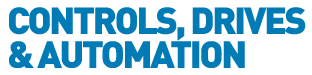
![]() |
Charlotte Stonestreet
Managing Editor |
Home> | IIot & Smart Technology | >Industry 4.0 | >The smart manufacturing transformation |
The smart manufacturing transformation
12 July 2021
To realise the full potential of smart factories, manufacturers are looking to integrate interconnected production systems, machines, robots, and other smart factory technologies into the SAP ERP operations. Heiko Mannherz looks at the challenges
TO REMAIN competitive, manufacturers are increasingly adopting modern technologies in their production facilities. These include SAP Manufacturing Execution, SAP HANA, and other devices and systems connected via the Internet of Things (IoT). Although Industry 4.0 technologies and processes offer manufacturers huge benefits, they also intensify IT infrastructure complexities and create new requirements for SAP operation and monitoring to avoid downtime and maximise productivity. Indeed, SAP is one of the most mission-critical applications for a manufacturer and any downtime brings activities at halt, potentially costing millions in lost revenue. Fortunately, automation is around to fill the gap and ensure that new-age manufacturers are meeting their business objectives.
Robust monitoring of the SAP environment is essential, and any weaknesses in this area are the most likely reasons for system outages. To support the new Industry 4.0 approach to manufacturing, businesses need to optimise the systems to get the best out of IoT and ERP operations. The automation of IT service management processes led by artificial intelligence delivers next-gen capabilities. Termed 'AIOps', this new way of automating, monitoring, and managing modern IT landscapes is an essential part of the journey towards reaping the full benefits of implementing Industry 4.0 or ‘smart’ manufacturing processes.
The dawn of the IoT and Industry 4.0 also means that SAP applications are increasingly being from on-premise to hybrid or cloud-based solutions. Any monitoring solution needs to be scalable, flexible, and able to handle future changes to the SAP landscape.
Complex IT landscapes
SEW-EURODRIVE is one of the leading manufacturers of drive and automation technology in the world. It offers a wide range of drive solutions with customised control technology and individual services. For example, conveyor belts, beverage filling systems, roofs of sports stadiums, gravel plants, assembly lines, or escalators. Depending on their requirements, customers can purchase pre-configured package solutions or individual components from an extensive modular system.
To deliver its extensive portfolio of solutions, SEW-EURODRIVE has 17 manufacturing plants, 109 SAP (26 SAP HANA and 83 Oracle) systems running on over 350 servers spread across different locations.
Additionally, it has various stand-alone databases used for development and production, which are linked to SAP applications such as ERP, CRM, HR, or MES (Manufacturing Execution System) for production control. Until 2015, SEW-EURODRIVE used an Application Manager, but this did not support new SAP solutions such as SAP HANA or the new NetWeaver systems and a new monitoring solution was necessary. A complex interface meant a high level of in-depth knowledge was required to monitor its SAP landscape. Along with the manual hours required to carry out relatively simple and mundane tasks, its IT service management processes were inefficient and left the business open to the risk of sales-critical process downtimes in its factories.I
Increased efficiency
AIOps-based technology, such as the SAP Operations Automation Platform from Avantra, offers manufacturers new-age observability across SAP environments. SEW-EURODRIVE employed such a solution to monitor its global ERP operations located globally, including in China and Australia. The deployment of such a system has simplified and automated IT service management processes, freeing high-skilled resources to work on other value-add activities.
Alongside ERP operations, SEW-EURODRIVE also uses the new system to monitor its modern and complex HANA-based manufacturing processes across its smart factories. By using open interfaces within the automated monitoring system, it was further able to integrate and monitor its enterprise automation solution.
The resulting system reduces the manual effort required to monitor business-critical systems and increases the control of maintenance processes.
Real-time monitoring means anomalies are identified straight away, and a simple user interface means that personnel without in-depth IT knowledge are readily alerted with clear differentiation between automation and IT components, enabling errors to be quickly rectified. Resulting in terms of fewer man-hours taken with manual monitoring tasks, less time to identify where problems lie, and reduced downtime of production systems, enhancing overall productivity and profitability.
Gregor Wachter, IT system administrator at SEW-EURODRIVE, said: “Integration and monitoring of interconnected production systems, machines, and robots from our smart factory into the existing SAP ERP operation is essential. In addition, we must provide sales-critical SAP processes such as customer and order management stably and efficiently and minimise any risk of failure.”
Daniel Müller, head of IT Operations at SEW-EURODRIVE, added: “Our colleagues working on SAP can now quickly develop individual monitoring scenarios themselves. There are also code modules for this. It is also possible for us to implement ABAP code and execute it in the new software.”
Beyond SAP monitoring
The AIOps monitoring system installed by SEW-EURODRIVE is also used to proactively monitor sales-critical assembly processes. Every assembly station on the shop floor has a touchpad that monitors the individual assembly steps and supports the work of the fitters with three-dimensional construction plans and clear video instructions. Only when a work step has been completed and this has been confirmed by the fitter can the next process step begin.
In addition, sensor data from machines, such as power, temperature, or revolutions, is integrated into the AIOps monitoring system. By analysing this data, the system can indicate which components are nearing the end of life and require replacement, effecting a predictive maintenance solution that further helps with the scheduling of maintenance activities to reduce downtime and avoid costly machine breakdowns. SEW-EURODRIVE hopes to extend this predictive maintenance capability to its customers in the future as a data-based cloud service as part of its service level agreement packages. Such capability presents an opportunity for both increased market differential and an additional revenue stream.
Alongside predefined standard checks based on manufacturing experience, the new monitoring system also provided custom checks, easy adaptation and configuration options which provided SEW-EURODRIVE with a flexible solution to meet their unique current needs and confidence that the system could adapt to future manufacturing system requirements.
The new monitoring system also means that IT staff are only notified of critical system alarms and, despite three-shift operation in the factories, there is no need for resource-intensive IT shifts to ensure round-the-clock support. The company now operates with a simple on-call IT service and is saving both time and money in systems support.
Gregor Wachter concluded: “The new AIOps software has increased the efficiency of our IT service management processes and helps prevent downtime of sales-critical processes. The software is easily scalable and is therefore equipped for monitoring a growing number of new systems and applications.”
As IT landscapes become increasingly sophisticated, companies are finding that their high-skilled IT resources are spending much of their time maintaining systems and carrying out mundane, repetitive tasks. Additionally, although Industry 4.0 or smart factories offer huge benefits in terms of increased efficiency, quality and business agility, the intricacies of the automation involved make the monitoring of SAP and other automation systems even more critical to business strategy.
Using AI, automated monitoring systems offer businesses such as SEW-EURODRIVE a way to increase the efficiency of SAP monitoring. Additionally, it frees valuable IT resources to concentrate on innovation and customer experiences. The whole essence of Industry 4.0 is to increase efficiency, productivity, and quality to customers. It makes sense, therefore, to also use the advanced AI technology available today to deliver the automated service needed at an IT level to keep pace with the changes on the shop floor. Ultimately, a properly constructed AIOps solution will deliver an excellent return on investment and make businesses more resilient for the future.
Heiko Mannherz is chief innovation officer, Avantra
- AVEVA expands collaboration with Microsoft with focus on Cloud & AI
- AMR revolution in cold chain logistics
- Sellafield and AtkinsRéalis operate Spot robotic dog
- Free app helps assess & control workforce infection risk
- What Wi-Fi 7 means for manufacturing
- VW's roaming charge
- Still work to be done on the Industry 4.0 journey
- Research hub to lead use of digital twins
- Geek+ & Nike introduce same-day delivery in Japan
- Evolving network standards for IIoT
- Industry 4.0 ready
- Intelligent interlocks
- The digital future has begun
- The smart future of manufacturing
- Partnership integrates freight & warehouse management
- When & where will Industry 4.0 actually happen?
- Education key to unlocking I4.0
- How well is your smart farm running?
- Digitalisation, automation & electrification
- Industry 4.0 guidance platform