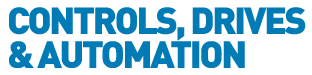
![]() |
Charlotte Stonestreet
Managing Editor |
Home> | MACHINE BUILDING & ENGINEERING | >3D Printing & Prototyping | >Manufacturing the future with robotic LFAM |
Editor's Pick
Manufacturing the future with robotic LFAM
16 January 2025
Violetta Nespolo provides an overview of key Large-Format Additive Manufacturing (LFAM) application areas for OEMs and the related benefits

As competition among manufacturers continues to grow, more digitalised and automated approaches are being adopted through the addition of robotics and AI to their manufacturing processes. These industry 4.0 technologies are transforming manufacturers’ value chains by offering greater flexibility, improved efficiency, and cost savings. These benefits span industries, with key industrial sectors such as automotive, aerospace, energy, and marine, adopting them for applications such as custom production moulds and tools, lightweighting finished parts, minimising waste, and reducing lead times.
One rapidly emerging technology driving this shift is 3D printing, more specifically Large-Format Additive Manufacturing (LFAM) combined with robotics. Yet, many companies hesitate to integrate these innovations, uncertain of where to begin, and which applications best benefit their business.
Practical Uses of LFAM
It is through industrial applications that the main benefits of robotic LFAM are best demonstrated, including design flexibility, minimised material waste, shortened production times, enhanced sustainability, and reliability.
For example, in aerospace and railways, composite 3D printing is used to produce large-scale parts, from lightweight and strong cabin components for passenger rolling stock, to extremely precise functional mock-ups and tooling. This can include jigs and fixtures for trimming, milling, and assembly; tools for positioning and vacuum-assisted drilling of airplane fuselage panels; master moluds for composite glass or carbon fiber parts; inspection fixtures for checking part precision; and cold lamination tools for aircraft fuselage maintenance.
In the automotive industry, LFAM is revolutionising the production of large, monolithic, lightweight components such as body panels and tooling. These parts can be produced faster, more cost-effectively, and with a significantly smaller environmental footprint.
LFAM is also widely used in architecture and construction, for creating forms, structural components, façade elements, and partition panels. It enables on-demand production without moulds and reduces transportation needs through on-site manufacturing. The Heron AM system is often applied to produce indoor, modular setups and unique displays for office and commercial spaces, customised, large-scale walls and façade elements with complex shapes, promoting eco-friendly and efficient construction.
Advantages of LFAM robotic platforms
When integrated into industrial supply chains, LFAM robotic platforms offer manufacturers an unparalleled opportunity to streamline and optimise production processes. The modular configuration of these platforms provides exceptional versatility, allowing manufacturers to customise setups according to their specific needs. For example, with our Heron AM or Vipra AM platforms, different extruding or deposition heads can be paired with robotic arms of varying sizes to achieve specific manufacturing needs and achieve efficiencies specific to their production purposes.
3D printing with robotic systems enables the production of highly complex, custom-designed parts with drastic reduction of waste and inefficiencies. These systems can deliver remarkable speed, precision, and flexibility. The use of smart manufacturing solutions such as sensors and IoT technologies that monitor and optimise the production data and 3D printing process as a whole enhances the LFAM robotic platforms’ performances. Core Manufacturing Benefits of Robotic LFAM
One benefit of LFAM is that it reduces production costs by eliminating the need for costly moulds, tooling, and labor-intensive assembly processes. Pairing LFAM with robotic systems automates workflows, cutting labor costs and speeding up time-to-market of finished parts. The ability to produce short-run or custom parts, which would be prohibitively expensive using traditional methods, becomes highly feasible with LFAM.
Manufacturers can also scale production seamlessly without the need for retooling or reconfiguring machinery when using LFAM. This is particularly advantageous in industries like aerospace and automotive, where custom designs and large components are common. The flexibility of LFAM robotic platforms enables companies to switch between different product lines or custom orders with zero to minimal downtime.
Additionally, LFAM enables the creation of complex, lightweight designs that are also strong and durable, particularly valuable in aerospace and automotive sectors. This level of customisation provides a significant competitive advantage in markets that demand unique, tailor-made products.
LFAM also minimises waste significantly compared to traditional manufacturing processes, which align with many manufacturers' sustainability goals. If this is a priority, it is worth looking into pellet-form recycled and high-performance materials, including thermoplastics and composites. This reduces material costs, and, by printing parts net shape, waste is cut drastically, lowering the overall use of raw materials and environmental impact of production.
The future of robotic LFAM
As awareness of its core benefits grows, an increasing number of OEMs are adopting robotic additive manufacturing to streamline production and expand the portfolio of applications and end parts they can achieve. The industry continues to introduce advanced solutions capable of producing composite and advanced material parts more sustainably, cost-effectively, and with greater design flexibility. For early adopters, these unique capabilities have become powerful business assets, driving cost savings, operational efficiency, and the creation of new revenue streams.
Violetta Nespolo is chief marketing and strategy officer at Caracol AM
- Robot disinfects 68,000 square feet in just 20 minutes
- KC Movers on the move with eCapital
- Accelerating robotics from cloud to edge
- Emerson expands automation portfolio with Afag
- Hybrid platform offers affordable additive manufacturing
- Eco-friendly electric valve actuator
- Septentrio starts mass production of GNSS module
- The hidden impact of harmonics
- Final call for women entrepreneurs in STEM to apply for grant
- Technology to help contain threat of Covid-19