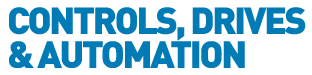
![]() |
Charlotte Stonestreet
Managing Editor |
Home> | MACHINE BUILDING & ENGINEERING | >3D Printing & Prototyping | >Printing the future with 3D technology |
Industry Update
Printing the future with 3D technology
11 June 2015
3D printing has come a long way since it was first introduced almost 30 years ago. The technology has significantly moved away from the scientific world and basic 3D objects to creating intricate designs for the fashion, automotive, medical and industrial automation sectors, says Rob Dumayne, director at igus
With increasing adoption and more people understanding the potential of 3D printing, the technology is set to revolutionise manufacturing – perhaps in the not too far distant future items will no longer be manufactured in remote factories and shipped thousands of miles to the buyer, instead an STL file of the 3D product is simply downloaded and printed at home.
The Government is keen to encourage the use of 3D printers in STEM and D&T teaching – the ultimate aim being every school and college having a 3D printer. Proof that 3D printing really is moving away from just prototyping is the recent news of a ratcheting socket spanner being printed by astronauts in the International Space Station. The spanner was printed using instructions sent to the astronauts via an e-mail – the first time hardware has ever been e-mailed into space.
Printer options
Wanting to print 3D components is something desired by all, but what is the best 3D printer available in the market today? With many options available, and prices starting from as little as £500, there are many things to look out for before investing in one, such as print size, speed, resolution and tolerance. Print speed and quality have a contrary relationship: the faster the speed, the lower the quality of the print and vice versa. Other factors to consider are: the layer height which is the vertical size of each layer of filament – the smaller the layer height the better the resolution, and also the printer tolerance which refers to the accuracy with which a printer can extrude the filament – a smaller tolerance indicates a more accurate print.
The next key factor to consider when printing 3D components is the material used. The majority of 3D printers today use a technology called fused filament fabrication (FFF), and use materials such as PLA (Polylactic Acid) and ABS (Acrylonitrile butadiene styrene). The plastic filaments of today make beautiful models to conceptualise a shape or prototypes that can be used to check whether a design will work but more robust materials that have structural properties, such as resistance to wear, temperature and abrasion, are needed.
In order to meet these high demands as well as enable engineers to print real workable parts used in motion applications, such as in bearing locations, igus has developed a tribo-polymer filament that is up to 50 times more resistant to wear and abrasion than ABS and PLA. The advantage of this filament is that it is made up of the self-lubricating material iglidur, and is available in two versions in two different diameters; iglidur I170 and iglidur I180. Both printer filaments are available in diameters of 1.75mm and 3.00mm.
Full potential
There is still a long way to go before the technology realises its full potential; developing materials with more structural properties is only one of the many steps that lie ahead. However, 3D printing is changing the way manufacturers operate as the technology can have a huge impact on everything from the design process to production, storage and recycling.
The technology allows engineers to produce one-off or small-batch components for more complex designs and move quickly from the test stage to a working prototype or even a replacement part. Additionally, warehousing and inventory costs can be reduced significantly too as spare parts can be stored digitally and created when required, removing the requirement for transporting the components to various remote sites.
Key Points
- With prices starting from as little as £500, there are many things to look out for before investing in a 3D printer
- The majority of 3D printers today use fused filament fabrication (FFF) technology, and use materials such as PLA and ABS
- igus has developed a tribo-polymer filament that is up to 50 times more resistant to wear and abrasion than ABS and PLA
- Eliminating bearing failure at low temperatures
- Cabling for robotic manufacturing
- Sustainable plain bearing materials
- ESD-certified dress pack for industrial robots
- Low cost roller energy chain and guiding trough
- Two-component injection-moulded bearings
- Direct drive robotic arms
- igus develops smart plastics app for FANUC FIELD system
- Engineered escapism
- Chainflex guarantee club