift
- Linear motion
- Improve Fluid Dispense Valve Speed and Accuracy With Nordson EFD’s BackPackTM Valve Actuator
- A question of application
- Heavy duty linear actuators
- Linear chain for a grand design