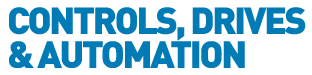
![]() |
Charlotte Stonestreet
Managing Editor |
Home> | IIot & Smart Technology | >Industry 4.0 | >The changing world of motion control |
Home> | CONTROLS | >Motion Controls | >The changing world of motion control |
The changing world of motion control
11 June 2018
John Inskip of Technique Services asks how motion control technology is changing to adapt to the fourth Industrial Revolution
The topic of data and lots of it is coming more to the forefront of Industry – how do we manage it and more importantly how do we get it from machines, process lines and robots to benefit respective businesses?
Being able to collect this data centrally on the machinery itself could be beneficial, as opposed to passing huge amounts of data via communication networks on the machine – using centralised controllers such as a PLC, handling processing and sending the data to central areas such as Cloud storage.
Monitoring the condition or environment of a process and of machinery has become a paramount priority to manufacturers, and the need to carry out predictive maintenance, as opposed to preventative maintenance, has led to advances in condition monitoring looking at the temperatures and vibration severity of motors and gearboxes, for example. Using a predictive maintenance approach to the requirements of machinery has enhanced machinery throughput, utilisation and reliability, ensuring that machinery asset utilisation is kept within high levels of usage. Not only is condition monitoring of interest, but also how energy is utilised by machinery and processes, ensuring that all assets have a reduced carbon footprint, and also use energy in the most efficient way.
When we take into account the accuracy that can now be achieved within motion control systems and the level of detail that can be monitored, there is no reason why high percentages of productivity cannot be achieved and arguably no unforeseen breakdown needs to occur any more in machinery. This message is true for any type of machinery, from conveyors through to complex robotic applications, but it is always important to have horizontal integration within the motion system, as well as vertical integration.
Usability and standardisation will become more desirable as technology moves forward. Being able to programme, commission, and diagnose – all from a central point – will provide the user with an enhanced experience that also allows them reduced commissioning time and the ability to diagnose trends, patterns and potential machine problems much faster.
User friendly
With usability in mind, motion control and drive technology in general is shifting to easy-to-use programming interfaces, those that are more accepted as mainstream as opposed to being perceived as a ‘black art’ by engineers.
User-friendly programming blocks that are intuitive and easy to use have de-mystified the subject of motion technology and at the same time ensured it adheres to the international IEC61131-3 standard.
Drive technology interfaces and software advancements have also benefitted the user, now using a framework of software that the automation hardware uses, allowing for seamless integration and configuration – a truly ‘joined-up’ approach. The demand for more compact drive technology has led to designs with a smaller footprint, that are more robust and resistant to changes in temperature. Drives are now designed to have coated printed circuit boards and wide operating temperature ranges, ensuring long service life and stability.
Better configurations
To support new products and solutions within motion control, vendors like Siemens are developing and releasing iPad/smart phone apps to assist and configure drive and motion technology; this benefits the user considerably by introducing a parallel method for the next generation of engineers who use smart phone technology on a daily basis.
Encapsulating motion control into the automation framework will not only reduce the hardware requirement, but also the supporting software, by using programmes like TIA Portal. It provides a suite of solutions within the one software environment, thus ensuring a common look and feel to all programme requirements, and making the need to be familiar with multiple software solutions obsolete.
Industry 4.0 and the technology evolutions that are happening provide the manufacturing industry with an opportunity to revolutionise machinery and processes, to meet the demands of mass production well into the next few decades of the 21st century.
Technique Services is an Approved Siemens Technical Partner
Key Points
- Business Secretary praises Siemens commitment to skills & apprenticeships
- Siemens tackles skills gap
- Education, investment & innovation
- Siemens speeds digital future of industry with Xcelerator
- Defend in depth
- Siemens launches control & automation degree
- PACKAGE DRIVES WIND TURBINES
- Complex configuration standardised
- Siemens & DAI launch technology hub
- Siemens appoints Juergen Maier as new UK chief executive
- HARMONIC CANCELLATION
- Integrated Motion Control
- New 4th Generation PH Series Servo Planetary Gears are Largest in Class and offer Engineers even more benefits
- Driving Trends & Developments
- EtherCAT I/O is Tightly Integrated into Aerotech's A3200 Automation Machine Controller
- Galvo and Controller Combination Offers Infinite Field of View and 24-Bit Resolution
- Control systems
- Rail Coupling Minimises Downtime
- Custom Motion System For CT Scanner
- Full Servo Motion Advantages At A Fraction Of The Cost