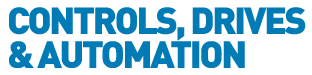
![]() |
Charlotte Stonestreet
Managing Editor |
Home> | MACHINE BUILDING & ENGINEERING | >3D Printing & Prototyping | >Self-built HT-3D printer |
Editor's Pick
ARTICLE
Self-built HT-3D printer
22 May 2019
An example of igus’ low-cost automation concept, the newly designed and constructed high-temperature 3D printer was built using drylin W linear guides, dryspin lead screws made of stainless steel and igus standard stepper motors, to facilitate the development of iglidur J350 high-temperature filaments.

“High temperatures not only create problems for many machine elements in plants but also conventional 3D printers,” explains Dean Aylott, dry-tech specialist product manager, igus. “To develop new filaments for wear-resistant parts in high-temperature applications, we built our own high-temperature 3D printer.”
For the mechanical system, igus engineers used the heat-resistant stainless steel components of the maintenance-free drylin W linear guide and smooth-running dryspin high-helix leadscrews in the X-, Y- and Z-axes. Lubrication-free liners and leadscrew nuts made from the wear-resistant high-performance iglidur X and iglidur C500 plastics, ensure precise adjustment of the building board, even at temperatures of up to 200ºC.
“We use a nozzle that can melt the filament at a temperature of up to 400ºC,” explains Aylott. “This enabled us to develop and extensively test a new filament for high-temperature environments with iglidur J350.” The lubrication-free iglidur J350 material is already offered as plain bearings and bar stock. Characterised, above all, by its extremely high wear resistance and its low coefficients of friction on steel, the engineering plastic has high dimensional stability at temperatures up to 180ºC.
Using the HT-3D printer, the filament can be processed well on a printing plate equipped with a PET film. Typical application areas of the new iglidur J350 filament include vending machine technology, automotive, glass processing and general mechanical engineering. In addition to iglidur J350, six more filaments are available from igus: from materials approved for food contact up to chemical-grade plastics.
For the mechanical system, igus engineers used the heat-resistant stainless steel components of the maintenance-free drylin W linear guide and smooth-running dryspin high-helix leadscrews in the X-, Y- and Z-axes. Lubrication-free liners and leadscrew nuts made from the wear-resistant high-performance iglidur X and iglidur C500 plastics, ensure precise adjustment of the building board, even at temperatures of up to 200ºC.
“We use a nozzle that can melt the filament at a temperature of up to 400ºC,” explains Aylott. “This enabled us to develop and extensively test a new filament for high-temperature environments with iglidur J350.” The lubrication-free iglidur J350 material is already offered as plain bearings and bar stock. Characterised, above all, by its extremely high wear resistance and its low coefficients of friction on steel, the engineering plastic has high dimensional stability at temperatures up to 180ºC.
Using the HT-3D printer, the filament can be processed well on a printing plate equipped with a PET film. Typical application areas of the new iglidur J350 filament include vending machine technology, automotive, glass processing and general mechanical engineering. In addition to iglidur J350, six more filaments are available from igus: from materials approved for food contact up to chemical-grade plastics.
MORE FROM THIS COMPANY
- Module enables predictive maintenance
- igus invests in automation
- Small rotary module for robots
- Custom parts produced rapidly & economically
- igus adds to low cost automation portfolio
- Easy installation
- Cost-effective entry into automated logistics
- First tribo-filament for 3D printers
- Hybrid cables for adverse conditions
- igus introduces new speedifit service
OTHER ARTICLES IN THIS SECTION