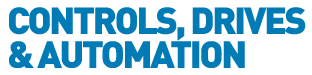
![]() |
Charlotte Stonestreet
Managing Editor |
Home> | MACHINE BUILDING & ENGINEERING | >3D Printing & Prototyping | >Adding additive value |
Adding additive value
24 June 2022
Moving beyond rapid prototyping, within the last decade additive manufacturing has developed into a production solution for final parts. Laura Kastenmayer reports

DEVELOPMENTS IN additive manufacturing have been driven by early adopters and printing enthusiasts, but also by machine manufacturers like TRUMPF; the German laser expert and machine manufacturer entered the additive manufacturing field back in 1999. Since 2014, the company has offered metal 3D printers based on laser powder bed fusion (LPBF) technology with its TruPrint machines. Being familiar with the medical market through its laser marking, laser cutting and laser welding solutions, the company has not only launched machines that meet the needs of medical device manufacturers, but also offers advanced services to help customers with their qualification and validation process.
Additive manufacturing is best known for its design freedom, which has made the technology ideal for the production of patient-specific devices. But this is not the limit of its potential. A large number of off-the-shelf devices have proven to be a sufficient and reliable solution for patients all over the world and do not necessarily need to be replaced by a customized solution. Nevertheless, or precisely because of this, the question arises as to how 3D printing can add value to the production of these standard medical devices.
The design flexibility afforded by additive manufacturing technology, makes it possible to significantly shorten the entire process chain by already integrating the surface modification or component functionality into the printing process step.
An exemplary case for the mass production of parts with integrated surface design is acetabular cups. These are flagship products for metal additive manufacturing in medical technology and have been printed with different surface structure characteristics since 2007.
Engineering improvements
Meeting the mass production market requires an approach that significantly reduces cost per part and time to market, while maintaining a high level of quality. There are several critical process parameters that impact a reliable and efficient production process, and many of these can be addressed through engineering improvements to the machine.
Over the years, TRUMPF has invested heavily in advanced and robust machine designs, focusing on well thought-out gas flow concepts, parameter settings and stable process conditions. The company also equips its machines with state-of-the-art monitoring solutions that help additive manufacturing operators better understand their process and monitor the quality of their parts. One of the technical machine developments is the 500°C preheating option on the TruPrint 5000 machine. This feature raised the limits of production capacity in metal powder bed melting to a new level without the need to add further laser sources. Using the acetabular cups as an example, the effects of 500°C could be optimally exploited by significantly reducing the number of support structures and stacking the components in multiple layers.
It is self-explanatory that this process saves material costs and reduces part costs in series production when the system is utilized to the maximum. The use of 500°C preheating for titanium and advanced parameter setting also ensure that quality is not compromised at maximum production capacity.
But it is not only the widely used material titanium for orthopedic implants that benefits from the advances TRUMPF has made in printing technology in recent years. With the 500°C preheating of the build plate, it is also possible to process high-carbon materials such as hot work tool steels 1.2343 (H11) and 1.2344 (H13). One might think that this is of no interest to the medical technology industry, but it is quite the opposite. Hot work steels, as well as stainless steels such as 1.2709, are often used for mould inserts in plastic injection moulding. Considering the huge amount of disposable plastic products, plastic injection moulding plays an important role in the medical industry. Combined with additive manufacturing, mould inserts can be designed with near-contour cooling to improve cooling rates and plastic quality in ways that would not be possible with conventionally manufactured inserts.
Complementary technologies
Nevertheless, it is rarely the case that additive manufacturing can do without one of the conventional processes. For users, machine suppliers and the manufacturing industry, it is crucial to bring the additive and conventional worlds together in the best possible way. Each technology should be used where it brings the greatest benefit. TRUMPF already offers technical solutions in the dental market that take this approach into account and allow individual geometries to be printed on a conventionally manufactured part. This approach is called printing on preform and medical applications such as shoulder or dental implants and surgical instruments can also benefit from this solution in an economical way.
From major OEMs in the medical industry to new, emerging contract manufacturing companies, all have recognised the potential of metal 3D printing for medical device products. The challenge is to use the technology in a profitable way. The initial time spent evaluating the potential of additive manufacturing, as well as the right machine solution and the right machine supplier to support along the way, are key to success.
“We worked for two years with IMR [Irish Manufacturing Research], a technology and research organization, to experience 3D printing and get a feel for what it could do in terms of its capabilities, limitations, advantages and disadvantages,” says Gerard King, director of Smithstown Light Engineering, an Ireland-based company that recently invested in two TruPrint 2000 machines from TRUMPF to manufacture and supply high-quality parts to the medical industry.
It is worth investing time and money in the introduction of additive manufacturing first. The benefits of the technology are obvious, even if only a fraction of the potential of additive manufacturing has been exploited so far. Currently, the focus of metal additive manufacturing is on orthopedic devices and implants, which are primarily made of titanium or CoCr. But the technology offers so much more. Even exotic materials such as copper, tungsten, tantalum, nitinol, precious metals and amorphous metals have already been successfully processed on TRUMPF printers, opening up future improvements in areas such as cardiology, electrosurgery or imaging and diagnostics. Those who neglect the emerging technology of additive manufacturing could thus lose touch with the market and the competition in the medium to long term.
Laura Kastenmayer is industry manager medical technology at TRUMPF Additive Manufacturing
- Reduce production costs with innovative solutions
- Simple solution for automated material transport
- Ground-breaking press brake
- 3D printing system supports medical device industry
- Compact laser workstation
- Laser processing, punching & forming
- Automated arc welding
- Sheet metal know-how
- 3D printer for medical devices
- Output & reliability boosted