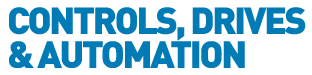
![]() |
Charlotte Stonestreet
Managing Editor |
Home> | DRIVES & MOTORS | >Variable Speed Drives | >Modular inverters for hydroelectric installation |
Editor's Pick
Modular inverters for hydroelectric installation
28 May 2014
Applied Hydropower has developed a dependable, efficient and cost effective solution to transfer surplus power to the national grid based on inverter drives from Parker Hannifin.

The biggest challenge with transferring energy from a small hydroelectric installation to the national grid is synchronisation: the power being fed to the grid must precisely match the phase and frequency of the grid itself. A second challenge is to have the turbine working at its peak efficiency all the time even though the supply of water flow and pressure varies considerably requiring the turbine speed to vary with it. A third challenge is to provide smooth shock-free starting for the turbine and alternator. Simply allowing the full force of the water to reach stationary turbine blades would impose large mechanical shock loads.
To address these issues when refurbishing the hydroelectric installation at Vivod Hall, a stately home in North Wales, engineers from Applied Hydropower decided to use Parker’s AC890 modular inverter drives. The drives are not, however, used in the usual way to control the speed of a motor. Instead, two bi-directional inverter modules are connected back-to-back via their DC buses. In essence, one of the inverters is connected to the hydroelectric installation’s generator, the other to the national grid. The generators used are induction generators.
With this arrangement, the speed of the induction generator may be varied, but the supply from the hydroelectric installation is always synchronised with the grid. The peak efficiency of the system may be set for different water conditions by measuring the induction generator slip between the frequency of the supply and the induction generator speed, by automatically raising and lowering the frequency by small increments the system can set its running frequency to find the most advantageous operating frequency.
This arrangement also has other benefits - as it is electrically bi-directional, it is possible to draw power from the grid to drive the induction generator as a motor. This means that it can be run up to speed at system start up, bringing the turbine up to speed prior to turning on the water, thereby eliminating mechanical shock problems.
- PUMPED UP PERFORMANCE
- SOFT STARTER OR VARIABLE SPEED DRIVE?
- Jeans With Less Energy
- Enhanced to Withstand Tough Environments
- Savings From Improved Torque Ratio & Efficiency
- Modular VSD
- ENERGY SAVING: AN OLD MESSAGE WITH NEW PROMISE
- Updated installation guide for power drive systems
- UK drives manufacturer seals global automation deal
- WEG motors & drives power high-efficiency air blowers