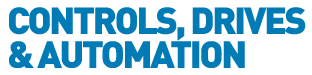
![]() |
Charlotte Stonestreet
Managing Editor |
Home> | AUTOMATION | >Condition Monitoring | >Making maintenance smart |
Home> | IIot & Smart Technology | >Industry 4.0 | >Making maintenance smart |
Making maintenance smart
11 July 2022
To minimise downtime effectively, maintenance technologies should be the most important aspect of Industry 4.0, says Marek Lukaszczyk

EQUIPMENT DOWNTIME can wreak havoc in industry. In fact, research by Oneserve found that downtime costs UK manufacturers £180 billion per year. The same report stated that 53% of all machinery downtime is caused by hidden internal faults, which would typically be investigated by a maintenance engineer. Interestingly, three quarters of business leaders in the survey also said they outsourced their machine maintenance. This suggests their businesses run on a planned maintenance methodology, where assets are replaced and maintained according to a predetermined schedule. A problem with this method is that engineers are unable to spot faults that could worsen in-between maintenance checks.
Excess vibration or heat are among the most common causes of equipment deterioration. Similarly, common causes of motor failures include worn-out bearings, shaft misalignment and winding insulation problems.
Traditionally, these problems would go unnoticed unless an expert was on-hand to investigate the asset, observe any symptoms of failure and take preventative maintenance steps. Now, digital technologies are being deployed to support, and sometimes automate, these processes.
Maintenance 4.0 is the phrase used to describe the digitalisation of maintenance technologies that collect, monitor, and analyse data generated by industrial assets. To fit the criteria of Maintenance 4.0, these technologies must diagnose problems faster than a human engineer following a planned or preventative maintenance schedule.
Maintenance technologies are not designed to replace engineers, but to ensure these teams work in the most efficient, and effective, way possible.
Fleet management technology
WEG’s Motion Fleet Management (MFM) sits within this category, as part of a growing portfolio of digital solutions from WEG. The solution uses cloud computing and Internet of Things (IoT) technologies to monitor the operational status of several industrial assets. Through data collection and processing, MFM generates valuable real-time insights to share with plant managers and engineers, which ultimately leads to improved asset management.
The tool can collect data from a range of different assets including motors, drives, pumps, fans and compressors. The information is fed back to a centralised dashboard where it is processed, analysed and visualised to provide engineers with real-time insights into asset performance.
In practice, this can mean that hundreds of industrial assets are visible at once, which allows engineers to identify any problems or irregularities. Let’s say a motor is beginning to deteriorate because of damage to a bearing. MFM is able to monitor data directly from the motor through a WEG Motor Scan, a special sensor developed by WEG that screws to onto the motor fin, and alerts an operator as soon as the bearing shows signs of decline.
This is an example of just one motor problem, but plants will typically operate with multiple motors that run continuously for production, meaning the problem-finding potential is much larger.
Managing large-scale asset fleets
Consider an environment with a huge number of industrial assets such as an oil refinery, a food processing facility or an energy distribution network. The sheer volume of motors, drives, gearboxes and other assets makes maintenance a hugely complex operation to oversee. Unfortunately, it also makes unplanned downtime inevitable.
Unplanned downtime has a particularly high cost in offshore oil and gas applications. A report by Kimberlite states that the industry experiences, on average, around £38 million of financial losses per year due to downtime. More shockingly, fewer than 24% of operators in offshore oil and gas describe their maintenance approach as one based on data and analytics. Instead, most opt for reactive maintenance.
Reactive maintenance differs to planned maintenance, mentioned earlier, and describes when a facility only repairs or replaces an asset when it has broken down completely. While this method can reduce the unnecessary part replacements sometimes associated with planned maintenance — for instance, overhauling a drive simply because the schedule suggests it — there are obvious disadvantages.
The biggest challenge of reactive maintenance is budget control. Emergency repairs cost far more than planned ones and, more often than not, failures occur when a system is working flat-out. This creates additional expenses due to unplanned downtime.
The offshore oil and gas sector is a prime example of a sector that needs Maintenance 4.0 technologies. Not only is the cost of downtime colossal, but the sheer scale of these facilities can make manual maintenance checks a logistical nightmare.
WEG’s MFM removes the need for oil and gas engineers to make regular visits to remote offshore assets. The system enables the visualisation of all equipment in a single environment, with reports and indicators of the performance of every single asset. Usefully, the system also provides customised layouts. These can give overviews of different levels, such as a view of the entire oil and gas infrastructure, the equipment within a drilling control room, or the assets related to one small application.
This is particularly helpful for large-scale infrastructures that have various stakeholders with different areas of interest — for instance, maintenance engineers, asset managers and production managers.
Smart maintenance
One of the key features of MFM for maintenance engineers is the customisation of asset tolerances. By inputting the ideal state of an asset, an engineer can set up alerts for when the asset moves outside of pre-set criteria. Alerts can identify when a piece of equipment is showing signs of excess heat, vibration or misalignment, and the engineer can investigate accordingly. E-mail alerts on critical assets can also be activated, and sent to maintenance teams on a daily basis.
MFM’s data processing is managed both on edge and in the cloud. This allows for fast reactions at the device level, while also enabling comprehensive data analysis in the cloud. The tool also boasts specialist modules with artificial intelligence (AI), allowing for automated fault diagnosis based on historic reports and trends.
Making maintenance smarter is a priority for WEG, and a goal of its new portfolio of digital tools. It’s no secret that unplanned equipment downtime has a significant financial impact on UK businesses. To minimise these losses, facilities managers must invest in Maintenance 4.0 technologies, like MFM, to keep industry moving.
Marek Lukaszczy is marketing manager for WEG Europe and Middle East
- Maintenance sector digitalisation
- WEG acquires industrial electric motors and generators business from Regal Rexnord
- IE3-compliant switchgears
- Growth or sustainability?
- Hazardous area motors no longer exempt
- Updated motor portfolio
- IE6 – unlocking efficiency in process industries
- WEG to launch latest VSD
- Increased energy efficiency & connectivity
- Safely advancing hydrogen technologies
- IO-LInk Now Included
- As Long As The Wind Blows
- CONDITION MONITORING FOR THE COMMON MAN
- Breakdown Avoided Thanks To Condition Monitoring
- "Try & Buy" Offer For Thermal Imaging Camera
- New generation condition monitoring
- Diagnostics from a distance
- Power plant protection
- Real-time monitoring
- Cost-effective protection for smaller machinery