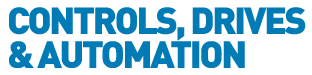
![]() |
Charlotte Stonestreet
Managing Editor |
Home> | AUTOMATION | >Condition Monitoring | >Optimising uptime |
Home> | DRIVES & MOTORS | >Variable Speed Drives | >Optimising uptime |
Editor's Pick
Optimising uptime
11 July 2022
Jonathan Smith looks at how enhanced diagnostic capabilities can be used to augment condition monitoring of low voltage drives

FOR MOST manufacturers, downtime is the single largest source of lost production time, and the cost of unplanned downtime is high. Depending on the industry and application affected, an hour of unplanned downtime can be many times more expensive than the cost to replace the equipment related to the issue.
Digital control is now a norm with most production and manufacturing drives connected and controlled through a network, typically ethernet based, and whilst this provides certainty in control commands and instructions, very often the only condition-based information available is a simple fault code which just advises that there is already a problem. Where the drives employed are mission critical this is simply not sufficient to ensure optimum plant uptime is maintained.
A choice of maintenance paths
There are several choices for managers when dealing with the lifespans of drives. The traditional route is to simply react to component failures when they occur or replace components on a fixed schedule that does not account for use and environment. The first approach can be costly, unpredictable and cause unplanned downtime. The second approach is better, but not optimal and can lead to overspending on maintenance and replacement components.
The latest digital drives such as the PowerFlex 755T range from Rockwell Automation are now leveraging the increased computing power they possess to provide a level of predictive maintenance previously unavailable. As such it is now possible to use advanced predictive maintenance functions to replace components as needed before they expire. This reduces unplanned downtime, optimises spending on maintenance and replacement components and makes the workloads of the maintenance professionals more effective and predictable.
Predictive maintenance models are built around a common framework where the life consumed by each component is tracked by the drive. Advanced physics-of-failure models are incorporated into the drive to convert actual stressors such as voltage, current, speed, switching frequency, and temperature into life consumption for critical components like fans, power semiconductors, capacitors, and breakers. When the consumed life exceeds the user-defined event level (default is 80%), an alarm is generated indicating that preventative maintenance is required for the specific component.
The rate of life consumption is also tracked in the firmware for each component on a virtual rolling average. This rate is unique to each drive and depends on how it is used. Based on the rolling rate of life consumption, the new predictive models will calculate how many hours remain until the percentage of consumed life reaches the alarm level. This remaining life calculation allows for proactive scheduling of preventative maintenance and minimum downtime.
The intent of the event level, or maximum life consumed before an alarm is generated, is to allow the end-user to control the risk of unplanned downtime. Finally, as the new predictive maintenance algorithms adapt to how the drive is being used, it will take about 30 days for the models to learn about the application stresses.
CMMS Systems
Utilising such data from intelligent devices within Cloud based computerised maintenance management systems (CMMS), such as such Fiix by Rockwell Automation, make it possible to have a structured record of plant conditions and develop optimised maintenance programmes to further maximise uptime and availability. The result is comprehensive and dynamic condition-based data based on both historical performance and actual device condition. By optimising maintenance programmes, not only uptime and availability are improved, but the lifespan of monitored assets are also enhanced so enabling maximum return on investment.
Jonathan Smith is business manager - intelligent devices, UK & Ireland at Rockwell Automation
www.rockwellautomation.com/en-gb.html
Key Points
- Traditional maintenance models react to component failures or replace components on a fixed schedule
- The latest digital drives leverage increased computing power to provide new level of predictive maintenance
- Data from intelligent devices make it possible to have a structured record of plant conditions and optimised maintenance
- Training for the next-generation workforce
- MIDRANGE CONTROL
- A modular approach in manufacturing
- Next generation edge gateway to accelerate IT/OT convergence
- Rockwell Automation to acquire Clearpath Robotics
- New thought leadership video series from Rockwell
- Energy savings as a service
- Rockwell to acquire ASEM
- Strategic investment gives early access to innovative technology
- GE Healthcare & Rockwell Automation collaborate
- PUMPED UP PERFORMANCE
- SOFT STARTER OR VARIABLE SPEED DRIVE?
- Jeans With Less Energy
- Enhanced to Withstand Tough Environments
- Savings From Improved Torque Ratio & Efficiency
- Modular VSD
- ENERGY SAVING: AN OLD MESSAGE WITH NEW PROMISE
- IO-LInk Now Included
- As Long As The Wind Blows
- CONDITION MONITORING FOR THE COMMON MAN