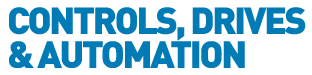
![]() |
Charlotte Stonestreet
Managing Editor |
Home> | DRIVES & MOTORS | >Variable Speed Drives | >Innovation drives inverter technology |
Innovation drives inverter technology
15 December 2015
Development work by leading manufacturers is centring on the customisation of both the mechanical and electronic elements of electric motors, as well as the advancement of high efficiency motors. Furthermore, the introduction of special inverters, frequency converters and other electronics that fit directly into the electric motor is ongoing, resulting in intelligent motor technologies
Despite the ongoing efforts of R&D technicians, two industry issues remain: the overall footprint of machines need to be reduced; as does the amount of electric cabling used to power it. In some instances, a high performance machine can be served by several kilometres of cabling, and the ability to eliminate electrical, magnetic and radio frequency interference makes for additional expense.
In short, costly remote control cabinets and long runs of cables are pushing suppliers towards localisation of machine parts. Here, the possibility of combining control components is a significant money-saving advantage as it reduces both the cable requirements and the manpower needed to assemble and wire control cabinets.
With the demand for greater motor efficiency and cost reduction, the onus is on the world’s leading motor manufacturers to introduce even more innovative products. Sure enough, European Commission Regulation C864012009 compels end users to specify high efficiency motors. However, by using frequency converters, it is now possible to boost the efficiency of the transmission system on the machine.
Consider a product such as Carpanelli's Microvert mini variable speed motors, which incorporate inverters up to 200W. Here, the inverter is completely hidden into the standard terminal box size of motor, which is considered to be a significant achievement.
Dedicated inverter
A further Carpanelli innovation, Minivert, houses a dedicated inverter up to 1.1kW inside a terminal block box to allow the use of asynchronous motors instead of single phase motors. It is particularly suited to applications where the presence of a single phase motor features high breakaway torque.
Drastic diffusion of EM (electromagnetic interference) is another quality of this product as it only has 3 cm of internal cable connecting the motor to the inverter. It is also said to be the most compact, integrated inverter solution available on the power transmission market. A special version has been developed to accept either 110 V input from a generator, or 240 V input from a mains supply. Sensing the input automatically, the device will operate anywhere in the range of 85 to 280V.
Among a myriad of intelligent applications is a specially designed inverter motor for the control of cow brushes. The brush is activated by the animal moving against the brush, and stops when the cow leaves the brush. Should the tail get caught in the brush, the inverter will sense the extra torque and switch into reverse mode automatically. Apparently, the cows love it and farmers are pleased as it results in greater milk yield.
Another farming application relates to a device known as the ‘helicopter’, a large fan situated in the roof of stables or cow sheds that is driven by a combined motor/inverter. The motor accelerates or slows down according to temperature, keeping the animals cool in summer and warm in winter. Another advantage is that the air flow generated by the fan blades has the effect of keeping the shed free of flies.
A further issue with standard inverters is that brake motors cannot normally be used, as a separate signal has to be sent from the inverter to the brake. This not only causes delay, but requires additional contacts, wiring and control cabinets. Carpanelli's solution to the problem is the MAI brake motor, in frame sizes 63-160, which is equipped with a special AC brake that operates directly from the inverter frequency through the motor terminals.
One final example of Carpanelli's inverter innovation is VacuumVert, a highly efficient motor with integrated electronic power board and intelligent firmware that has been developed specifically for vacuum pump applications. Typically, the motor power requirements are reduced by half.
Key Points
- Costly remote control cabinets and long runs of cables are pushing suppliers towards localisation of machine parts
- Using frequency converters, it is possible to boost the efficiency of the transmission system on the machine
- Carpanelli's Minivert houses a dedicated inverter up to 1.1 kW inside a terminal block box to allow the use of asynchronous motors instead of single phase motors
- PUMPED UP PERFORMANCE
- SOFT STARTER OR VARIABLE SPEED DRIVE?
- Jeans With Less Energy
- Enhanced to Withstand Tough Environments
- Savings From Improved Torque Ratio & Efficiency
- Modular VSD
- ENERGY SAVING: AN OLD MESSAGE WITH NEW PROMISE
- Updated installation guide for power drive systems
- UK drives manufacturer seals global automation deal
- WEG motors & drives power high-efficiency air blowers