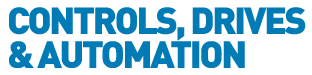
![]() |
Charlotte Stonestreet
Managing Editor |
Home> | IIot & Smart Technology | >Connectivity | >Ready for take off to Industry 4.0 |
Home> | IIot & Smart Technology | >Industry 4.0 | >Ready for take off to Industry 4.0 |
Editor's Pick
Ready for take off to Industry 4.0
30 January 2018
Tool coding using RFID has been in successful use long before Industry 4.0. Premium Aerotec, one of the world's leading Tier 1 suppliers for aircraft structures, has been using this key technology for decades for quality and process assurance.

Used today over the entire range of metal-cutting production, the Tool-ID system from Balluff does however, represent the prerequisite for intelligent networking, with the potential for further optimising tool utilization and ultimately for continually improving processes and product quality.
The machining of aircraft structure components is considered to be one of the most premium classes in the industry. One reason for this is due to them using modern and often difficult to machine materials. In addition to sophisticated aluminum alloys, materials such as titanium or carbon fibre reinforced composites (CFRP) place high demands on the machining process. Furthermore, these are preferably thin-wall components due to weight reduction being the top priority in aerospace, whilst still achieving the optimum strength and stiffness of the components.
"Structural components made of light alloys often have complex free form surfaces and the most difficult undercuts. So-called HPC, or High Performance Cutting, is highly demanding in terms of precision and process reliability," explains Daniel Weishaupt, head of tool reconditioning and commissioning at Premium Aerotec in Augsburg, Germany. "The basic prerequisite however, is that the tool parameters are loaded precisely and error-free into the machining centre," adds Weishaupt, touching on the main motivation for using a tool identification system.
The general advantage of systems such as Tool-ID from Balluff, is the transmission of tool-relevant data between a data carrier fixed to the tool and a read/write unit using a high-frequency electromagnetic alternating field. So-called Radio Frequency Identification (RFID) ensures certain association of the tool. Using RFID read/write heads on the tool presetter, information can be written to the data carrier on the tool and read out in the machine tool. In addition, relevant data such as cutting time can be written back to the data carrier after the tool has been used. Automatic processing of the data ensures that all the information is correct and current. For this reason Premium Aerotec has equipped the tool presetters and measuring devices from Zoller, as well as around 30 machining centres with Tool-ID read/write heads and processor units from Balluff.
"We were able to integrate the system into all the controllers on our various machines with no difficulty," notes Weishaupt. Integration was carried out amongst the companies by Erhardt + Leimer Automatisierungstechnik GmbH from Augsburg. This company specialises in system solutions and automation technology in ongoing production and required just 12 weeks for completion. The BIS M read/write heads are available in a variety of form factors and dimensions - such as round or bar antenna - so that all the various requirements in the different machining centres at Premium Aerotec could be met.
No small parts were played by the BIS V processor units in the rapid integration of Tool-ID into the ongoing production at Premium Aerotec. The BIS V can communicate at various frequencies. In other words, these controllers can operate using low-frequency system components (LF, 70...455 kHz), which are especially rugged and reliable in metal surroundings and high-frequency components (HF, 13.56 MHz) at the same time.
At Premium Aerotec however, it was the variety of available interfaces these processor units offer that was the deciding factor for integrating into the various machines. All the common bus systems used in industry around the world such as Profibus, Profinet, EtherCAT, CC-Link and Ethernet/IP variations are available. There is also a web server for Ethernet-based interfaces. Function blocks for many common controller OEMs also make setup fast.
The existing tools and tool holders were fitted on their sides with so-called tags. Premium Aerotec choose type BIS M data carriers, which operate at a frequency of 13.56 MHz and are rated for an unlimited number of read/write cycles. "We decided on the BIS M version because these tags meet the RFID standards ISO 15693 and ISO 14443A and are available from different manufacturers,“ adds Weishaupt, who sees this as a security factor for his production. Around 30,000 tools are currently managed using this system.
Also important according to Weishaupt is the high transmission speed even at high data quantities which can be achieved with the BIS M RFID system. "This contributes to the fact that today the read process is faster by 30 percent," notes Weishaupt.
The first requirement for RFID tool identification, namely automating and securing the handling of tool-specific data, has been met for years. Accurately conveyed tool dimensions and usage parameters, as well as, recorded service and life and remaining life times ensure reliable processes. Recording cutting time of tools is hugely important," explains Weishaupt: Wear results in increasing cutting forces and causes geometric deviations in the workpiece. Especially critical is the resulting so-called surface spalling as a consequence of thermal and mechanical cyclic loading, which can lead to unrepairable damage to the component."
Surface spalling in cutting tools occurs after longer periods of use, during which however, no wear is actually measurable. It becomes evident in the form of cracks which propagate. Structural changes and fatigue can result in disassociation of particles which in turn can damage the component. Tool wear from abrasion for example, leads to increased cutting forces. The tool edge can no longer withstand the higher cutting forces and consequently results in tool breakage, which itself can also damage the workpiece.
The cost of aerospace components, often in the thousands or tens of thousands of dollars, makes the problem clear. For this reason the data carrier on each tool holder transmits a maximum tool life datum to the tag on the tool itself, which is based on experiential values.
Beyond the determination of tool use times, the BIS M data carriers with their unique ID number make it possible to create what Weishaupt calls a lifetime document for the tools. The unique ID on this data carrier is read-only and cannot be changed. It makes it possible to ensure traceability for the parts in the sense of quality assurance and to document the history of each tool. Central storage and processing of the tool data in a tool management system will open up countless new approaches to further optimising tool use. Tool-ID from Balluff is therefore, a key component of the intelligently networked production at Premium Aerotec who are now ready for takeoff for Industry 4.0.
- Sensor mounting system
- I/O blocks for quicker network building
- Signal lamp with IO-Link
- Simulated production line
- University students get a taste of engineering
- Read 1D & 2D Codes
- Seamless Data Recording
- Balluff introduces hundreds of new products to its portfolio
- Impact, Chemical & Abrasion Resistant
- Highly accurate angle detection
- Industry 4.0 ready
- Intelligent interlocks
- The digital future has begun
- Transmission of Data to Cloud
- The smart future of manufacturing
- Partnership integrates freight & warehouse management
- Makes IoT available in practice
- When & where will Industry 4.0 actually happen?
- Education key to unlocking I4.0
- Complete solution for IO-Link